-
-
News
News Highlights
- Books
Featured Books
- design007 Magazine
Latest Issues
Current IssueAll About That Route
Most designers favor manual routing, but today's interactive autorouters may be changing designers' minds by allowing users more direct control. In this issue, our expert contributors discuss a variety of manual and autorouting strategies.
Creating the Ideal Data Package
Why is it so difficult to create the ideal data package? Many of these simple errors can be alleviated by paying attention to detail—and knowing what issues to look out for. So, this month, our experts weigh in on the best practices for creating the ideal design data package for your design.
Designing Through the Noise
Our experts discuss the constantly evolving world of RF design, including the many tradeoffs, material considerations, and design tips and techniques that designers and design engineers need to know to succeed in this high-frequency realm.
- Articles
- Columns
- Links
- Media kit
||| MENU - design007 Magazine
DFM 101: Cost Driver Summary
June 8, 2023 | Anaya Vardya, American Standard CircuitsEstimated reading time: 1 minute
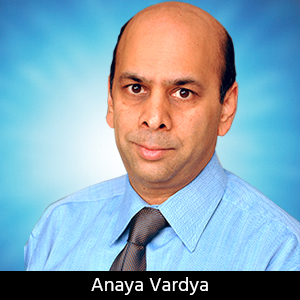
Introduction
One of the biggest challenges facing PCB designers is in not understanding the cost drivers in the PCB manufacturing process. We will wrap up this DFM series with a summary of cost drivers that impact delivery, quality, and reliability. It is categorized by low-, medium-, and high-cost adders.
Low-cost Adders (< 10% board cost)
Complex routing and scoring mean a small increase in process time, but a process is still required which will be driven by NC programming; it may limit tool life as a function of diameter. Thicker or thinner PWBs (>0.093", <0.030") means a material cost variation but it is minimal. Via plug or button print requires a small process change to the screen-print mask dot.
Medium-cost Adders (10–25%)
Regarding drilled hole quantity, there is a cost adder for high-density design-driven hole count and process time. With smaller drilled hole size, the small drill diameter (<0.010") limits throughput and stack height.
Embedded resistors with Ohmega/Gould technology will need additional core testing and finished board verification. Non-FR-4 materials, like PTFEs, can be 10 to 20 times the FR-4 cost, and material cost is generally 25–50% of the board cost. Edge plating will have additional processes required prior to plating.
To read this entire article, which appeared in the May 2023 issue of Design007 Magazine, click here.
Suggested Items
SMT007 Magazine July—What’s Your Competitive Sweet Spot?
07/01/2025 | I-Connect007 Editorial TeamAre you in a niche that’s growing or shrinking? Is it time to reassess and refocus? We spotlight companies thriving by redefining or reinforcing their niche—what are their insights? In the July 2025 issue of SMT007 Magazine, we spotlight companies thriving by redefining or reinforcing their niche and offer insights to help you evaluate your own.
Smarter Machines Use AOI to Transform PCB Inspections
06/30/2025 | Marcy LaRont, PCB007 MagazineAs automated optical inspection (AOI) evolves from traditional end-of-process inspections to proactive, in-line solutions, the integration of AI and machine learning is revolutionizing defect reduction and enhancing yields, marking a pivotal shift in how quality is managed in manufacturing.
Magnalytix and Foresite to Host Technical Webinar on SIR Testing and Functional Reliability
06/26/2025 | MAGNALYTIXMagnalytix, in collaboration with Foresite Inc., is pleased to announce an upcoming one-hour Webinar Workshop titled “Comparing SIR IPC B-52 to Umpire 41 Functional & SIR Test Method.” This session will be held on July 24, 2025, and is open to professionals in electronics manufacturing, reliability engineering, and process development seeking insights into new testing standards for climatic reliability.
The Death of the Microsection
06/26/2025 | Bob Neves, Reliability Assessment Solutions, Inc.I got my start out of college grinding and polishing PCB microsections. My thumbs are a bit arthritic today because of the experience (microsection grinders know what I mean). Back then, via structures were rather large, and getting to the center in six steps of grinding and polishing was easy compared to what my team has been doing recently at the lab.
Specially Developed for Laser Plastic Welding from LPKF
06/25/2025 | LPKFLPKF introduces TherMoPro, a thermographic analysis system specifically developed for laser plastic welding that transforms thermal data into concrete actionable insights. Through automated capture, evaluation, and interpretation of surface temperature patterns immediately after welding, the system provides unprecedented process transparency that correlates with product joining quality and long-term product stability.