-
- News
- Books
Featured Books
- smt007 Magazine
Latest Issues
Current IssueWhat's Your Sweet Spot?
Are you in a niche that’s growing or shrinking? Is it time to reassess and refocus? We spotlight companies thriving by redefining or reinforcing their niche. What are their insights?
Moving Forward With Confidence
In this issue, we focus on sales and quoting, workforce training, new IPC leadership in the U.S. and Canada, the effects of tariffs, CFX standards, and much more—all designed to provide perspective as you move through the cloud bank of today's shifting economic market.
Intelligent Test and Inspection
Are you ready to explore the cutting-edge advancements shaping the electronics manufacturing industry? The May 2025 issue of SMT007 Magazine is packed with insights, innovations, and expert perspectives that you won’t want to miss.
- Articles
- Columns
- Links
- Media kit
||| MENU - smt007 Magazine
Taking the Human Out of Hand Soldering: Is it a Must?
June 15, 2015 | Barry Matties, I-Connect007Estimated reading time: 6 minutes
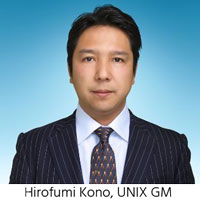
At NEPCON 2015 in Shanghai, I stopped by the WKK booth where Japan Unix (represented by WKK in China) was displaying its new robotic soldering technology. Japan Unix’s robotic soldering module is fully automated—there is no need for a human operator. With automation a key focus on driving labor cost down and the need for reproducible quality, automated hand soldering systems are certainly a smart focus. In this interview, General Manager Hirofumi Kono explains why this new technology makes so much sense.
Barry Matties: Is the idea that this technology could replace hand soldering?
Hirofumi Kono: Yes. We have been working with this kind of machine and technology for more than 35 years. When we started robotic soldering in the 1970s, it was only with a one-cylinder system. In the early ’80s, we started implementing a six-axis robotic base model.
Matties: So it's faster and more accurate than humans?
Kono: The advantage of robotics is the soldering speed. An advanced operator might be faster because of his or her skill, but compared to a beginner operator, robotics is faster. Also, technicians calculate at an average speed. Robots can calculate the throughput much easier and the accuracy is much better than the operator, because robots always go to the same position. With the vision sensor on this model you can check the position to make sure it solders correctly.
Matties: What would make somebody come in and buy this today? If I have experienced technicians doing the hand soldering, and they're faster than robots, what's the biggest advantage then?
Kono: The advantage is that labor costs are increasing in some countries. The technician is costing more and more, but the soldering machine is only a one-time investment. With the operator, you have to hire and train continuously. Side by side, the machine’s speed is not much faster than that of an experienced operator, but the average speeds over time are higher than personal operators. In the long term it is faster and cheaper.
Matties: But is it faster per piece?
Kono: Per piece, especially with less quantity or a single board for R&D, an experienced operator is much faster. Robotic soldering systems can copy an advanced technician’s know-how, but cannot duplicate a technician’s skill. The best soldering performance for single pieces is by an advanced technician.
Matties: I see what you are saying. The average would be faster because this can work 24 hours a day without breaks.
Kono: It depends on the model.
Matties: In some countries, it would take a long time to get a return on investment, right? That must be a difficult sell for you in places like China, for example.
Kono: In China, labor costs are getting higher. Also, it’s very difficult to hire factory workers these days. Most EMS companies want to use the same machine in every country, not only in China, but India, Mexico, Vietnam, Indonesia, etc. They cannot control the skills of technicians in all these countries. If they use this one machine, they can control the quality in each country. This option is much more cost-effective than hand soldering.
Matties: One machine replaces how many operators?
Kono: One machine might cover at least three operators in one day, but it depends on the configuration and the component.
Matties: Is there any advantage to having a human physically looking at this versus the machine? If I had a human doing the hand soldering, will they recognize some of the problems that the machine may not detect? Because with the human, you have experience; with the machine, you do not.
Kono: Experience differs between every technician. No two technicians do everything the same. But with robotics, even a hundred robots can make the same circuit board with the same soldering condition and quality. But if you hire a hundred operators, even if they are experienced technicians, the hundred circuit boards will have differences and won’t be the same.
Matties: Can you use anybody's solder wire with your systems?
Kono:Yes.
Matties: Good, so that's not a variable or a roadblock. The footprint is rather small and you can just line these up. For loading the boards, I would assume it's all optically aligned for the start position?
Kono: Yes, loading and unloading is done by an operator. But this operator can just load the board and press the start switch, which is less cost because even a newcomer or beginner can perform this action. If the customer wants to have something like a more integrated system, we also have both a robotic conveyor system and laser soldering system.
Matties: Does the laser offer more precision?
Kono: It offers more precision and much less maintenance time. With the soldering iron, you have to clean the iron tip about every six hours, so you need to keep checking the iron to maintain good soldering quality. Also, when you solder a lot of points, the iron tips have to be replaced periodically.
Matties: I see the laser system is a conveyorized system as well, which is nice. The laser basically lasts forever, right?
Kono: You just need to change the solder wire and clean up optics.
Matties: I think the return on investment must be faster because you no longer need the operator to load the board.
Page 1 of 2
Suggested Items
Driving Innovation: Direct Imaging vs. Conventional Exposure
07/01/2025 | Simon Khesin -- Column: Driving InnovationMy first camera used Kodak film. I even experimented with developing photos in the bathroom, though I usually dropped the film off at a Kodak center and received the prints two weeks later, only to discover that some images were out of focus or poorly framed. Today, every smartphone contains a high-quality camera capable of producing stunning images instantly.
Hands-On Demos Now Available for Apollo Seiko’s EF and AF Selective Soldering Lines
06/30/2025 | Apollo SeikoApollo Seiko, a leading innovator in soldering technology, is excited to spotlight its expanded lineup of EF and AF Series Selective Soldering Systems, now available for live demonstrations in its newly dedicated demo room.
Indium Corporation Expert to Present on Automotive and Industrial Solder Bonding Solutions at Global Electronics Association Workshop
06/26/2025 | IndiumIndium Corporation Principal Engineer, Advanced Materials, Andy Mackie, Ph.D., MSc, will deliver a technical presentation on innovative solder bonding solutions for automotive and industrial applications at the Global Electronics A
Fresh PCB Concepts: Assembly Challenges with Micro Components and Standard Solder Mask Practices
06/26/2025 | Team NCAB -- Column: Fresh PCB ConceptsMicro components have redefined what is possible in PCB design. With package sizes like 01005 and 0201 becoming more common in high-density layouts, designers are now expected to pack more performance into smaller spaces than ever before. While these advancements support miniaturization and functionality, they introduce new assembly challenges, particularly with traditional solder mask and legend application processes.
Knocking Down the Bone Pile: Tin Whisker Mitigation in Aerospace Applications, Part 3
06/25/2025 | Nash Bell -- Column: Knocking Down the Bone PileTin whiskers are slender, hair-like metallic growths that can develop on the surface of tin-plated electronic components. Typically measuring a few micrometers in diameter and growing several millimeters in length, they form through an electrochemical process influenced by environmental factors such as temperature variations, mechanical or compressive stress, and the aging of solder alloys.