-
-
News
News Highlights
- Books
Featured Books
- design007 Magazine
Latest Issues
Current IssueAll About That Route
Most designers favor manual routing, but today's interactive autorouters may be changing designers' minds by allowing users more direct control. In this issue, our expert contributors discuss a variety of manual and autorouting strategies.
Creating the Ideal Data Package
Why is it so difficult to create the ideal data package? Many of these simple errors can be alleviated by paying attention to detail—and knowing what issues to look out for. So, this month, our experts weigh in on the best practices for creating the ideal design data package for your design.
Designing Through the Noise
Our experts discuss the constantly evolving world of RF design, including the many tradeoffs, material considerations, and design tips and techniques that designers and design engineers need to know to succeed in this high-frequency realm.
- Articles
- Columns
- Links
- Media kit
||| MENU - design007 Magazine
Kelly Dack and Mark Thompson Unite in the War on Failure
September 9, 2015 | Andy Shaughnessy, PCBDesign007Estimated reading time: 2 minutes
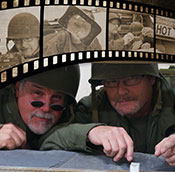
There’s been a lot of talk about fighting the war on failure in the PCB industry. But what strategies should our generals follow to prosecute this war? What exactly constitutes a failure in the first place? Is this war even winnable? I recently spoke with longtime designer Kelly Dack and CAM support veteran Mark Thompson of Prototron Circuits about the best battle plans for beating failure, and why designers and manufacturers must team up against this common enemy.
Andy Shaughnessy: Kelly, you recently said, "Failure wins when it leverages the guerrilla warfare tactic of divide and conquer to confuse and disorient the product development community. Designers and manufacturers must unite to fight this war.”
Why don't you start off by saying what failure means to each of you at the design stage and at the board shop stage?
Kelly Dack: Andy, failure is defined as not meeting the intended objective. But I think the concept is easily confused if coming from isolated design and manufacturing perspectives. Meeting the intended objective successfully can only come from allied efforts. Designers need to describe or define objectives for their projects in terms of concise orders in order to make successful products, but this will only come about if the folks giving orders are also able to follow orders.
Mark Thompson: Absolutely, I agree with Kelly entirely. I'd say from the fabrication side, following orders is easy if the orders are given from time-proven, industry standard specification. We open the door for failure when we have to question orders. But we manufacturers have to occasionally, when the orders are outside of the guidelines of conventional process or machine capability. Designer and manufacturer communication and respect is key here, and I think this is why Kelly mentions that it is important that those giving orders must be willing to take them if the order would put the part at risk of failure.
Shaughnessy: Is failure always someone's fault or is it the fault of a bad process, or is it a combination of both?
Dack: I’m not comfortable pointing fingers at individuals. The causes for success and failure can be attributed to people, but it can also be caused by unforeseen conditions or even acts of God. A good strategy is to identify performance requirements and operating conditions. The “battle plan” needs to identify constraints: design constraints, manufacturing constraints, performance constraints, even cost constraints. Knowing the enemy and anticipating every possible way a design could possibly fail is crucial, but it can’t happen in a vacuum. It must occur through open communication with the allies – stakeholders of the product who are connected through the process steps.
Thompson: If you're asking if every failure is someone's fault, I would say yes, at the most base level. It will always turn out to be someone's fault either due to negligence or lack of vigilance. But, as Kelly said, there are extenuating circumstances. There can be dynamic situations where environmental, human or mechanical conditions create a failure in the field. Or it could be a poor design type of situation, where something wasn't properly considered in the original design phase. It’s a good time to draw in the metaphor of a combat unit here. No one person in a combat unit takes credit for the unit’s success or failure. They are a team!
To read this entire article, which appeared in the August 2015 issue of The PCB Design Magazine, click here.
Suggested Items
DownStream Acquisition Fits Siemens’ ‘Left-Shift’ Model
06/26/2025 | Andy Shaughnessy, I-Connect007I recently spoke to DownStream Technologies founder Joe Clark about the company’s acquisition by Siemens. We were later joined by A.J. Incorvaia, Siemens’ senior VP of electronic board systems. Joe discussed how he, Rick Almeida, and Ken Tepper launched the company in the months after 9/11 and how the acquisition came about. A.J. provides some background on the acquisition and explains why the companies’ tools are complementary.
Elementary Mr. Watson: Retro Routers vs. Modern Boards—The Silent Struggle on Your Screen
06/26/2025 | John Watson -- Column: Elementary, Mr. WatsonThere's a story about a young woman preparing a holiday ham. Before putting it in the pan, she cuts off the ends. When asked why, she shrugs and says, "That's how my mom always did it." She asks her mother, who gives the same answer. Eventually, the question reaches Grandma, who laughs and says, "Oh, I only cut the ends off because my pan was too small." This story is a powerful analogy for how many PCB designers approach routing today.
Siemens Turbocharges Semiconductor and PCB Design Portfolio with Generative and Agentic AI
06/24/2025 | SiemensAt the 2025 Design Automation Conference, Siemens Digital Industries Software today unveiled its AI-enhanced toolset for the EDA design flow.
Cadence AI Autorouter May Transform the Landscape
06/19/2025 | Andy Shaughnessy, Design007 MagazinePatrick Davis, product management director with Cadence Design Systems, discusses advancements in autorouting technology, including AI. He emphasizes a holistic approach that enhances placement and power distribution before routing. He points out that younger engineers seem more likely to embrace autorouting, while the veteran designers are still wary of giving up too much control. Will AI help autorouters finally gain industry-wide acceptance?
Beyond Design: The Metamorphosis of the PCB Router
06/18/2025 | Barry Olney -- Column: Beyond DesignThe traditional PCB design process is often time-consuming and labor-intensive. Routing a complex PCB layout can consume up to 30% of a designer’s time, and addressing this issue is not straightforward. We have all encountered this scenario: You spend hours setting the constraints and finally hit the Go button, only to be surprised by the lack of visual appeal and the obvious flaws in the result.