-
- News
- Books
Featured Books
- pcb007 Magazine
Latest Issues
Current IssueIn Pursuit of Perfection: Defect Reduction
For bare PCB board fabrication, defect reduction is a critical aspect of a company's bottom line profitability. In this issue, we examine how imaging, etching, and plating processes can provide information and insight into reducing defects and increasing yields.
Voices of the Industry
We take the pulse of the PCB industry by sharing insights from leading fabricators and suppliers in this month's issue. We've gathered their thoughts on the new U.S. administration, spending, the war in Ukraine, and their most pressing needs. It’s an eye-opening and enlightening look behind the curtain.
The Essential Guide to Surface Finishes
We go back to basics this month with a recount of a little history, and look forward to addressing the many challenges that high density, high frequency, adhesion, SI, and corrosion concerns for harsh environments bring to the fore. We compare and contrast surface finishes by type and application, take a hard look at the many iterations of gold plating, and address palladium as a surface finish.
- Articles
- Columns
Search Console
- Links
- Media kit
||| MENU - pcb007 Magazine
Estimated reading time: 3 minutes
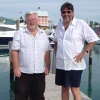
PCB 101: Coefficient of Thermal Expansion
CTE is one of the phrases we use daily in the printed circuit business. But how many of us really know what CTE is and how it affects a circuit board?
CTE stands for coefficient of thermal expansion. It describes a number or percentage relating to how much a PCB expands as it is heated or cooled. Every material in the world expands or contracts with a change in temperature; for example, your house is actually a few inches larger in the summer than it is in the winter.
A few materials change for the negative, so the part shrinks when it experiences a rise in temperature. But most items expand by a small percentage as they heat up. The expansion is expressed in parts per million per degree Celsius (ppm/°C).
A PCB will expand in length or width by 14 parts per million per Celsius degree. This means that if a PCB were 1 million inches long, it would expand by 14 inches for every Celsius degree of temperature increase.
A typical FR-4 laminate has a CTE of 14 to 17 ppm/°C. This is fine, until we consider that the large silicon chip packages we solder onto a PCB have an expansion rate of only 6 ppm/°C. The difference in expansion rate is enough--especially on the larger BGA packages--that when the PCB and chip are heated up, the PCB will expand more than the chip package and shear the solder joins off the chip.
So, we in the PCB business talk of CTE and fabricators often take low CTE orders. But how does CTE affect the board and the way we design and fabricate them?
When selecting the laminate, we look at an alphabet of specifications: Tg, Dk and Df, to name a few. All are important and all interact. When we select laminates in an attempt to reduce CTE, we notice many of the FR-4 brands have similar CTE values, and most are far too high (14 ppm/°C) to be used with large silicon packaging. This means we need to look at a different method to control CTE by designing the layup for metal, Kevlar and Aramid cores.
These three low-CTE materials are often used with FR-4 outer layers to create low-CTE boards. The metal cores used are copper-invar-copper (CIC) and copper-molybdenum-copper (CMC), typically 6 mils thick. The copper on the outside of the metal core allows us to laminate onto the normal FR-4 prepregs and cores.
The two most widely used metal cores are CIC and CMC, which feature CTEs of 8 ppm/°C and 6 ppm/°C, respectively. The metal core is used to anchor the expansion of the FR-4 outer layers and provide an overall CTE of 12 ppm/°C and 9 ppm/°C, respectively.
Similarly, we can use Kevlar Thermount or a Aramid laminate as a core material; their low CTE of 7 to 9 ppm/°C used with standard FR-4 outer layers will yield a CTE of 12 ppm/°C. The low CTE laminate cores replace the typical FR-4 core in multilayer production. Interestingly, the actual Kevlar fibers have a negative CTE, while the epoxy used to glue them together has a positive CTE, resulting in a low CTE laminate.
As low-CTE laminates go, the most expensive are metal cores, followed by Kevlar and Aramid fiber laminates. In the past, the Arlon Kevlar Thermount was hard to obtain, but new production efforts have increased its availability. All of the low-CTE cores are hard to drill and process, but this is the only way to achieve the desired 6-9 CTE required by larger silicon packaging.
In addition to the control of CTE, metal core PCBs can be used for high-power heat transfer improvements. Remember that metal expands with significantly more force than an FR-4 layer; the metal cores control the CTE, changing the FR-4 layers more than Kevlar can.
In a future column, we'll discuss Young's modulus, which measures the amount of force a laminate possesses as it expands.
Bob Tarzwell is CEO and founder of DMR Ltd. He can be reached at rtarzwell@megadawn.com.
More Columns from Bob and Me
Controlled Impedance: A Real-World Look at the PCB SideBob and Me: The Key to Increasing Quality - Bribe Your Employees
Bob and Me: Tarzwell's First--and Last--Lean Meeting
Bob and Me: A PCB Potpourri
Bob and Me: Spacing is Irrelevant Below 270 Volts
The Bleeding Edge: Serious as a Heart Attack
PCB101: Fabricating High-Voltage Boards
New Column: PCB 101