-
- News
- Books
Featured Books
- pcb007 Magazine
Latest Issues
Current IssueThe Hole Truth: Via Integrity in an HDI World
From the drilled hole to registration across multiple sequential lamination cycles, to the quality of your copper plating, via reliability in an HDI world is becoming an ever-greater challenge. This month we look at “The Hole Truth,” from creating the “perfect” via to how you can assure via quality and reliability, the first time, every time.
In Pursuit of Perfection: Defect Reduction
For bare PCB board fabrication, defect reduction is a critical aspect of a company's bottom line profitability. In this issue, we examine how imaging, etching, and plating processes can provide information and insight into reducing defects and increasing yields.
Voices of the Industry
We take the pulse of the PCB industry by sharing insights from leading fabricators and suppliers in this month's issue. We've gathered their thoughts on the new U.S. administration, spending, the war in Ukraine, and their most pressing needs. It’s an eye-opening and enlightening look behind the curtain.
- Articles
- Columns
- Links
- Media kit
||| MENU - pcb007 Magazine
Standard of Excellence: The Future is in Fine lines
July 11, 2016 | John Bushie, American Standard CircuitsEstimated reading time: 4 minutes
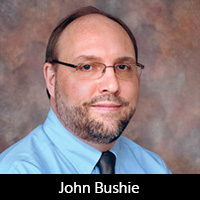
The age of much finer lines and spaces is upon us. After years of slowly moving towards this technology our customers are now demanding that all of us provide them with fine lines and spaces. Our new trend in electronics is for denser and denser circuitry on smaller and smaller real estate. Let’s face it, you just have to look at your typical smartwatch to realize you have an entire computer on your wrist; medical electronics where you have to build a small computer so small that you swallow it; a hearing aid so small that you can barely see it. This is where the world is not only going, but is actually there today.
And yes, these products dictate the need for fine lines, which in turn can be very challenging for those of us building these products. The routing of the lines between pads and vias necessitates this in localized areas as well as the drive to greater layer counts and subsequently thinner cores. All of this while maintaining 50Ω impedance. This is generally where lower Dk laminates can be of benefit to the designer and subsequently the fabricator. It allows one to use a wider line/space while maintaining the required impedance value.
Currently fine lines for standard production are 3-mil lines and 3-mil spaces (3/3). While the technology exists for ≤ 2.6-mil lines, achieving the surface finish necessary for achieving them reliably through imaging has been difficult. Fortunately, with the advent of improved low etch surface preparations, this should allow these ≤2.6-mil lines to be consistently producible.
I can’t speak for other shops, but in my opinion the greatest issues don’t typically lie in the ability to image these types of geometries. The larger issues are mechanical as to whether you can use the thinner copper clad materials as well as reliably etch down in between the ever-decreasing spaces between fine lines. So 4-mil lines and spaces are considered the standard nominal or “easy” product. This is quickly moving toward 3/3 as the norm.
Once again, the real challenge is not just in imaging the product. While there have been great improvements in the imaging areas with the widespread use of LDI and newer, thinner, dry film photo-resists, the larger challenge for us is typically related to the chemical etching to form the individual traces. Since most designs utilize via-in-pad to increase density and allow the use of these finer pitch components, the added copper required for via fill exacerbates the etching issues. Couple this with the increased use of sequential laminations requiring plated sub-assemblies. This extra surface plating increases the amount of copper that is required to be etched through to create the 3-mil spaces. Thus we have had to get creative in our ability to planarize and partial button plate most PCBs having these requirements. All of these added mechanical operations require precise control to minimize the impact on dimensional stability to avoid subsequent registration issues for later processes.
Obviously, controlling the amount of surface copper is paramount. Whether by careful planarization or partial plating operations.
One good thing is that by using 1.3-mil (30 µm) dry films and the use of 16kw and higher LDI equipment, the photoimaging is quite easy at this time. This makes fine lines and spaces fairly simple to produce on print and etch innerlayers if the copper cladding is fine enough. The larger issue comes when producing these types of lines/spaces on the outer layers of these packages.
When talking to designers I urge them to start with the thinnest copper readily available. Currently that would be ¼-oz. copper foil; however, on core constructions this is not always possible. I recommend avoiding sequential constructions when possible, as I’m sure most of you would if the design would allow, and finally, be aware of the added copper plating that each one of the via fill and sequential lamination cycles will add. These all work against the ability to readily realize finer lines and spaces.
Finally, the drive will always be to higher density in lines and layers. So this will effectively drive the lines and spaces down to physical or chemical limitations in the abilities to define (etch) these types of features.
This is where we are with this technology today. Not everyone can do it but most companies I know are headed in that direction. Frankly, at some point we are going to need to develop newer techniques beyond what are commonly used today.
The fact of the matter is that electronics just like the world are getting smaller all the time and we in the PCB industry are going to have to keep up and if want to support that trend.
All I can say is stay tuned for that.
John Bushie is ASC's Application Engineering Manager and is also a Process Engineering Specialist. To contact Bushie, click here.
Suggested Items
I-Connect007 Editor’s Choice: Five Must-Reads for the Week
07/11/2025 | Andy Shaughnessy, Design007 MagazineThis week, we have quite a variety of news items and articles for you. News continues to stream out of Washington, D.C., with tariffs rearing their controversial head again. Because these tariffs are targeted at overseas copper manufacturers, this news has a direct effect on our industry.I-Connect007 Editor’s Choice: Five Must-Reads for the Week
Digital Twin Concept in Copper Electroplating Process Performance
07/11/2025 | Aga Franczak, Robrecht Belis, Elsyca N.V.PCB manufacturing involves transforming a design into a physical board while meeting specific requirements. Understanding these design specifications is crucial, as they directly impact the PCB's fabrication process, performance, and yield rate. One key design specification is copper thieving—the addition of “dummy” pads across the surface that are plated along with the features designed on the outer layers. The purpose of the process is to provide a uniform distribution of copper across the outer layers to make the plating current density and plating in the holes more uniform.
Trump Copper Tariffs Spark Concern
07/10/2025 | I-Connect007 Editorial TeamPresident Donald Trump stated on July 8 that he plans to impose a 50% tariff on copper imports, sparking concern in a global industry whose output is critical to electric vehicles, military hardware, semiconductors, and a wide range of consumer goods. According to Yahoo Finance, copper futures climbed over 2% following tariff confirmation.
Happy’s Tech Talk #40: Factors in PTH Reliability—Hole Voids
07/09/2025 | Happy Holden -- Column: Happy’s Tech TalkWhen we consider via reliability, the major contributing factors are typically processing deviations. These can be subtle and not always visible. One particularly insightful column was by Mike Carano, “Causes of Plating Voids, Pre-electroless Copper,” where he outlined some of the possible causes of hole defects for both plated through-hole (PTH) and blind vias.
Trouble in Your Tank: Can You Drill the Perfect Hole?
07/07/2025 | Michael Carano -- Column: Trouble in Your TankIn the movie “Friday Night Lights,” the head football coach (played by Billy Bob Thornton) addresses his high school football team on a hot day in August in West Texas. He asks his players one question: “Can you be perfect?” That is an interesting question, in football and the printed circuit board fabrication world, where being perfect is somewhat elusive. When it comes to mechanical drilling and via formation, can you drill the perfect hole time after time?