-
- News
- Books
Featured Books
- smt007 Magazine
Latest Issues
Current IssueThe Path Ahead
What are you paying the most attention to as we enter 2025? Find out what we learned when we asked that question. Join us as we explore five main themes in the new year.
Soldering Technologies
Soldering is the heartbeat of assembly, and new developments are taking place to match the rest of the innovation in electronics. There are tried-and-true technologies for soldering. But new challenges in packaging, materials, and sustainability may be putting this key step in flux.
The Rise of Data
Analytics is a given in this industry, but the threshold is changing. If you think you're too small to invest in analytics, you may need to reconsider. So how do you do analytics better? What are the new tools, and how do you get started?
- Articles
- Columns
Search Console
- Links
- Media kit
||| MENU - smt007 Magazine
Final Test Solution of WLCSP Devices
May 26, 2015 | Andreas Nagy, Xcerra Corp.Estimated reading time: 4 minutes
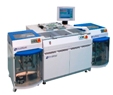
Wafer level chip scale package (WLCSP) devices are used because they offer low cost, small footprint packages that can be directly mounted into smartphones, tablet PCs and other mobile devices. Today, this packaging technology is also used in automotive applications. The manufacturers of mobile device applications are demanding lower defective parts per million (DPPM) from their suppliers of WLCSP devices, catching up with automotive standards.
Currently, the common back-end process flow for mobile WLCSP devices is a single or dual insertion test at wafer probe. With this flow, there is no testing performed after device singulation (wafer saw). The singulated devices are then sorted and picked from the film frame ring for final packaging into reel. Since there is no final test prior to tape and reel, this equipment typically needs to provide a 5-side device inspection to identify potential device damage from sawing. The inspection efforts are quite demanding, with defect recognition requirements in the range of only 10 to only 20 microns, resulting in frequent time and cost intense human interaction and support requirements. Remaining concerns of this inspection are potential functional damages to the device that cannot be identified with a visual inspection. The reason for this flow without a final test is that there has not been a cost effective way to handle singulated WLCSP devices in a high volume manufacturing environment.
In addition to the high visual inspection cost, the cost for bad quality resulting from the escaping devices with functional defects is a burden to the mobile industry that requires new solutions to overcome the shortcomings of this flow.
What are the key attributes and technical challenges of singulated WLCSP device handling with final test?
- Ultimately the final test of WLCSP must address the shortcomings of today’s probe test flow.
- Most critical are the brittle and touch sensitive edges and corners of the devices that could get damaged at any handling step. The reduction of handling steps is therefore mandatory for a successful solution.
- The support of tri-temp final test is required to also address the needs of automotive and industrial applications beyond the ambient and hottest requirements of mobility applications.
- High multi-site test capabilities of high pin count devices will require the control of high contact forces.
- Device pad pitch below 0.3mm will require high accurate device to contact site alignment.
- Improved touch efficiency versus wafer probe test would help to increase productivity and reduce cost.
- The final test results should be capable of virtually reconstituting a wafer test map that might be used for process optimizations in the front end.
A practical approach is to hold hundreds of singulated devices in an array formatted similarly to a device strip. By placing the singulated devices in such an array, a standard strip test handler can then be used to provide true final tri-temp test of WLCSP devices.
The device pad to contact alignment is a standard requirement for a strip handler. Auto vision alignment is therefore a standard feature that supports small pitch requirements.
The strip handler can index the device matrix along the contactor matrix with 100% touch efficiency. Good strip test handlers provide, as standard, very rigid plunger architectures and docking structures to support high parallel, high pin count test requirements. To ensure the highest contact yield optional plunge force measurements monitor the nominal contact force even at the smallest structural deflections.
The remaining task is to safely mount the device to such a strip like array. The technology has to ensure that no corner of the device is getting touched and needs to be able to register the devices very precisely in a defined matrix.
Simplifying backend final test processes
Xcerra has developed InCarrier, a patented sheet metal assembly with a mechanical clamping scheme that addresses all the described requirements. It is already in high volume production and several billion devices have been tested at tri-temp, and with up to 144 devices parallel.
The loading of the sensitive WLCSP is supported by a loading machine that is picking the devices from the wafer ring and placing them into the carrier. The devices are secured in small pockets of the carrier and no handling step of the multiple temperature insertions of the final test can cause any harm to them.
The tracing information from wafer position to strip position can be stored. The strip test handler test results are stored in electronic map files similar to wafer probe. A virtual wafer test map can therefore be reconstituted and used for process quality improvements in the front end.
After final test, the devices then get picked from the InCarrier right at the final packaging equipment. Optional 5S inspections can still be provided, but visual requirements can likely be relaxed to defect sizes that will not require intense human support.
The proposed process is not theory, but is already in high volume evaluation for WLCSP and in high volume production for standard packages. It is the first, and currently the only, cost effective final test solution for WLCSP in a high volume manufacturing environment provided. It may enable the elimination of probe test and could support the automation requirements of the backend final test process.
Author Information
Andreas Nagy is Senior Director Marketing Handler & Test Cell Innovation, at Xcerra Corp.
Suggested Items
The Training Connection LLC Opens Headquarters in Hunt Valley, MD, Offering Premier Technical Training Solutions
01/02/2025 | The Training Connection LLCThe Training Connection LLC (TTC-LLC) is excited to announce the grand opening of its headquarters in Hunt Valley, MD. Founded with the mission to enhance industry knowledge and equip professionals with essential technical skills, TTC-LLC provides top-tier training that enables success for professionals across a variety of industries.
TRI to Host Test and Inspection Technology Seminars
01/02/2025 | TRITest Research, Inc. (TRI) is proud to announce the 2025 Technology Seminars, which will feature Innovative Inspection Solutions, SPI, AOI, AXI, and ICT solutions at a series of technology seminars and product demos held in Taiwan, Shenzhen, and Suzhou.
TRI to Exhibit Advanced Test and Inspection at IPC APEX Expo 2025
01/01/2025 | TRITest Research, Inc. (TRI) will join the IPC APEX EXPO 2025 held at Anaheim Convention Center on March 18 – 20, 2025. Visit TRI at booth #2905 to experience TRI's latest test and inspection solutions for the electronics manufacturing Industry.
IPC: PCB Designers Invited to Attend PEDC-Pan-European Electronics Design Conference
12/30/2024 | IPCThe Pan-European Electronics Design Conference (PEDC), co-hosted by FED and IPC, will take place on January 29-30, 2025. This two-day conference, held in English, will bring together global PCB designers for a comprehensive exchange of ideas and insights on the latest trends and technologies in electronics design.
Kimball Electronics Thailand Namlee School
12/26/2024 | Kimball ElectronicsKimball Electronics Thailand (KETL) has continued its commitment to supporting education and community development in Thailand.