-
- News
- Books
Featured Books
- pcb007 Magazine
Latest Issues
Current IssueSales: From Pitch to PO
From the first cold call to finally receiving that first purchase order, the July PCB007 Magazine breaks down some critical parts of the sales stack. To up your sales game, read on!
The Hole Truth: Via Integrity in an HDI World
From the drilled hole to registration across multiple sequential lamination cycles, to the quality of your copper plating, via reliability in an HDI world is becoming an ever-greater challenge. This month we look at “The Hole Truth,” from creating the “perfect” via to how you can assure via quality and reliability, the first time, every time.
In Pursuit of Perfection: Defect Reduction
For bare PCB board fabrication, defect reduction is a critical aspect of a company's bottom line profitability. In this issue, we examine how imaging, etching, and plating processes can provide information and insight into reducing defects and increasing yields.
- Articles
- Columns
- Links
- Media kit
||| MENU - pcb007 Magazine
Happy’s Essential Skills: Design for Manufacturing and Assembly, Part 1
June 29, 2016 | Happy HoldenEstimated reading time: 9 minutes
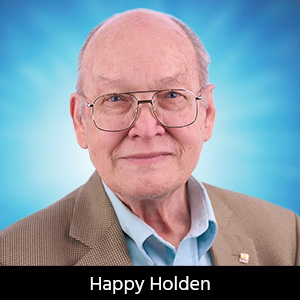
Advances in interconnection technologies have occurred in response to the evolution of component packages, electronic technology and increasing complex functions. Therefore, it comes as no surprise that various forms of printed wiring remain the most popular and cost-effective method of interconnections.
Manufacturing, assembly and test technologies have responded by improvements in their technologies. These increased capabilities have made selection of technologies, design rules and features so complex that a new function has developed to allow for the prediction and selection of design parameters and performance versus manufacturing costs. This is the planning for design, fabrication and assembly. This activity has also been called design for manufacturing and assembly (DFM/A) or sometimes predictive engineering. It is essentially the selection of design features and options that promote cost-competitive manufacturing, assembly, and test practices. Later in this column, I will offer a process to define producibility unique to each design or manufacturing process.
The purpose of this column is to provide information, concepts, and processes that lead to a thoughtfully and competitively designed printed circuit, ensuring that all pertinent design and layout variables have been considered.
Originators: Dewhurst & Boothroyd
Modern DFMA stems from the ideas of university professors Goefrey Dewhurst at University of Massachusetts -Amherst and Jeffery Boothroyd at University of Rhode Island [1]. These Manufacturing Engineering professors came up with the concept that you could predict the assembly time, dificulty and cost by cateloging and summing all the kinematic actions it takes during assembly. This concept became so accurate that it was used to predict assembly while a product was still in the design phase. Thus as a predictive metric, it became Design for Manufacturing—DfM. Today this technology is taught in universities and used by most large OEMs around the world. The Dewhurst & Boothroyd software (Table 1 and Figures 1a & b) consists of:
The D&B techniques consist of analyzing an assembly for these features:
- The need for this part
- How many fasteners are required
- The number of different fastener types
- The number of difficult-to-assemble parts or subassemblies
- The number of motions and twist/turns involved in each assembly step
- The role of tooling and fixturing
The resulting analysis shows a:
- Total part count
- Theoretical minimum of parts or preassembled item (Pmin)
- Assembly efficiency (ease of assembly—AE)
- Assembly time
The analysis uses software to measure:
- Prototype evaluations based on either actual or 3D models using Boothroyd and Dewhurst method.
- Pmin is a measure of the complexity of the product. In general, the more functionality there is in a product, the higher the Pmin value.
- Assembly Efficiency (AE) is a ratio of the theoretical minimum number of parts (Pmin) to the estimated assembly time. An approximation is used to compute AE (2.933 seconds per part), so AE values are used for relative comparisons only.
Table 1: The Dewhurst & Boothroyd DFMA software.
Figure 1a: The Dewhurst & Boothroyd DFMA software.
Figure 1b: The Dewhurst & Boothroyd DFMA software.
Page 1 of 4
Suggested Items
Tata Electronics, Bosch Sign MoU for Strategic Collaboration in Electronics and Semiconductor Manufacturing
07/18/2025 | Tata ElectronicsTata Electronics, a leading player in the Indian electronics and semiconductor manufacturing sector, and Robert Bosch GmbH, a leading global supplier of technology and services, announced that they have signed a Memorandum of Understanding (MoU) to collaborate on several key areas within the electronics and semiconductor industries.
HANZA Accelerates the LYNX Program Through Acquisition of Defense Manufacturer
07/18/2025 | HANZAHANZA AB has signed an agreement to acquire the contract manufacturing division of Milectria, a group of companies focused on the defense sector.
NEOTech’s Agave 1 Facility Earns AS9100 Certification for Commercial Aerospace Manufacturing Excellence
07/17/2025 | NEOTechNEOTech, a premier provider of electronic manufacturing services (EMS), integrated design engineering, and advanced supply chain solutions for the aerospace and defense, medical device, and high-tech industrial markets, proudly announces that its Agave 1 manufacturing facility in Juarez, Mexico has officially received AS9100 certification.
Libra Industries Launches In-House High Precision Underfill Capabilities
07/17/2025 | Libra IndustriesLibra Industries, a leading provider of systems integration and electronics manufacturing services (EMS), is excited to announce the addition of high-precision underfill to its in‑house manufacturing capabilities.
Fraunhofer IPMS, DIVE Optimize Semiconductor Processes with Cutting-Edge Measurement System
07/17/2025 | Fraunhofer IPMSThe Fraunhofer Institute for Photonic Microsystems IPMS, in collaboration with DIVE imaging systems GmbH, has achieved a major milestone in resource-efficient semiconductor manufacturing.