-
-
News
News Highlights
- Books
Featured Books
- smt007 Magazine
Latest Issues
Current IssueWhat's Your Sweet Spot?
Are you in a niche that’s growing or shrinking? Is it time to reassess and refocus? We spotlight companies thriving by redefining or reinforcing their niche. What are their insights?
Moving Forward With Confidence
In this issue, we focus on sales and quoting, workforce training, new IPC leadership in the U.S. and Canada, the effects of tariffs, CFX standards, and much more—all designed to provide perspective as you move through the cloud bank of today's shifting economic market.
Intelligent Test and Inspection
Are you ready to explore the cutting-edge advancements shaping the electronics manufacturing industry? The May 2025 issue of SMT007 Magazine is packed with insights, innovations, and expert perspectives that you won’t want to miss.
- Articles
- Columns
- Links
- Media kit
||| MENU - smt007 Magazine
Solder Jet Printing: Is It the Right Time?
May 11, 2015 | Barry Matties, I-Connect007Estimated reading time: 9 minutes
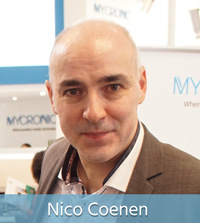
I stopped by the Mycronic booth at Nepcon China 2015 and spoke with Sales Director Nico Coenen. He updated me on the company's new solder jet printing system, a technology that Mycronic has been developing and pioneering for 10 years. The company now believes that now is the time for it to gain real traction. One thing is certain: solder jet printing certainly has advanced and could make a big difference in process and quality.
Barry Matties: Nico, what is Mycronic doing in jet printing?
Nico Coenen: Jet printing in general has been around a while in the industry, but we are unique in that we are pioneering solder-based jet printing. It's a very difficult media to jet.
I've been working for many dispense companies, so I know how challenging it is. Mycronic has developed a unique, patented technology to actually make this process quite mature. We’ve been running in production for about 10 years with this. We are starting to see some competition popping up, which is good, because that means there is more demand for the technology itself.
Matties: It validates what you're doing. What does your typical customer look like?
Coenen: Traditionally, the Mycronic customer would have small- to medium-batch sizes, a lot of changeovers during the day, and they would need a flexible production environment. I would say the first 300–350 systems typically went to these kinds of customers. There were a lot of military, aerospace, and medical customers.
However, we have recently seen a lot of interest from high-volume guys. Not to replace the screen printer, but to have an add-on tool. We have seen that doing fine pitch by itself is not the issue. Having fine pitch and larger components on the same board is where people get into more difficulties.
Typical mobile phone manufacturers have an add-on process where they do screen printing and then a dispense or jet process afterwards.
Matties: Is speed the roadblock for the volume customer?
Coenen: We have a speed issue for volume customers. Let's say a mobile phone today takes about 15 to 20 seconds, max. That's your cycle time. With a screen printer you can do that, no problem. For us, speed is dependent on board size and how many deposits we have to do, so there is quite a bit of variation.
Although we have cranked up the speed 50% from our previous model, we're still not in line with that kind of speed.
Matties: And that is where you need to be to compete with screen printing. Do you see a day when that might happen?
Coenen: Yes, there are people that really would like to have a stencil-free factory for a number of reasons.
Matties: If you go stencil-free you eliminate multiple steps to the process. Preparing the stencil, managing it, painting it—even ordering it.
Coenen: Yes. Basically we are software driven, so something like high-volume mobile phone manufacturing still will have some small variance. Some might have 32 memory, the other 64, and with a stencil, that is a physical change. With jet printing you can do any batch size, and then switch over to the other in seconds.
Matties: I take it your R&D team is focused on increasing speed and breaking the speed barrier? How many jets are in your printer currently?
Coenen: Currently there is one jet. There are options to do four heads in one system, or to go for a modular system where you have up to five. That's all on the table. It looks like we're heading in that direction so that we can offer any capability or any speed, and that would bring us into a whole different league.
Matties: One of the common defects that I hear about is head-in-pillow. Is there an advantage to solving that through a jet system?
Coenen: One of the great benefits of the jet system is that we put down exactly the amount of solder per component because we can program it by piece, by single path, etc. All our initial customers more or less bought this for quality improvements for head-in-pillow and solder balling, which are typical problems you have in the screen printing process.
Matties: What is the most prevalent problem that you see in that process?
Coenen: There are a few. We mentioned head-in-pillow and solder balling; another is handling QFP devices. These are challenging components. Besides that, there are new kinds of problems where you have cavities in boards, flex ridges, and all kinds of different combinations, which make traditional screen printing more complicated. One of the big advantages is that we don't touch. We shoot from a distance, so we're less sensitive to height variations, and so on. Basically, the software can shoot here at this height, or follow by laser, topography, etc.
The system itself has a large opportunity window. We have identified that there is going to be a huge focus on this technology going forward, because there are so many demands on the current technology.
Matties: What do you think is the limit for screen printing? What's the deciding factor where they say screen just isn't what we can use any more?
Coenen: At a certain point, let's say, if your screen is only going to be maybe 50 microns, it would go to 03015. There's only a certain amount of thickness that you can put down, such as 50 microns of solder, and there is a limit on what type of component you can add to that. Again, it's a combination.
There are solutions like step stencils and so on, but again there are some design limitations as to where you can put small components, big components and so on.
Matties: What is the important thing that you think the market should know about this technology? What have we left out?Page 1 of 2
Suggested Items
Silicon Mountain Contract Services Enhances SMT Capabilities with New HELLER Reflow Oven
07/17/2025 | Silicon Mountain Contract ServicesSilicon Mountain Contract Services, a leading provider of custom electronics manufacturing solutions, is proud to announce a significant upgrade to its SMT production capability with the addition of a HELLER 2043 MK5 10‑zone reflow oven to its Nampa facility.
Knocking Down the Bone Pile: Addressing End-of-life Component Solderability Issues, Part 4
07/16/2025 | Nash Bell -- Column: Knocking Down the Bone PileIn 1983, the Department of Defense identified that over 40% of military electronic system failures in the field were electrical, with approximately 50% attributed to poor solder connections. Investigations revealed that plated finishes, typically nickel or tin, were porous and non-intermetallic.
SHENMAO Strengthens Semiconductor Capabilities with Acquisition of PMTC
07/10/2025 | SHENMAOSHENMAO America, Inc. has announced the acquisition of Profound Material Technology Co., Ltd. (PMTC), a premier Taiwan-based manufacturer of high-performance solder balls for semiconductor packaging.
KYZEN to Highlight Understencil and PCB Cleaners at SMTA Querétaro Expo and Tech Forum
07/09/2025 | KYZEN'KYZEN, the global leader in innovative environmentally responsible cleaning chemistries, will exhibit at the SMTA Querétaro Expo & Tech Forum, scheduled to take place Thursday, July 24, at Centro de Congresos y Teatro Metropolitano de Querétaro.
Driving Innovation: Direct Imaging vs. Conventional Exposure
07/01/2025 | Simon Khesin -- Column: Driving InnovationMy first camera used Kodak film. I even experimented with developing photos in the bathroom, though I usually dropped the film off at a Kodak center and received the prints two weeks later, only to discover that some images were out of focus or poorly framed. Today, every smartphone contains a high-quality camera capable of producing stunning images instantly.