-
- News
- Books
Featured Books
- smt007 Magazine
Latest Issues
Current IssueSoldering Technologies
Soldering is the heartbeat of assembly, and new developments are taking place to match the rest of the innovation in electronics. There are tried-and-true technologies for soldering. But new challenges in packaging, materials, and sustainability may be putting this key step in flux.
The Rise of Data
Analytics is a given in this industry, but the threshold is changing. If you think you're too small to invest in analytics, you may need to reconsider. So how do you do analytics better? What are the new tools, and how do you get started?
Counterfeit Concerns
The distribution of counterfeit parts has become much more sophisticated in the past decade, and there's no reason to believe that trend is going to be stopping any time soon. What might crop up in the near future?
- Articles
- Columns
Search Console
- Links
- Media kit
||| MENU - smt007 Magazine
Book Excerpt: 'The Printed Circuit Assembler’s Guide to...Process Control'
July 26, 2023 | I-Connect007Estimated reading time: 2 minutes
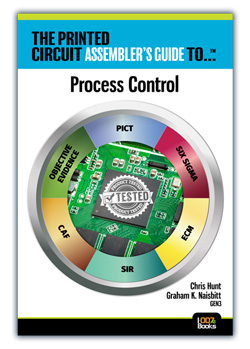
Introduction: The Printed Circuit Assembler’s Guide to...Process Control, a new book from Gen3 Systems.
An electronic assembly, by definition, has a circuit with current flowing. If by corrosion that circuit is changed, open circuit or short circuit, then the assembly will most likely be non-functional and will have failed. Dendrites are fragile metal filaments that can easily fuse when completing a circuit. Hence, an intermittent fault is observed. Continued exposure to the stress environment will cause the dendrite to regrow and cause another fault, and then fuse again. This process can repeat itself many times and, hence, many intermittent faults can be observed. Dendrites are the most common cause of No Fault Found; their intermittent nature tends to allow circuits to perform as normal, with interrupts that are not easily picked up by field return engineers who classify the product as NFF. Only when a dendrite forms a strong permanent short can it be discovered.
Susceptibility to ECM is contingent on harmful residues being present on the circuit assembly, along with other environmental factors. The creation of a water layer is a key step in ECM; this can be a sub-micron adsorbed layer, or a significantly thicker layer caused by condensation.
Figure 2.1: This visualisation (top) depicts condensation on a BGA. Release of organic acids into solution from flux residues (bottom). (Source: Mike Cummings)
Figure 2.1 depicts condensation droplets forming on the top surface of a component. As the condensation builds, at some point it will spill over the edge and then wick under the component. The right-hand images depict a flux residue encapsulating weak organic acids (WOA). When the residue is exposed to water, the WOA will dissolve into the liquid and are then available to support an electrical current. Figure 2.2 shows schematically the chemical processes occurring in ECM.
Figure 2.2: ECM processes. (Source: Mike Cummings)
Figure 2.2 depicts a condensed water layer under a BGA. Within this layer, WOA ions have been produced from flux residues. These ions migrate to the appropriate electrode supporting current flow. At the anode, anions release their charge where typically a cation is formed—in this case, a charged metallic ion. This is a corrosion process taking place at the anode. The cation migrates to the cathode, where it gives up its charge, depositing as a metal, which commonly grows as a dendrite. The figure also depicts diffusion processes and the creation of a double layer at the cathode.
The challenge, therefore, is to create a test that measures this electrical failure, where the causation has been corrosion. Such a test exists, and is the well-known SIR test, which measures resistance between electrodes. By using a SIR pattern, there is a geometric amplification of the resistance change, as well as an increased opportunity to detect a corrosion event. Within a single test assembly, the SIR test can be easily set up to provide data on specific component types. As we will see, the SIR test is the only test that truly provides objective evidence (OE).
Continue reading this book by visiting our library here.
Suggested Items
IPC Announces Two New Courses to Enhance Electronics Manufacturing Excellence
12/03/2024 | IPCIPC is excited to announce the launch of two new courses designed to optimize electronics manufacturing processes: "Ensuring Excellence: IPC-J-STD-001 Process Optimization" and "Ensuring Excellence: IPC-A-610 Process Optimization."
Absolute EMS Enters Strategic Partnership with PTEC Solutions to Enhance End-to-End Electronics Manufacturing Capabilities
11/27/2024 | PTEC SolutionsAbsolute EMS, Inc., a six-time award-winning provider of fast turnaround, turnkey contract electronic manufacturing services (EMS), is excited to announce a new partnership with PTEC Solutions, a highly respected provider specializing in design, cable and mechanical assembly services.
Indium Technical Expert to Present at SiP Conference China
11/25/2024 | Indium CorporationIndium Corporation Senior Area Technical Manager for East China Leo Hu is scheduled to deliver a presentation on Low-Temperature Solder Material in Semiconductor Packaging Applications at SiP China Conference 2024 on November 27 in Suzhou, China.
CIL Installs Third Volume Auto SMT Line with In-Line 3D AOI at BP2 Facility
11/25/2024 | CILIn early November 2024, CIL completed the installation of its third volume SMT PCBA assembly line at its BP2 Semiconductor Packaging facility
Real Time with... electronica 2024: SPEA's AI Integration—Innovations in Test Equipment
11/25/2024 | Real Time with... electronicaIn this interview from electronica 2024, Pete Starkey speaks with Andrea Furnari, VP of Electronic Test Products Business Unit for SPEA. The discussion revolves around AI integration in test equipment, trends in substrate materials, and SPEA's focus on R&D.