-
- News
- Books
Featured Books
- design007 Magazine
Latest Issues
Current IssueAll About That Route
Most designers favor manual routing, but today's interactive autorouters may be changing designers' minds by allowing users more direct control. In this issue, our expert contributors discuss a variety of manual and autorouting strategies.
Creating the Ideal Data Package
Why is it so difficult to create the ideal data package? Many of these simple errors can be alleviated by paying attention to detail—and knowing what issues to look out for. So, this month, our experts weigh in on the best practices for creating the ideal design data package for your design.
Designing Through the Noise
Our experts discuss the constantly evolving world of RF design, including the many tradeoffs, material considerations, and design tips and techniques that designers and design engineers need to know to succeed in this high-frequency realm.
- Articles
- Columns
- Links
- Media kit
||| MENU - design007 Magazine
Freedom CAD: Navigating the Unpredictable Design Marketplace
October 26, 2016 | Barry Matties, I-Connect007Estimated reading time: 15 minutes
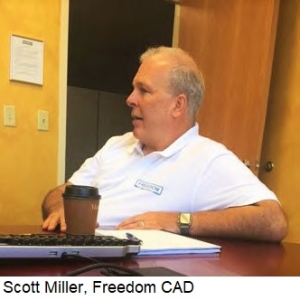
As COO of the design service bureau Freedom CAD, Scott Miller has a front-row seat to the challenges currently plaguing designers and the design community as a whole. He shared his view of the industry with me recently, offering insights on the importance of picking the right partners and customer relationships in an unforgiving and sometimes unpredictable design marketplace.
Barry Matties: First, for a little context, why don't you tell us a little bit about Freedom CAD.
Scott Miller: Freedom CAD is a premier design service company oriented toward printed circuit board design. Our services include engineering related to PCB design. So, electrical and mechanical engineering, PCB layout, as well as peripheral services like signal integrity, power integrity, and schematic integrity. We are also able to provide customers with a full turnkey solution through partnering relationships with contract manufacturers to take what I like to call getting from “CAD to the Lab.” By providing this turnkey service, we can get prototypes into the customers’ hands quickly and seamlessly for testing and debugging.
Matties: Being a service company, you obviously get a chance to see a lot of different design challenges or just challenges in general from a lot of different applications. What do you think is the greatest trend or challenge that you see in design today?
Miller: It's a combination of density and power. We're constantly being pushed to do things in tighter spaces with higher densities, higher pin counts and complex power requirements. There's a lot of influence that takes place because of those, whether it be signal integrity or power integrity. These are the things that push us technology-wise.
Matties: From a customer’s point of view, are they typically people that don't have design in-house, or is it a combination of people with design but not the capacity? What does that look like?
Miller: It’s all of the above. I kind of group it into three categories. We have customers that have no in-house capability. They are architects of technology and they outsource everything. They may have an engineer or two, but then they want people to execute on the high-level engineering. We also have customers that have in-house capabilities, but they staff to meet their average demand and when they get into peak demand, they have insufficient capacity. They look to augment that internal skillset with outside resources to satisfy that peak demand. Then the surge goes away, and the cost goes away.
Then we have customers that simply have reached the point where they don't have a skillset or knowledge of the technology. Rather than take on the risks of doing it wrong, they look outside to find people that know how to do it well. You'd be surprised. We've done some interesting things for companies that are very capable, but have come to us for a variety of reasons. Sometimes it's the technology, or the signal speed at which they need to operate are outside of their experience. Sometimes, their internal processes are just too slow, or there are obstacles to getting things done, so they'll outsource to us.
Matties: There’s probably a large area of the market where the skill doesn't match up to where it needs to be.
Miller: Yes, we have industrial customers who have been doing business in a certain way. Think about this in terms of the water meter business. If you design water meters, now all of a sudden water meters have Bluetooth and digital connections, because they want their drivers to be able to drive by and capture their readings without getting out of the truck. So now, these guys who have been very capable at building mechanical or analog water meters are now pushed into digital and RF technology, which is outside of their expertise. That's just one example, which is happening a lot in the industrial market.
Matties: The question that comes to mind is, do they even know they don't have the skill? We live in these vacuums. Will people come in for a sanity check?
Miller: What I see on a regular basis is companies that say, “We see this competitor and they're doing this and we need to be able to do that.” Some of it is pushed by innovation and outside of their box, and some of it is people who are the innovators and they recognize that they don't have that new skillset.
Matties: Now for you, what is your sweet spot of the three categories? Which one fits the best?
Miller: Traditionally we've been tied to the companies that have internal capabilities and we augment their teams. We do that well because we pride ourselves on our communications and our skillsets. The differentiator is being seamless. If you can work with a company that has an internal team, and you can be as seamless as possible to them, they feel confident about working with you. In general, that tends to be the biggest market for us—companies where they used to have 10 designers and now they're down to two. Because they only have two, they're able to keep up with the average, everyday stuff, but when they get into the big programs they need to count on us.
That puts pressure on our business, because it's a sine wave of demand. The peak loads don't happen all the time. At Freedom CAD, we see scale as a really important part of our business strategy. We obviously want to hire the best designers we can.
Matties: You have to do that.
Miller: We want to compete at the highest level, but we also have been purposefully driving scale. That scale gives you the ability to take on more customers and more programs, so that those sine waves hopefully don't line up and you've got one customer at a peak when another customer is at a valley. If you're too small, you can get devastated by those valleys, particularly if they're extended.
Matties: You can get devastated by the peaks, too.
Miller: Right. You can be overwhelmed, and then you can lose a customer when you're not in a position to say yes when they ask.
Matties: It's a fine balancing act there for you.
Miller: It's a tough act.
Matties: How do you project this? How do you look forward?
Miller: I'd love to tell you that our customers are wonderful and they tell us everything [laughs]. I'll talk to a customer on Tuesday, and I'll say “Hey, anything in the pipeline?” “No, I don't have anything.” On Thursday, they're calling me saying, “Hey, do you have somebody available?” There's no visibility. There are some customers who will give you a horizon, and then it's a matter of “We're going to have this project that’s going to start in October.” Then October turns into February. You just constantly have to keep an ear to the ground and talk to your customers so you have some semblance of what's going on.
Page 1 of 3
Suggested Items
The Evolution of Picosecond Laser Drilling
06/19/2025 | Marcy LaRont, PCB007 MagazineIs it hard to imagine a single laser pulse reduced not only from nanoseconds to picoseconds in its pulse duration, but even to femtoseconds? Well, buckle up because it seems we are there. In this interview, Dr. Stefan Rung, technical director of laser machines at Schmoll Maschinen GmbH, traces the technology trajectory of the laser drill from the CO2 laser to cutting-edge picosecond and hybrid laser drilling systems, highlighting the benefits and limitations of each method, and demonstrating how laser innovations are shaping the future of PCB fabrication.
Day 2: More Cutting-edge Insights at the EIPC Summer Conference
06/18/2025 | Pete Starkey, I-Connect007The European Institute for the PCB Community (EIPC) summer conference took place this year in Edinburgh, Scotland, June 3-4. This is the third of three articles on the conference. The other two cover Day 1’s sessions and the opening keynote speech. Below is a recap of the second day’s sessions.
Day 1: Cutting Edge Insights at the EIPC Summer Conference
06/17/2025 | Pete Starkey, I-Connect007The European Institute for the PCB Community (EIPC) Summer Conference took place this year in Edinburgh, Scotland, June 3-4. This is the second of three articles on the conference. The other two cover the keynote speeches and Day 2 of the technical conference. Below is a recap of the first day’s sessions.
Preventing Surface Prep Defects and Ensuring Reliability
06/10/2025 | Marcy LaRont, PCB007 MagazineIn printed circuit board (PCB) fabrication, surface preparation is a critical process that ensures strong adhesion, reliable plating, and long-term product performance. Without proper surface treatment, manufacturers may encounter defects such as delamination, poor solder mask adhesion, and plating failures. This article examines key surface preparation techniques, common defects resulting from improper processes, and real-world case studies that illustrate best practices.
RF PCB Design Tips and Tricks
05/08/2025 | Cherie Litson, EPTAC MIT CID/CID+There are many great books, videos, and information online about designing PCBs for RF circuits. A few of my favorite RF sources are Hans Rosenberg, Stephen Chavez, and Rick Hartley, but there are many more. These PCB design engineers have a very good perspective on what it takes to take an RF design from schematic concept to PCB layout.