-
-
News
News Highlights
- Books
Featured Books
- design007 Magazine
Latest Issues
Current IssueAll About That Route
Most designers favor manual routing, but today's interactive autorouters may be changing designers' minds by allowing users more direct control. In this issue, our expert contributors discuss a variety of manual and autorouting strategies.
Creating the Ideal Data Package
Why is it so difficult to create the ideal data package? Many of these simple errors can be alleviated by paying attention to detail—and knowing what issues to look out for. So, this month, our experts weigh in on the best practices for creating the ideal design data package for your design.
Designing Through the Noise
Our experts discuss the constantly evolving world of RF design, including the many tradeoffs, material considerations, and design tips and techniques that designers and design engineers need to know to succeed in this high-frequency realm.
- Articles
- Columns
- Links
- Media kit
||| MENU - design007 Magazine
Effective Characteristic Impedance
March 4, 2015 | Kirk Fabbri, KSPT Engineering ConsultingEstimated reading time: Less than a minute
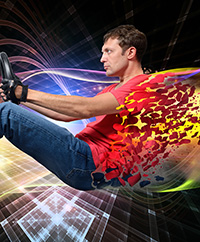
In a typical interconnect, there lie multiple places where capacitance plays a factor in the signal integrity. This includes the driver and receiver output/input capacitance, as well as the packages, vias, and the transmission lines. Failing to optimize these parameters can often lead to unwanted reflections, excessive radiated and or conducted emissions, and sometimes failure of components and systems.
Reflections can occur anytime there is an impedance mismatch on the line. Sources of mismatches are plentiful and include trace width changes, vias, stubs, reference plane changes, and even the so-called fiber weave effect. In this case, a trace can encounter a different dielectric constant depending on whether it is routed over glass or the epoxy resin in the dielectric material.
In this investigation, it is the capacitive contribution of the different components that are of interest, and how they affect the characteristic impedance the driver sees.
To read the rest of this article, click here.
Suggested Items
Count On Tools Recognizes Donna Orr’s Ongoing Leadership and Impact Across 27+ Years
06/26/2025 | Count On ToolsCount On Tools, Inc. (COT), a leading provider of precision components and SMT spare parts, is proud to recognize Donna Orr, Executive Manager, for her continued dedication and leadership as she marks more than 27 years with the company.
A Record Year for the 75th Annual IEEE Electronic Components and Technology Conference (ECTC)
06/26/2025 | ECTCThe 75th annual 2025 IEEE Electronic Components and Technology Conference (ECTC), held at the Gaylord Texan Resort & Convention Center here May 27-30, had record attendance, a record number of paper submissions/presentations, record international and student participation, and a record number of exhibitors in a sold-out exhibition hall:
The Death of the Microsection
06/26/2025 | Bob Neves, Reliability Assessment Solutions, Inc.I got my start out of college grinding and polishing PCB microsections. My thumbs are a bit arthritic today because of the experience (microsection grinders know what I mean). Back then, via structures were rather large, and getting to the center in six steps of grinding and polishing was easy compared to what my team has been doing recently at the lab.
Specially Developed for Laser Plastic Welding from LPKF
06/25/2025 | LPKFLPKF introduces TherMoPro, a thermographic analysis system specifically developed for laser plastic welding that transforms thermal data into concrete actionable insights. Through automated capture, evaluation, and interpretation of surface temperature patterns immediately after welding, the system provides unprecedented process transparency that correlates with product joining quality and long-term product stability.
Fresh PCB Concepts: Assembly Challenges with Micro Components and Standard Solder Mask Practices
06/26/2025 | Team NCAB -- Column: Fresh PCB ConceptsMicro components have redefined what is possible in PCB design. With package sizes like 01005 and 0201 becoming more common in high-density layouts, designers are now expected to pack more performance into smaller spaces than ever before. While these advancements support miniaturization and functionality, they introduce new assembly challenges, particularly with traditional solder mask and legend application processes.