-
- News
- Books
Featured Books
- pcb007 Magazine
Latest Issues
Current IssueInventing the Future with SEL
Two years after launching its state-of-the-art PCB facility, SEL shares lessons in vision, execution, and innovation, plus insights from industry icons and technology leaders shaping the future of PCB fabrication.
Sales: From Pitch to PO
From the first cold call to finally receiving that first purchase order, the July PCB007 Magazine breaks down some critical parts of the sales stack. To up your sales game, read on!
The Hole Truth: Via Integrity in an HDI World
From the drilled hole to registration across multiple sequential lamination cycles, to the quality of your copper plating, via reliability in an HDI world is becoming an ever-greater challenge. This month we look at “The Hole Truth,” from creating the “perfect” via to how you can assure via quality and reliability, the first time, every time.
- Articles
- Columns
- Links
- Media kit
||| MENU - pcb007 Magazine
Understanding DFM and its Role in PCB Layout
April 14, 2015 | Rick Almeida, Downstream TechnologiesEstimated reading time: 2 minutes
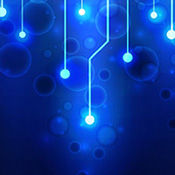
DFM, DRC, DFF, DFA, DFwhat? These are all terms used daily in the PCB design world regarding manufacturing analysis, and they are often used interchangeably. But what exactly is DFM and why is it such an important, but often ignored aspect of the PCB design process?
Let’s start by clarifying some terms. DFM is short for “design for manufacturability.” It is the process of arranging a PCB layout topology to mitigate problems that could be encountered during the PCB fabrication and assembly processes required to manufacture an electronic system. Addressing fabrication issues is what’s known as design for fabrication (DFF), and addressing assembly issues during design is known as design for assembly (DFA). The two together mostly make up DFM analysis—mostly.
In many cases, the term DRC, which stands for design rule checking, is also used interchangeably with DFM and creates further confusion. That’s understandable, because DRC issues detected in manufacturing can indeed have a direct impact on the manufacturability of a PCB. However, DRC is markedly different from DFF and DFA. Think of DRC as a hard pass/fail detection of a problem in a PCB. Either a problem exists or it doesn’t. In engineering, DRC is used to ensure that PCB layout connectivity accurately reflects the connectivity defined in a board’s associated schematic diagram. But connectivity is only one aspect of DRC. The “R” stands for rules. The rules are used largely to define the minimum spacing allowed between various PCB objects for the entire PCB or for individual layers, nets or areas on the PCB. In engineering, the spacing may have direct impact on circuit performance. In manufacturing, spacing may play a pivotal role in the ability to fabricate or assemble a PCB. As a result, DRC becomes a subset of DFM, but only if the rules used reflect a manufacturer’s requirements for spacing. Otherwise, DRC is used solely for electrical verification.
DFM’s two primary components, DFF and DFA, are more nuanced than DRC. While DRC detects very specific discrepancies from the intended interconnect, DFM identifies issues in the PCB topology that have the potential to create manufacturing problems. What’s more, a DRC defect will be present in every copy of the PCB built, so if there is a short missed in DRC, every PCB will contain the short, no matter how many PCBs are produced. By contrast, if the same PCB quantities contain DFM issues, problems may only manifest in some of the PCBs while others perform correctly as expected.
For example, a PCB layout containing very thin pieces of copper created in the design tool by rule would be correct per the schematic. And if spaced properly it would pass DRC. However, that same sliver, being so thin, could potentially detach on the physical PCB and inadvertently connect itself to other copper elements during assembly, thus creating shorts on some PCBs but not on others. So, the sliver would pass DRC verification, but in real-world manufacturing the sliver could cause some PCBs to fail. Without DFM, this problem would go on undetected and would result in scrap or rework.
This article originally appeared in the March 2015 issue of The PCB Design Magazine. To read this article in its entirety, click here.
Testimonial
"The I-Connect007 team is outstanding—kind, responsive, and a true marketing partner. Their design team created fresh, eye-catching ads, and their editorial support polished our content to let our brand shine. Thank you all! "
Sweeney Ng - CEE PCBSuggested Items
The Government Circuit: Navigating New Trade Headwinds and New Partnerships
08/25/2025 | Chris Mitchell -- Column: The Government CircuitAs global trade winds continue to howl, the electronics manufacturing industry finds itself at a critical juncture. After months of warnings, the U.S. Government has implemented a broad array of tariff increases, with fresh duties hitting copper-based products, semiconductors, and imports from many nations. On the positive side, tentative trade agreements with Europe, China, Japan, and other nations are providing at least some clarity and counterbalance.
How Good Design Enables Sustainable PCBs
08/21/2025 | Gerry Partida, Summit InterconnectSustainability has become a key focus for PCB companies seeking to reduce waste, conserve energy, and optimize resources. While many discussions on sustainability center around materials or energy-efficient processes, PCB design is an often overlooked factor that lies at the heart of manufacturing. Good design practices, especially those based on established IPC standards, play a central role in enabling sustainable PCB production. By ensuring designs are manufacturable and reliable, engineers can significantly reduce the environmental impact of their products.
50% Copper Tariffs, 100% Chip Uncertainty, and a Truce
08/19/2025 | Andy Shaughnessy, I-Connect007If you’re like me, tariffs were not on your radar screen until a few months ago, but now political rhetoric has turned to presidential action. Tariffs are front-page news with major developments coming directly from the Oval Office. These are not typical times. President Donald Trump campaigned on tariff reform, and he’s now busy revamping America’s tariff policy.
Global PCB Connections: Understanding the General Fabrication Process—A Designer’s Hidden Advantage
08/14/2025 | Markus Voeltz -- Column: Global PCB ConnectionsDesigners don’t need to become fabricators, but understanding the basics of PCB fabrication can save you time, money, and frustration. The more you understand what’s happening on the shop floor, the better you’ll be able to prevent downstream issues. As you move into more advanced designs like HDI, flex circuits, stacked vias, and embedded components, this foundational knowledge becomes even more critical. Remember: the fabricator is your partner.
MKS’ Atotech to Participate in IPCA Electronics Expo 2025
08/11/2025 | AtotechMKS Inc., a global provider of enabling technologies that transform our world, announced that its strategic brands ESI® (laser systems) and Atotech® (process chemicals, equipment, software, and services) will showcase their latest range of leading manufacturing solutions for printed circuit board (PCB) and package substrate manufacturing at the upcoming 17th IPCA Show to be held at Pragati Maidan, New Delhi from August 21-23, 2025.