-
-
News
News Highlights
- Books
Featured Books
- smt007 Magazine
Latest Issues
Current IssueWhat's Your Sweet Spot?
Are you in a niche that’s growing or shrinking? Is it time to reassess and refocus? We spotlight companies thriving by redefining or reinforcing their niche. What are their insights?
Moving Forward With Confidence
In this issue, we focus on sales and quoting, workforce training, new IPC leadership in the U.S. and Canada, the effects of tariffs, CFX standards, and much more—all designed to provide perspective as you move through the cloud bank of today's shifting economic market.
Intelligent Test and Inspection
Are you ready to explore the cutting-edge advancements shaping the electronics manufacturing industry? The May 2025 issue of SMT007 Magazine is packed with insights, innovations, and expert perspectives that you won’t want to miss.
- Articles
- Columns
- Links
- Media kit
||| MENU - smt007 Magazine
Reliability Assessment of No-clean and Water-soluble Solder Pastes, Part II
May 6, 2015 | Emmanuelle Guéné and Steven Teh, Inventec Performance ChemicalsEstimated reading time: 2 minutes
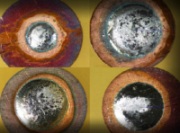
Note: Part 1 of this article published in the March 2014 issue of SMT Magazine, available here.
Twenty-five years ago, solder paste residues had to be cleaned after reflow due to their corrosive nature: two ways of cleaning were available, either with solvent or by using water, with or without detergent. Now, the assembly world is mainly no-clean: paste formulation is safer in terms of chemical reliability and process costs are reduced without cleaning. However, some applications (i.e., military, aerospace, high-frequency, and semiconductor) require a perfect elimination of the residue after reflow. Several options can achieve this result: a no-clean paste which allows residue to be removed with the most suitable cleaning method, or a paste designed to be cleaned, such as a water-soluble solder paste.
Water-soluble solder pastes generally show great wettability because of their strong activation but they are also known to have shorter stencil life and to be more sensitive to working conditions as temperature and humidity, compared to the no-clean pastes. Additionally, with the components stand-off getting smaller and smaller, washing residues with water only is more and more challenging due to its high surface tension: the addition of detergent becomes often necessary.
The purpose of this article is to highlight the differences between these two families of solder pastes to guide users in their choice. This will be achieved through the comparison of several recent water-soluble and no-clean formulations as far as reliability is concerned. First, the printing quality will be evaluated (viscosity, tack, cold slump, printing speed according to pressure, stencil life, idle time, printing consistency). Next, the reflow properties will be compared (hot slump, solderballing, reflow process window, wetting ability on different finishes).
Finally, the residue cleanability will be assessed. The IPC SIR will be also done to conclude the study. Both standardized tests and production tests will be used to evaluate the performance of these two kinds of solder pastes.
Introduction
Six lead-free pastes were extensively studied, three being water-soluble and three being no-clean. The first part of the study focused on printing performance. The pastes were characterized using standardized tests and internally developed tests: dynamic viscosity, tackiness, slump and solderballing. The influence of accelerated storage at elevated temperature, the influence of time and conditions between printing and reflow and the influence of continuous shear according to time were shown. The printing performances were also evaluated in a printer. Although the number of pastes studied was restricted, the water- soluble pastes generally yielded results below the no-clean pastes with more sensitivity to temperature and humidity, tendency to slump during preheat and narrower printing window. Water- soluble solder pastes must be stored, handled and used with more caution before reflow.
In the second part of the paper, the reflow properties will be compared: wettability, reflow process window, anti-graping properties. Finally the residue cleanability with water, then with water and detergents will be examined. The cleanliness will be assessed using visual inspection, ionic contamination and surface insulation resistance tests.
Editor's Note: This article originally appeared in the April issue of SMT Magazine.
Suggested Items
Silicon Mountain Contract Services Enhances SMT Capabilities with New HELLER Reflow Oven
07/17/2025 | Silicon Mountain Contract ServicesSilicon Mountain Contract Services, a leading provider of custom electronics manufacturing solutions, is proud to announce a significant upgrade to its SMT production capability with the addition of a HELLER 2043 MK5 10‑zone reflow oven to its Nampa facility.
Knocking Down the Bone Pile: Addressing End-of-life Component Solderability Issues, Part 4
07/16/2025 | Nash Bell -- Column: Knocking Down the Bone PileIn 1983, the Department of Defense identified that over 40% of military electronic system failures in the field were electrical, with approximately 50% attributed to poor solder connections. Investigations revealed that plated finishes, typically nickel or tin, were porous and non-intermetallic.
SHENMAO Strengthens Semiconductor Capabilities with Acquisition of PMTC
07/10/2025 | SHENMAOSHENMAO America, Inc. has announced the acquisition of Profound Material Technology Co., Ltd. (PMTC), a premier Taiwan-based manufacturer of high-performance solder balls for semiconductor packaging.
KYZEN to Highlight Understencil and PCB Cleaners at SMTA Querétaro Expo and Tech Forum
07/09/2025 | KYZEN'KYZEN, the global leader in innovative environmentally responsible cleaning chemistries, will exhibit at the SMTA Querétaro Expo & Tech Forum, scheduled to take place Thursday, July 24, at Centro de Congresos y Teatro Metropolitano de Querétaro.
Driving Innovation: Direct Imaging vs. Conventional Exposure
07/01/2025 | Simon Khesin -- Column: Driving InnovationMy first camera used Kodak film. I even experimented with developing photos in the bathroom, though I usually dropped the film off at a Kodak center and received the prints two weeks later, only to discover that some images were out of focus or poorly framed. Today, every smartphone contains a high-quality camera capable of producing stunning images instantly.