-
-
News
News Highlights
- Books
Featured Books
- smt007 Magazine
Latest Issues
Current IssueWhat's Your Sweet Spot?
Are you in a niche that’s growing or shrinking? Is it time to reassess and refocus? We spotlight companies thriving by redefining or reinforcing their niche. What are their insights?
Moving Forward With Confidence
In this issue, we focus on sales and quoting, workforce training, new IPC leadership in the U.S. and Canada, the effects of tariffs, CFX standards, and much more—all designed to provide perspective as you move through the cloud bank of today's shifting economic market.
Intelligent Test and Inspection
Are you ready to explore the cutting-edge advancements shaping the electronics manufacturing industry? The May 2025 issue of SMT007 Magazine is packed with insights, innovations, and expert perspectives that you won’t want to miss.
- Articles
- Columns
- Links
- Media kit
||| MENU - smt007 Magazine
American Standard Circuits’ Unique Offerings Contribute to Long-term Success
June 11, 2015 | Barry Matties, I-Connect007Estimated reading time: 5 minutes
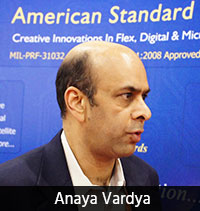
At the recent IMS RF and microwave show in Phoenix, Arizona, I had a chance to catch up with Anaya Vardya, CEO of American Standard Circuits, which has been in business for more than a quarter-century. In this interview, we discuss market trends, recent equipment investments and where their growth as a company will likely come from.
Barry Matties: Anaya, the IMS microwave show, as you said, is a large part of your business. Why don't you give me a little history about American Standard Circuits—where you guys started and how you got where you are.
Anaya Vardya: We've been in business for about 27 years now, as of this August. The shop started with four people, so it was a very small facility. We've now grown to more than 100 employees. We're about $17 million in revenue, so we've grown fairly significantly over the last 20-plus years. A good portion, between 60–65% of our business, is focused on the RF/microwave sector. We have a pretty large portion in automotive telematics. We also do a fair amount of business in communication and a lot in mil/aero.
One thing that is pretty unique about us is the fact that we're able to build a lot of different kinds of metal-backed PCBs for the RF/microwave space. We have a couple of patents in that area. In addition, we've got some very unique offerings in the metal-backed sector, including the fact that we can do some very quick turns on this kind of technology. We're probably one of the only shops that can turn metal-backed technology in five days or less.
Matties: So your patents have given you some competitive advantages.
Vardya: Right, our patents give us competitive advantages because we have the ability to actually bond circuit boards to metal with our proprietary materials. Some of the proprietary materials have advantages over the commercially available materials and are preferred by many of our customers.
Matties: With the RF market, the automotive sector has grown a lot for you then.
Vardya: Yes, it has. In the last few years we've seen significant increase in the amount of electronics content in automobiles, with technologies like blind spot detection, automatic braking, and stop and go in crowded areas. What you're seeing in a lot of these applications is RF/microwave–type circuits, and because of that you're seeing a lot more RF microwave boards in the automotive sector.
Matties: What sorts of process requirements do your customers have?
Vardya: Several things: many different kinds of materials; a lot of very thin boards; very tight registration requirements; and then very fine lines and fine circuits. What's really important in the RF/microwave space is the tight tolerance on requirements.
Matties: You mentioned military as well.
Vardya: We're participating in a large number of different sectors. We've built boards that have ended up in IED collision avoidance devices worn on backs of marines. We've also done boards for satellites and the F-35 fighter jet program. We really have a very large variety of applications.
Matties: There's got to be a great sense of pride in your organization when you're building products for such important missions.
Vardya: Yes, there absolutely is.
Matties: All the manufacturing is done in your facility in West Chicago. Is that where you started?Page 1 of 2
Suggested Items
Meet the Author Podcast: Martyn Gaudion Unpacks the Secrets of High-Speed PCB Design
07/16/2025 | I-Connect007In this special Meet the Author episode of the On the Line with… podcast, Nolan Johnson sits down with Martyn Gaudion, signal integrity expert, managing director of Polar Instruments, and three-time author in I-Connect007’s popular The Printed Circuit Designer’s Guide to... series.
Intervala Hosts Employee Car and Motorcycle Show, Benefit Nonprofits
08/27/2024 | IntervalaIntervala hosted an employee car and motorcycle show, aptly named the Vala-Cruise and it was a roaring success! Employees had the chance to show off their prized wheels, and it was incredible to see the variety and passion on display.
KIC Honored with IPC Recognition for 25 Years of Membership and Contributions to Electronics Manufacturing Industry
06/24/2024 | KICKIC, a renowned pioneer in thermal process and temperature measurement solutions for electronics manufacturing, is proud to announce that it has been recognized by IPC for 25 years of membership and significant contributions to electronics manufacturing.
Boeing Starliner Spacecraft Completes Successful Crewed Docking with International Space Station
06/07/2024 | BoeingNASA astronauts Barry "Butch" Wilmore and Sunita "Suni" Williams successfully docked Boeing's Starliner spacecraft to the International Space Station (ISS), about 26 hours after launching from Cape Canaveral Space Force Station.
KIC’s Miles Moreau to Present Profiling Basics and Best Practices at SMTA Wisconsin Chapter PCBA Profile Workshop
01/25/2024 | KICKIC, a renowned pioneer in thermal process and temperature measurement solutions for electronics manufacturing, announces that Miles Moreau, General Manager, will be a featured speaker at the SMTA Wisconsin Chapter In-Person PCBA Profile Workshop.