-
-
News
News Highlights
- Books
Featured Books
- smt007 Magazine
Latest Issues
Current IssueWhat's Your Sweet Spot?
Are you in a niche that’s growing or shrinking? Is it time to reassess and refocus? We spotlight companies thriving by redefining or reinforcing their niche. What are their insights?
Moving Forward With Confidence
In this issue, we focus on sales and quoting, workforce training, new IPC leadership in the U.S. and Canada, the effects of tariffs, CFX standards, and much more—all designed to provide perspective as you move through the cloud bank of today's shifting economic market.
Intelligent Test and Inspection
Are you ready to explore the cutting-edge advancements shaping the electronics manufacturing industry? The May 2025 issue of SMT007 Magazine is packed with insights, innovations, and expert perspectives that you won’t want to miss.
- Articles
- Columns
- Links
- Media kit
||| MENU - smt007 Magazine
A Review of the Opportunities and Processes for Printed Electronics (Part 2): Printing Technologies
June 24, 2015 | Happy Holden, PCB Technologist-RetiredEstimated reading time: 11 minutes
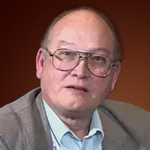
In printed electronics, the selection of printing method to use is determined by requirements concerning printed layers and properties of printed materials, as well as economic and technical considerations for printed products.
Presently, printing technologies divide between sheet-based and roll-to-roll-based approaches. Sheet-based techniques, such as inkjet and screen printing, are best for low-volume, high-precision work. Gravure, offset and flexographic printing are more common for high-volume production, such as solar cells, reaching 10,000m²/h.
While offset and flexographic printing are mainly used for inorganic and organic conductors (the latter also for dielectrics), gravure printing is especially suitable for quality-sensitive layers like organic semiconductors and semiconductor/dielectric-interfaces in transistors, due to high layer image registration quality. Gravure printing is also suitable for inorganic and organic conductors in terms of high resolution. Organic field-effect transistors and integrated circuits can be prepared completely using mass-printing methods.
Screen printing
Screen printing is a printing technique that uses a woven mesh to support an ink-blocking stencil. The attached stencil forms open areas of mesh that transfer ink or other printable materials that can be pressed through the mesh as a sharp-edged image onto a substrate. A roller or squeegee is moved across the screen stencil, forcing or pumping ink past the threads of the woven mesh in the open areas.
Screen printing is also a stencil method of printmaking in which a design is imposed on a screen of silk or other fine mesh with blank areas coated with an impermeable substance, and ink is forced through the mesh onto the printing surface. It is also known as silkscreen, seriography and serigraph.
Rotogravure printing
Rotogravure (roto or gravure for short) is a type of intaglio printing process, which means that it involves engraving the image onto an image carrier. In gravure printing, the image is engraved onto a cylinder because, like offset and flexography, it uses a rotary printing press. The vast majority of gravure presses print on rolls (also known as webs) of paper, rather than sheets of paper. (Sheet-fed gravure is a small, specialty market.)
Rotary gravure presses are the fastest and widest presses in operation, printing everything from narrow labels to rolls of vinyl flooring 12ft (4m) wide. Additional operations may be conducted in line with a gravure press, such as saddle stitching facilities for magazine and brochure work. Once a staple of newspaper photo features, the rotogravure process is still used for commercial printing of magazines, postcards and corrugated (cardboard) product packaging.
Flexograph printing
Flexography (often abbreviated as flexo) utilizes a flexible relief plate. It is an updated version of the letterpress and can be used for printing on almost any type of substrate, including plastic, metallic films, cellophane and paper. It is widely used for printing on the non-porous substrates required for various types of food packaging. It is also well-suited for printing large areas of solid color.
The greatest advances in flexographic printing have been in the area of photopolymer printing plates, including improvements to the plate material and the method of plate creation.
Digital direct-to-plate systems have been a good improvement in the industry recently. Companies like AV Flexologic, DuPont, MacDermid, Kodak and Esko have pioneered recent technologies with advances in fast washout and the latest screening technology.
Laser-etched ceramic anilox rolls also play a part in the improvement of print quality. Full color picture printing is now possible, and some of the finer presses available today, in combination with a skilled operator, allow quality that rivals the lithographic process. One ongoing improvement has been the increasing ability to reproduce highlight tonal values, thereby providing a workaround for the very high dot gain associated with flexographic printing.
There are five types of inks that can be used in flexography: solvent-based inks, water-based inks, electron beam (EB) curing inks, ultraviolet (UV) curing inks and two-part chemically-curing inks (usually based on polyurethane isocyanate reactions), although these are uncommon at the moment. Water-based flexo inks with particle sizes below 5μm may cause problems when de-inking recycled paper.
Ink control
In the flexographic printing process, ink is controlled by the inking unit. The inking unit can be either a fountain roll system or doctor blade system. The fountain roll system is a simple, old system. Yet if there is too much or too little ink, this system would not likely control ink in a good way. The doctor blade inside the anilox roller uses cell geometry and distribution. These blades ensure that the cells are filled with enough ink.
Offset printing
Offset printing is the most widely used printing technique for newspapers and magazines worldwide. Famous equipment, such as the Heidelberg and MAN-Roland presses, makes nearly two-thirds of the world’s newspapers and high-quality magazines. These include web and sheet-fed offset presses, as well as digital printing systems.
Offset has high resolution, but only a very thin ink film can be transferred, typically 1μm to 2μm on the substrate, but at a resolution of 50μm or less. This thickness is suitable for printing catalytic inks, allowing the conductor thickness to be subsequently increased by additive or semi-additive post-deposition processes.
From the simplest stenciling to the most sophisticated offset, traditional printing technologies are still the mainstay of printing today. For flexographic printing, the previous step was contact with an ink-coated roller where the ink thickness had been adjusted using a doctor blade. In the gravure printing example, the previous step would have been contact with a doctor blade to remove excess ink from the coated surface, which controls the depth of the cavities in the print roller. Photolithographic printing is another traditional technology. However, it has limited applicability, with the exception of the prospect of crossover of catalyst-coated materials that can be activated by light. This method has thus far been limited to molded interconnection devices.Page 1 of 2
Suggested Items
I-Connect007 Editor’s Choice: Five Must-Reads for the Week
07/18/2025 | Nolan Johnson, I-Connect007It may be the middle of the summer, but the news doesn’t quit, and there’s plenty to talk about this week, whether you’re talking technical or on a global scale. When I have to choose six items instead of my regular five, you know it’s good. I start by highlighting my interview with Martyn Gaudion on his latest book, share some concerning tariff news, follow that up with some promising (and not-so-promising) investments, and feature a paper from last January’s inaugural Pan-European Design Conference.
Elephantech Launches World’s Smallest-Class Copper Nanofiller
07/17/2025 | ElephantechJapanese deep-tech startup Elephantech has launched its cutting-edge 15 nm class copper nanofiller – the smallest class available globally. This breakthrough makes Elephantech one of the first companies in the world to provide such advanced material for commercial use.
Copper Price Surge Raises Alarms for Electronics
07/15/2025 | Global Electronics Association Advocacy and Government Relations TeamThe copper market is experiencing major turbulence in the wake of U.S. President Donald Trump’s announcement of a 50% tariff on imported copper effective Aug. 1. Recent news reports, including from the New York Times, sent U.S. copper futures soaring to record highs, climbing nearly 13% in a single day as manufacturers braced for supply shocks and surging costs.
I-Connect007 Editor’s Choice: Five Must-Reads for the Week
07/11/2025 | Andy Shaughnessy, Design007 MagazineThis week, we have quite a variety of news items and articles for you. News continues to stream out of Washington, D.C., with tariffs rearing their controversial head again. Because these tariffs are targeted at overseas copper manufacturers, this news has a direct effect on our industry.I-Connect007 Editor’s Choice: Five Must-Reads for the Week
Digital Twin Concept in Copper Electroplating Process Performance
07/11/2025 | Aga Franczak, Robrecht Belis, Elsyca N.V.PCB manufacturing involves transforming a design into a physical board while meeting specific requirements. Understanding these design specifications is crucial, as they directly impact the PCB's fabrication process, performance, and yield rate. One key design specification is copper thieving—the addition of “dummy” pads across the surface that are plated along with the features designed on the outer layers. The purpose of the process is to provide a uniform distribution of copper across the outer layers to make the plating current density and plating in the holes more uniform.