-
- News
- Books
Featured Books
- pcb007 Magazine
Latest Issues
Current IssueThe Hole Truth: Via Integrity in an HDI World
From the drilled hole to registration across multiple sequential lamination cycles, to the quality of your copper plating, via reliability in an HDI world is becoming an ever-greater challenge. This month we look at “The Hole Truth,” from creating the “perfect” via to how you can assure via quality and reliability, the first time, every time.
In Pursuit of Perfection: Defect Reduction
For bare PCB board fabrication, defect reduction is a critical aspect of a company's bottom line profitability. In this issue, we examine how imaging, etching, and plating processes can provide information and insight into reducing defects and increasing yields.
Voices of the Industry
We take the pulse of the PCB industry by sharing insights from leading fabricators and suppliers in this month's issue. We've gathered their thoughts on the new U.S. administration, spending, the war in Ukraine, and their most pressing needs. It’s an eye-opening and enlightening look behind the curtain.
- Articles
- Columns
- Links
- Media kit
||| MENU - pcb007 Magazine
A Scientific Response to Mr. Laminate Tells All
November 29, 2016 | Mark Goodwin and Bill Wang, Ventec International GroupEstimated reading time: 3 minutes
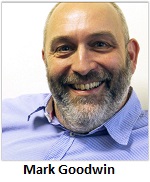
We read with interest Doug Sober’s recent Mr. Laminate Tells All column, The Certification of IPC-4101D Polyimide Base Materials: Buyer Beware.
The article raises interesting questions about the IPC 4101 classification system, primarily, how is a pure resin defined?
For thermosetting materials, the “resin system” includes at least a resin and a curing system, which can take many forms—can this be defined as pure?
“Purity” is a term generally applied to single compounds, especially in inorganic chemistry. To broadly apply this term to complex organic resin systems, which may contain multiple curing chemistries, inert and active fillers, and flame retardant components, is stretching the term beyond the breaking point.
Let us consider materials classified under IPC 4101/126 for example. The specification sheet states the following:
The primary resin system is listed as “Epoxy,” with a secondary of multifunctional epoxy or modified epoxy or non-epoxy (max. wt. 5%). However, for base materials’ manufacturers to meet the performance requirements of lead-free FR-4 and high decomposition temperature, it has been standard practice for base materials manufacturers to replace the previously common dicyandiamide curing element with a phenolic resin in /126 materials. The phenolic resin element is typically present in double-digit weight percentage proportions; these products are openly referred to as “phenolic cured epoxies.” If the argument about purity of resins were applied in the same way as in the polyimide example, then all manufacturers of /126 materials should be declared as having a secondary resin system outside of the specification requirements, and would therefore be non-compliant.
The only argument that allows base materials manufacturers to claim /126 compliance with such a high percentage of non-compliant secondary resins relates to the nature of the organic molecule. The argument is that many species may be used in the formulation, but in the final reacted state there is one molecule, which had epoxy functionality prior to curing (by definition, the presence of an epoxy functional group), and can therefore be correctly classed as an epoxy resin. To quote the article, “there is only one big molecule with the largest portion being the polyimide functionality. So it is a pure polyimide at that point. That argument does not hold any water…” We can just as easily replace the term “polyimide” with “epoxy” and we have the statement “there is only one big molecule with the largest portion being the epoxy functionality. So it is a pure epoxy at that point. That argument does not hold any water…” By inference, the author must also support the argument to disbar /126 materials that use a phenolic curing element, which is most, if not all of them.
Polyimide is, by definition, a polymer that contains imide groups. Polyimide resins form a family of chemistries, aliphatic or aromatic; they may be thermoplastic or form part of a thermosetting system and may or may not include flame retardant components. Using the same arguments above, for epoxy, the final reacted state is one molecule that contains a polymer that contained a functional group consisting of two acyl groups bound to nitrogen (an imide). It is just the same argument for /126 epoxies above; what is true for /126 must also be true for /40 /41.
To reinforce this distinction one should also not forget that in the final condition, no functional epoxy or imide groups exist at all as they will have all reacted as part of the crosslinking process. It is truly “one big molecule.”
Far from “using their own rules for substitutions” and saying “you (IPC) cannot stop us,” the laminators concerned (of which Ventec is just one) are applying a consistent and scientifically correct approach to the formulation of both polyimide and epoxy resin systems. And if a “special case” is being argued for /40/41 materials that somehow does not apply to /126 materials, then the buyer must truly beware of using the IPC 4101 slash sheet classification system at all.
Mark Goodwin is CCO, EMEA & Europe with Ventec International Group.
Bill Wang is technical director with Ventec International Group.
Suggested Items
Advancing Aerospace Excellence: Emerald’s Medford Team Earns Space Addendum Certification
06/30/2025 | Emerald TechnologiesWe’re thrilled to announce a major achievement from our Medford, Oregon facility. Andy Abrigo has officially earned her credentials as a Certified IPC Trainer (CIT) under the IPC J-STD-001 Space Addendum, the leading industry standard for space and military-grade electronics manufacturing.
Magnalytix and Foresite to Host Technical Webinar on SIR Testing and Functional Reliability
06/26/2025 | MAGNALYTIXMagnalytix, in collaboration with Foresite Inc., is pleased to announce an upcoming one-hour Webinar Workshop titled “Comparing SIR IPC B-52 to Umpire 41 Functional & SIR Test Method.” This session will be held on July 24, 2025, and is open to professionals in electronics manufacturing, reliability engineering, and process development seeking insights into new testing standards for climatic reliability.
IPC Rebrands as Global Electronics Association: Interview With Dr. John W. Mitchell
06/22/2025 | Marcy LaRont, I-Connect007Today, following a major announcement, IPC is embracing the rapid advancement of technology with a bold decision to change its name to the Global Electronics Association. This name more accurately reflects the full breadth of its work and the modern realities of electronics manufacturing. In this exclusive interview, Global Electronics Association President and CEO Dr. John W. Mitchell shares the story behind the rebrand: Why now, what it means for the industry, and how it aligns with the organization’s mission.
Global Electronics Association Debuts; New Name Elevates IPC’s 70-Year Legacy as Voice of $6 Trillion Electronics Industry
06/25/2025 | Global Electronics AssociationToday begins a new chapter for IPC as it officially becomes the Global Electronics Association, reflecting its role as the voice of the electronics industry. Guided by the vision of “Better electronics for a better world,” the Global Electronics Association (electronics.org) is dedicated to enhancing supply chain resilience and promoting accelerated growth through engagement with more than 3,000 member companies, thousands of partners, and dozens of governments across the globe.
I-Connect007 Editor’s Choice: Five Must-Reads for the Week
06/20/2025 | Andy Shaughnessy, I-Connect007It’s been a busy week in this industry, and we have news and articles from the PCB design, fabrication and assembly communities. Some of this news is out of this world. We may be losing the high ground—the really high ground. Columnist Jesse Vaughan explains how the U.S. seems to be falling behind in space, and how this could affect our ability to defend ourselves in the future. We have an update on the U.S.-China tariff talks, which seem to be moving forward, though sometimes at a snail’s pace.