-
- News
- Books
Featured Books
- pcb007 Magazine
Latest Issues
Current IssueThe Hole Truth: Via Integrity in an HDI World
From the drilled hole to registration across multiple sequential lamination cycles, to the quality of your copper plating, via reliability in an HDI world is becoming an ever-greater challenge. This month we look at “The Hole Truth,” from creating the “perfect” via to how you can assure via quality and reliability, the first time, every time.
In Pursuit of Perfection: Defect Reduction
For bare PCB board fabrication, defect reduction is a critical aspect of a company's bottom line profitability. In this issue, we examine how imaging, etching, and plating processes can provide information and insight into reducing defects and increasing yields.
Voices of the Industry
We take the pulse of the PCB industry by sharing insights from leading fabricators and suppliers in this month's issue. We've gathered their thoughts on the new U.S. administration, spending, the war in Ukraine, and their most pressing needs. It’s an eye-opening and enlightening look behind the curtain.
- Articles
- Columns
- Links
- Media kit
||| MENU - pcb007 Magazine
Ventec International Group Earns ISO 9001:2015 Certification for its German Facility
June 28, 2016 | Ventec International GroupEstimated reading time: 2 minutes
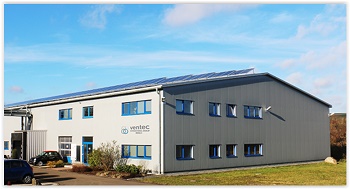
Ventec International Group, a world leader in the production of polyimide & high reliability epoxy laminates and prepregs, is proud to announce that its Central European facility located in Kirchheimbolanden, Germany has received certification under the ISO 9001:2015 quality management standard.
The nearly 3000sqm manufacturing, distribution and sales facility in Germany is the company's latest location within its global network of manufacturing and service centers in Asia, Europe and the USA to receive the ISO 9001:2015 quality standard. ISO 9001:2015 is an internationally recognized standard that specifies requirements for a quality management system (QMS). The standard helps organizations consistently meet the needs of customers and other key stakeholders in both the delivery and continuous improvement of products and services.
PCB fabrication customers can continue to rely on Ventec's fully accredited supply chain for high reliability laminates and pre-pregs. From manufacture through fabrication and delivery, Ventec's high quality product portfolio of polyimides, high reliability FR4 and its latest 'tec-speed' range of high speed/low loss materials are all covered by the accreditation.
"Receiving the ISO 9001:2015 certification at our German facility is another key milestone in our roadmap to offer a full complement of PCB base-products and service options for our customers," said Thomas Michels, Managing Director Europe. "In addition to providing products and solutions that adhere to the stringent quality requirements expected from our customers, Ventec takes great pride in helping our customers around the world to optimize their operational efficiency to better serve their customers."
"Today, our customers are faced with a significantly more competitive environment with tighter regulatory demands across industries," said Mark Goodwin, COO Ventec International Group. "They are looking to strategically partner with companies like Ventec for the supply of reliable materials and services to increase quality and lower their operating costs as a differentiated business model to maximize their own resources. By earning ISO 9001:2015 and other certifications such as AS9100 Rev C for aerospace and ISO/TS16949 for automotive, Ventec can offer our customers the highest possible quality standards and cost structure transformation through an improved and fully controlled supply chain, innovation and long term strategic partnerships."
For more information about Ventec’s solutions and the company’s wide variety of products, please click here.
About Ventec International Group
With volume manufacturing facilities and HQ in Suzhou China, Ventec International specializes in advanced copper clad glass reinforced and metal backed substrates for the PCB industry. With distribution locations and quick-turn CCL manufacturing sites in both the US and Europe, Ventec International is a premier supplier to the Global PCB industry.
Suggested Items
The Evolution of Picosecond Laser Drilling
06/19/2025 | Marcy LaRont, PCB007 MagazineIs it hard to imagine a single laser pulse reduced not only from nanoseconds to picoseconds in its pulse duration, but even to femtoseconds? Well, buckle up because it seems we are there. In this interview, Dr. Stefan Rung, technical director of laser machines at Schmoll Maschinen GmbH, traces the technology trajectory of the laser drill from the CO2 laser to cutting-edge picosecond and hybrid laser drilling systems, highlighting the benefits and limitations of each method, and demonstrating how laser innovations are shaping the future of PCB fabrication.
Day 2: More Cutting-edge Insights at the EIPC Summer Conference
06/18/2025 | Pete Starkey, I-Connect007The European Institute for the PCB Community (EIPC) summer conference took place this year in Edinburgh, Scotland, June 3-4. This is the third of three articles on the conference. The other two cover Day 1’s sessions and the opening keynote speech. Below is a recap of the second day’s sessions.
Day 1: Cutting Edge Insights at the EIPC Summer Conference
06/17/2025 | Pete Starkey, I-Connect007The European Institute for the PCB Community (EIPC) Summer Conference took place this year in Edinburgh, Scotland, June 3-4. This is the second of three articles on the conference. The other two cover the keynote speeches and Day 2 of the technical conference. Below is a recap of the first day’s sessions.
Preventing Surface Prep Defects and Ensuring Reliability
06/10/2025 | Marcy LaRont, PCB007 MagazineIn printed circuit board (PCB) fabrication, surface preparation is a critical process that ensures strong adhesion, reliable plating, and long-term product performance. Without proper surface treatment, manufacturers may encounter defects such as delamination, poor solder mask adhesion, and plating failures. This article examines key surface preparation techniques, common defects resulting from improper processes, and real-world case studies that illustrate best practices.
RF PCB Design Tips and Tricks
05/08/2025 | Cherie Litson, EPTAC MIT CID/CID+There are many great books, videos, and information online about designing PCBs for RF circuits. A few of my favorite RF sources are Hans Rosenberg, Stephen Chavez, and Rick Hartley, but there are many more. These PCB design engineers have a very good perspective on what it takes to take an RF design from schematic concept to PCB layout.