-
-
News
News Highlights
- Books
Featured Books
- smt007 Magazine
Latest Issues
Current IssueWhat's Your Sweet Spot?
Are you in a niche that’s growing or shrinking? Is it time to reassess and refocus? We spotlight companies thriving by redefining or reinforcing their niche. What are their insights?
Moving Forward With Confidence
In this issue, we focus on sales and quoting, workforce training, new IPC leadership in the U.S. and Canada, the effects of tariffs, CFX standards, and much more—all designed to provide perspective as you move through the cloud bank of today's shifting economic market.
Intelligent Test and Inspection
Are you ready to explore the cutting-edge advancements shaping the electronics manufacturing industry? The May 2025 issue of SMT007 Magazine is packed with insights, innovations, and expert perspectives that you won’t want to miss.
- Articles
- Columns
- Links
- Media kit
||| MENU - smt007 Magazine
A Greener, Money-saving Approach to Dealing with Waste
August 5, 2015 | Steve Burns, Conecsus LLCEstimated reading time: 6 minutes
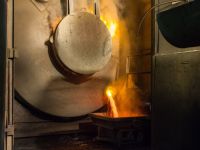
One of the world's leading contract manufacturers and EMS companies, Sanmina, has a high-technology manufacturing facility in Huntsville, Alabama. This facility produces advanced electronic products for some of the world’s leading medical and defense companies.
Sanmina produces state of the art PCBAs (printed circuit board assemblies) on several advanced SMT (surface mount technology) lines. Many of these SMT lines produce products in high volumes. These SMT lines understandably use water, disposables and other materials that result in a significant amount of hazardous waste.
While Sanmina is recognized in Huntsville and around the world as a "green" company, and one that uses state of the art processing for waste treatment, they are classified as a "Large Waste Generator" in the area. For SMT, the primary by-products are solder dross and solder-contaminated consumables. Responsibly managing and disposing of these materials was costing the facility between $12,000 to $20,000 per year, depending on manufacturing volumes. One of the agencies Sanmina works with to certify processes and procedures for hazardous waste disposal is the Alabama Department of Environmental Management, or ADEM, one of the strictest state regulatory agencies in the country.
"We tried a total of three times over the years to get ADEM to approve different processes for dealing with this waste that we advanced," says Patsy Smolik, CMfgT, Regional Environmental Health and Safety Engineer at the Sanmina Corporation facility. "Twice they turned us down, because the process that we suggested, while efficiently dealing with the waste, was not 'true' recycling of the material. They were very strict about that." Sanmina always met or exceeded environmental standards for waste treatment, but was always looking for a better, greener way that would cost less. And wasn't there a way, somewhere, to recycle this material?
The stakes were huge; Sanmina provides advanced technology products to some of the world’s most innovative companies. These products have electronics using lead and lead-free solders depending on the application. There is considerable diversity in the waste streams, and as regulations continue to tighten, the costs associated with dealing with hazardous waste continue to rise.
In 2014, the facility shipped 12,000 pounds of waste material for processing and disposal. That's a lot of dross and solder-contaminated consumables. There had to be a more efficient and environmentally friendly way of processing these materials.
The solution came from a refining company in Terrell, Texas that has been, until recently, virtually unknown in the SMT PCB assembly industry. In 2013, Conecsus LLC developed the RACS (Reducing Agent: Coke Substitute) technology process, which is focused solely on the waste stream colloquially known as "contaminated trash". This material is generally comprised of under-stencil wipes, spent paste, tubes and jars, gloves, rags, finger cots, and other similar items that are, from a regulatory standpoint, a characteristically hazardous and regulated waste.
Figure 1: Conecsus Rotary furnace that utilizes RACS material in processing metal residues.
Toxic metal residues are what cause this material to be considered hazardous by regulatory agencies, and these cannot be processed or transported in the same fashion as solder dross when a generator has a "Small or Large Quantity Generator" status. As such, they are very expensive to manage or dispose of, and a great deal of record keeping is required to remain compliant with state and federal regulations.
The RACS technology allows Conecsus to take that material and re-use it as a reagent ingredient in the processing of other materials, such as solder dross, filter cakes, detinning dross, and other tin or lead residues. This small but important distinction in many cases gives generators in most states the ability to ship it to Conecsus with the dross on a common carrier, with a bill of lading along with their solder dross. This may eliminate the need for an expensive hazardous waste carrier, or processing the material through a hazardous waste management firm.
"Dealing with metal residues and metal contaminated residues from Surface Mount Operations, can be expensive and complex," explains Steve Burns, Regional Sales Manager for Conecsus LLC. "When we initially approached Sanmina with our RACS solution, they were very skeptical, and understandably so. They had already tried twice to get ADEM to approve more progressive solutions for dealing with contaminated surface mount residues and trash. With our system, contaminated waste becomes a useful product, a reagent in an industrial process that produces a product with value.
"We had to get approval from the regulatory staff at ADEM before Sanmina would approve of the new process RACS provides," Steve continues. "If managed as hazardous waste by environmental companies, these materials normally go to fuel blending or landfill. Hazardous waste minimization and sustainability are goals of many responsible companies like Sanmina. Additional cost savings are realized in the fact that, when these materials are shipped to Conecsus, they can be shipped common carrier. When classified as hazardous waste, higher-priced regulated carriers are required."
The patented Conecsus RACS technology allows generators to send their solder-contaminated waste to Conecsus as a reagent replacement rather than as a hazardous waste, and as a result, it also reduces the amount of hazardous waste that the client generates because they no longer have to report these materials as hazardous waste. The RACS process allows the refiner to re-use the carbon units, containing metallics, as a reagent in Conecsus' other pyrometallurgical processes, and this reduces the amount of coal products needed for their reagent values in refining impure metals.
Page 1 of 2
Suggested Items
Silicon Mountain Contract Services Enhances SMT Capabilities with New HELLER Reflow Oven
07/17/2025 | Silicon Mountain Contract ServicesSilicon Mountain Contract Services, a leading provider of custom electronics manufacturing solutions, is proud to announce a significant upgrade to its SMT production capability with the addition of a HELLER 2043 MK5 10‑zone reflow oven to its Nampa facility.
Knocking Down the Bone Pile: Addressing End-of-life Component Solderability Issues, Part 4
07/16/2025 | Nash Bell -- Column: Knocking Down the Bone PileIn 1983, the Department of Defense identified that over 40% of military electronic system failures in the field were electrical, with approximately 50% attributed to poor solder connections. Investigations revealed that plated finishes, typically nickel or tin, were porous and non-intermetallic.
SHENMAO Strengthens Semiconductor Capabilities with Acquisition of PMTC
07/10/2025 | SHENMAOSHENMAO America, Inc. has announced the acquisition of Profound Material Technology Co., Ltd. (PMTC), a premier Taiwan-based manufacturer of high-performance solder balls for semiconductor packaging.
KYZEN to Highlight Understencil and PCB Cleaners at SMTA Querétaro Expo and Tech Forum
07/09/2025 | KYZEN'KYZEN, the global leader in innovative environmentally responsible cleaning chemistries, will exhibit at the SMTA Querétaro Expo & Tech Forum, scheduled to take place Thursday, July 24, at Centro de Congresos y Teatro Metropolitano de Querétaro.
Driving Innovation: Direct Imaging vs. Conventional Exposure
07/01/2025 | Simon Khesin -- Column: Driving InnovationMy first camera used Kodak film. I even experimented with developing photos in the bathroom, though I usually dropped the film off at a Kodak center and received the prints two weeks later, only to discover that some images were out of focus or poorly framed. Today, every smartphone contains a high-quality camera capable of producing stunning images instantly.