-
- News
- Books
Featured Books
- smt007 Magazine
Latest Issues
Current IssueWhat's Your Sweet Spot?
Are you in a niche that’s growing or shrinking? Is it time to reassess and refocus? We spotlight companies thriving by redefining or reinforcing their niche. What are their insights?
Moving Forward With Confidence
In this issue, we focus on sales and quoting, workforce training, new IPC leadership in the U.S. and Canada, the effects of tariffs, CFX standards, and much more—all designed to provide perspective as you move through the cloud bank of today's shifting economic market.
Intelligent Test and Inspection
Are you ready to explore the cutting-edge advancements shaping the electronics manufacturing industry? The May 2025 issue of SMT007 Magazine is packed with insights, innovations, and expert perspectives that you won’t want to miss.
- Articles
- Columns
- Links
- Media kit
||| MENU - smt007 Magazine
Characterization of Solder Defects in Package-on-Package with AXI Systems for Inspection Quality Improvement (Part 1)
June 29, 2015 | Z. Feng, D. Geiger, W. Liu, A. Mohammed, M. Kurwa, Flextronics, and G. Tint, HDI SolutionsEstimated reading time: 5 minutes
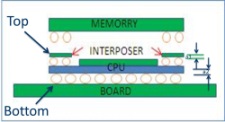
Abstract
As a part of series of studies on X-ray inspection technology to quantify solder defects in BGA balls, we have conducted inspection of three-level Package-on-Package (PoP) by using a new automated X-ray inspection (AXI) technology that is capable of 3D-CT imaging. The new results are compared with the results of earlier AXI measurements. It is found that 3D measurements offer better defect inspection quality, and reduce lower false call and escapes.
Introduction
Package-on-Package (POP) devices are different from conventional SMT devices because they require solder attachments at different levels from the PCB surface. Their importance becomes even greater as PoPs are increasingly utilized in various types of assemblies because designers want to take advantage of 3D integration, to offer superior performances in their new products. Therefore, achieving the best possible PoP solder joint quality becomes important consideration for today’s PCBA manufacturers.
As solder joints in a PoP device cannot be inspected by optical means, X-ray inspection mostly is the only way to assure their quality nondestructively. Recently, automated X-ray inspection—AXI (AXI3, AXI4)—are found to have capabilities to detect not only solder bridge, missing ball, extra solder, and ball voiding defects, but also open/HIP for the bottom and top layers of POP. However, AXI images are not as clear as 2DX and planar CT (pCT). In this project, we used an AXI with pCT (AXI5) capability to characterize the solder defects in POP to explore improvement in inspection quality in a production environment.
The goal of this project is to evaluate the level of performance offered by different types of X-ray inspection equipment. It is better for the PCBA manufacturers to be able to test POP using AXI with pCT images. Getting unambiguous images with Pass/Fail result AUTO output are the obvious benefits. Our project consists of three phases: (1) Analytical comparison of images acquired by 2DX and AXI with pCT; (2) exploration of possibilities to optimize the AXI with pCT algorithms in order to improve the quality of defect detection; and (3) attempt to develop a process for AXI with pCT algorithm optimization.
Background
With more and more PoP packages in production assemblies, achieving zero defects escape rate came to our focus in recent years. In early 2013, we faced the issue that some open defective pins on the top layer of POP were escaped from AXI. Therefore, we have been working with our engineers and X-ray vendors for this issue being resolved. In 2013, the best detecting coverage for open/HIP on the bottom layer was 85% with about 14,000+ false call PPM, and was about 50% defects detecting coverage with >30,000 false call PPM for the top layer of POP. It was not available to detect open / HIP on top layer with 3 layers POP from our AXIs that time.
However with many efforts for new software development, as well as Algorithms Threshold settings studies, good achievements were obtained in 2014. Both AXI 3 and AXI 4 have capabilities to detect open/HIP defects with three-layer PoP packages, and the average defects escaped is 4-8% with about 20,000+ false call PPM. The challenge was that getting clear image difference between good solder and bad solder pins while showing big separation between good and bad joints numerical data as measured by main Algorithm.
There was benefit to verify POP solder joints with AXI capabilities. Since November of 2013, we have not seen any defective pin on 3 layers POP from our SMT lines at Milpitas site after SMT process improvement. With the real-time AXI testing data feedback, we are confident with our SMT process. Because of our AXI machine on the line with high false call PPM and not clear different X-ray images between good solder joint and bad solder joint, therefore usually we use 2DX to verify the defective pins which called at AXI. In this way, we do rework only when it is real defect.
Experiments
In this project, we use AXI 5 for POP X-ray inspection. The reason we choose AXI 5 is that it not only has AXI capabilities, but also offers CT capabilities at reasonably high speed. These features (AXI & pCT) should provide more benefits for our SMT lines.
1. Summary of Previous Experiments on AXI3, AXI4
The inspection quality of AXI not only depends on the AXI machine design, but also on the on the structural complexity of a given POP. Figure 1 illustrates the three-layer POP we utilized in this study, which is assembled on a customer board. We do not test middle interposer ball layer of the POP on AXI as no SMT process is required on these pins. The POP structural information is tabulated in Table 1.
Figure 1: Structure of 3 BGA layers POP on Customer Board
- a1 (Substrate1) = 0.122 ±0.022 mm
- a2 (Substrate 2) = 0.262 ±0.022 mm
The 2DX results are adopted as the reference for this POP AXI study. We use two parameters (Defect Escaped % and False Call PPM) to evaluate the AXI capability. Table 2 summarized the results from inspections by AXI 3, and AXI 4. The definitions of Defect Escaped % and False Call PPM are expressed by Equation 1, and Equation 2.
Equation 1:
Defect Escaped % = (Total # of Defect Escaped / Total # of Defects) x 100%
Equation 2:
False Call PPM = (Total # of False Call / Total # of Tested Pins) x 1,000,000
The 2DX, AXI3, and AXI 4 testing results are shown with pin locations in Figure 2. The cell colors are described as below.
Figure 2: The Test Results of POP Board from 2DX, AXI3, AXI4
Figure 3: X-ray images for Detected HIP, Good solder, False Call pins from 2DX, AXI3, and AXI4.
Figure 3 shows X-ray images for Defective HIP, Good solder, and False Call pins on top BGA ball layer of the POP from 2DX, AXI3, and AXI4, where green, red, and yellow colors stand for Good solder joint, HIP/Open defective pin, and False Call pin respectively. It is obvious to see difference for good solder and open solder on 2DX images. Based on the observed images, the big challenge in AXI is that there is no obvious difference visible between the images of good solder joint verses defective HIP/Open pins. It is also observed at both AXI3, and AXI4 machines.
Therefore, our previous AXI study showed that AXI 3 and AXI 4 have capabilities to test POP including three ball layers by full AUTO mode with focus images for different BGA layers on POP Package. Both AXI3 and AXI4 have capabilities to detect POP open, HIP defects with some level of success. There is no clear visual distinction between AXI images of good verses bad pins, especially when it comes to HIP/Open defects. The requirement to balance for Defect Escaped % and False Call PPM was our main focus issue for AXI with POP study, and looking forward to having characterization of solder defects in POP with AXI systems for inspection quality improvement. That is the driving factor to work on with AXI 5 which has AXI and pCT capabilities for the POP project.
In Part 2, the authors discuss the highlights of AXI with planar computer tomography (pCT).
Editor's Note: This paper has been published in the technical proceedings of IPC APEX EXPO.
Suggested Items
Driving Innovation: Direct Imaging vs. Conventional Exposure
07/01/2025 | Simon Khesin -- Column: Driving InnovationMy first camera used Kodak film. I even experimented with developing photos in the bathroom, though I usually dropped the film off at a Kodak center and received the prints two weeks later, only to discover that some images were out of focus or poorly framed. Today, every smartphone contains a high-quality camera capable of producing stunning images instantly.
Hands-On Demos Now Available for Apollo Seiko’s EF and AF Selective Soldering Lines
06/30/2025 | Apollo SeikoApollo Seiko, a leading innovator in soldering technology, is excited to spotlight its expanded lineup of EF and AF Series Selective Soldering Systems, now available for live demonstrations in its newly dedicated demo room.
Indium Corporation Expert to Present on Automotive and Industrial Solder Bonding Solutions at Global Electronics Association Workshop
06/26/2025 | IndiumIndium Corporation Principal Engineer, Advanced Materials, Andy Mackie, Ph.D., MSc, will deliver a technical presentation on innovative solder bonding solutions for automotive and industrial applications at the Global Electronics A
Fresh PCB Concepts: Assembly Challenges with Micro Components and Standard Solder Mask Practices
06/26/2025 | Team NCAB -- Column: Fresh PCB ConceptsMicro components have redefined what is possible in PCB design. With package sizes like 01005 and 0201 becoming more common in high-density layouts, designers are now expected to pack more performance into smaller spaces than ever before. While these advancements support miniaturization and functionality, they introduce new assembly challenges, particularly with traditional solder mask and legend application processes.
Knocking Down the Bone Pile: Tin Whisker Mitigation in Aerospace Applications, Part 3
06/25/2025 | Nash Bell -- Column: Knocking Down the Bone PileTin whiskers are slender, hair-like metallic growths that can develop on the surface of tin-plated electronic components. Typically measuring a few micrometers in diameter and growing several millimeters in length, they form through an electrochemical process influenced by environmental factors such as temperature variations, mechanical or compressive stress, and the aging of solder alloys.