-
-
News
News Highlights
- Books
Featured Books
- design007 Magazine
Latest Issues
Current IssueAll About That Route
Most designers favor manual routing, but today's interactive autorouters may be changing designers' minds by allowing users more direct control. In this issue, our expert contributors discuss a variety of manual and autorouting strategies.
Creating the Ideal Data Package
Why is it so difficult to create the ideal data package? Many of these simple errors can be alleviated by paying attention to detail—and knowing what issues to look out for. So, this month, our experts weigh in on the best practices for creating the ideal design data package for your design.
Designing Through the Noise
Our experts discuss the constantly evolving world of RF design, including the many tradeoffs, material considerations, and design tips and techniques that designers and design engineers need to know to succeed in this high-frequency realm.
- Articles
- Columns
- Links
- Media kit
||| MENU - design007 Magazine
Fighting the War on Failure
August 11, 2015 | Andy Shaughnessy, PCBDesign007Estimated reading time: 3 minutes
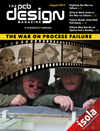
In the August 2015 issue of The PCB Design Magazine, the focus is on the “War on Failure,” a war that your company is likely already prosecuting. The big question is this: Can we ever win this war?
No one in this industry sets out to fail, except failure analysis test engineers. But failure is a part of life for designers and manufacturers of electronics. Our reader surveys show that failure affects nearly everyone in the PCB industry: designers, fabricators, assembly providers, OEMs, and suppliers.
And failure itself is difficult to define; everyone has a different definition.
The meaning of “failure” seems to evolve over time. Think about this: The PCB design process of the past would be considered a failure today. Decades ago, many PCB designs went through multiple design iterations and board re-spins. No one labeled those actions as failures; it’s just the way the process worked back then.
There was no hand-wringing about it, no post-mortem meetings full of downcast faces, wondering what went wrong. That was the accepted practice. I bet design managers included these multiple steps in their department’s flow charts.
Multiple iterations and board re-spins weren’t an issue until price and time-to-market made them an issue. Once high-speed PCBs became the norm, doing redesigns and building prototype after prototype was no longer financially feasible. Design teams began using simulation and analysis, the “right the first time” movement took off, and now we look at the old way as a failure.
The same holds true for PCB fabrication and assembly providers. The scrap rates of the past would run a company out of business today. Now, manufacturers are adopting processes like Lean and Six Sigma to help eliminate as much waste as humanly possible. Six Sigma’s 99.997% rate of perfection is no longer considered an unattainable dream.
What Does Failure Mean to You?
That was one of the first questions I posed in our cover story interview, “Kelly Dack and Mark Thompson Unite in the War on Failure.” Kelly and Mark come from design and CAM backgrounds, respectively, and they’ve teamed up in this ongoing battle. In this interview, they discuss their definition of failure, some of the more common failures they see from their perspectives, and a variety of ways to keep failures to a minimum. But as they point out, we’ll probably never eliminate failure completely from the PCB industry.
Paul Reid’s feature column, “Failure Mode: Hole Wall Pullaway,” details how stress-relieving and stress-inducing HWPA can cause copper plating in a plated through-hole to be pulled away from the dielectric of the hole wall. As usual, Paul brought along a few of his super cool cross-section animations that show these defects as they happen.
In Tim Haag’s feature column, “Failure May Not be an Option, But Sometimes it’s a Reality,” he discusses some of the mistakes, miscues, and missteps that are common among PCB designers. Working off the famous line by Ed Harris’ character in Apollo 13, “Failure is not an option,” Tim explores everything from not using all of your EDA tool’s inherent capabilities to using far too much automation.
In “Mentor Graphics Helps Bridge Gap between PCB and RF,” Barry Matties interviews Per Viklund, director of IC packaging and RF product lines for Mentor, and Business Development Manager Alex Caravajal. Per and Alex explain how Mentor is helping bring together the RF and PCB design worlds, and their plans to accelerate the RF design cycle.
We also bring you the latest in columnist Barry Olney’s continuing series, “Stackup Planning, Part 3.” This month, Barry looks into stackup configurations for high layer-count, high-speed PCBs, with some stackup tricks for eight-layer designs.
Columnist John Coonrod offers a “Brief Overview of High-Frequency Laminates,” explaining their moisture absorption challenges, thermal properties, and thickness control. He also addresses the use of special fillers to achieve good CTE values and greater stability.
DfR Solutions’ Tom O’Connor offers an update on the ongoing shortage of engineers graduating in North America in “Training the Next-Generation Engineer: When Does it Begin and End?” Tom focuses on the efforts to attract more smart young students to the STEM disciplines, and the need to jump-start these efforts right now, before it’s too late.
This month, our sister magazines The PCB Magazine and SMT Magazine also focus on the war on failure from their perspectives, so don’t forget to check them out.
I’ll see you next month, when we devote the September issue to automotive electronic design. Enjoy the last of your summer—show time is around the corner!
Suggested Items
The Evolution of Picosecond Laser Drilling
06/19/2025 | Marcy LaRont, PCB007 MagazineIs it hard to imagine a single laser pulse reduced not only from nanoseconds to picoseconds in its pulse duration, but even to femtoseconds? Well, buckle up because it seems we are there. In this interview, Dr. Stefan Rung, technical director of laser machines at Schmoll Maschinen GmbH, traces the technology trajectory of the laser drill from the CO2 laser to cutting-edge picosecond and hybrid laser drilling systems, highlighting the benefits and limitations of each method, and demonstrating how laser innovations are shaping the future of PCB fabrication.
Day 2: More Cutting-edge Insights at the EIPC Summer Conference
06/18/2025 | Pete Starkey, I-Connect007The European Institute for the PCB Community (EIPC) summer conference took place this year in Edinburgh, Scotland, June 3-4. This is the third of three articles on the conference. The other two cover Day 1’s sessions and the opening keynote speech. Below is a recap of the second day’s sessions.
Day 1: Cutting Edge Insights at the EIPC Summer Conference
06/17/2025 | Pete Starkey, I-Connect007The European Institute for the PCB Community (EIPC) Summer Conference took place this year in Edinburgh, Scotland, June 3-4. This is the second of three articles on the conference. The other two cover the keynote speeches and Day 2 of the technical conference. Below is a recap of the first day’s sessions.
Preventing Surface Prep Defects and Ensuring Reliability
06/10/2025 | Marcy LaRont, PCB007 MagazineIn printed circuit board (PCB) fabrication, surface preparation is a critical process that ensures strong adhesion, reliable plating, and long-term product performance. Without proper surface treatment, manufacturers may encounter defects such as delamination, poor solder mask adhesion, and plating failures. This article examines key surface preparation techniques, common defects resulting from improper processes, and real-world case studies that illustrate best practices.
RF PCB Design Tips and Tricks
05/08/2025 | Cherie Litson, EPTAC MIT CID/CID+There are many great books, videos, and information online about designing PCBs for RF circuits. A few of my favorite RF sources are Hans Rosenberg, Stephen Chavez, and Rick Hartley, but there are many more. These PCB design engineers have a very good perspective on what it takes to take an RF design from schematic concept to PCB layout.