-
- News
- Books
Featured Books
- smt007 Magazine
Latest Issues
Current IssueWhat's Your Sweet Spot?
Are you in a niche that’s growing or shrinking? Is it time to reassess and refocus? We spotlight companies thriving by redefining or reinforcing their niche. What are their insights?
Moving Forward With Confidence
In this issue, we focus on sales and quoting, workforce training, new IPC leadership in the U.S. and Canada, the effects of tariffs, CFX standards, and much more—all designed to provide perspective as you move through the cloud bank of today's shifting economic market.
Intelligent Test and Inspection
Are you ready to explore the cutting-edge advancements shaping the electronics manufacturing industry? The May 2025 issue of SMT007 Magazine is packed with insights, innovations, and expert perspectives that you won’t want to miss.
- Articles
- Columns
- Links
- Media kit
||| MENU - smt007 Magazine
Estimated reading time: 3 minutes
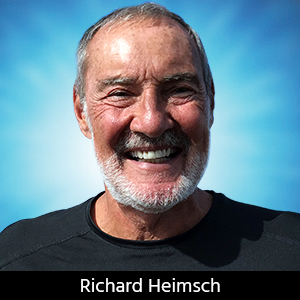
PCBs are MSDs
Guidelines for the proper storage, handling and moisture protection of electronic components can be found in IPC standards (IPC/JEDEC J-Std-033C). Though these date back to 1999, there were no published standards for storage and moisture protection for printed boards until 2010, and their proper handling is still often overlooked. But with the correct storage control and the use of suitable drying methods, considerable manufacturing advantages can be gained; PCBs will remain solderable for a much longer time and damage during reflow due to moisture can be eliminated.
The IPC-1601A (2016 revision) Printed Board Handling and Storage Guidelines states that “If process controls are ineffective, and printed boards have absorbed excessive moisture, baking is the most practical remedy.” It goes on to state, “However, baking not only increases cost and cycle time, it can also degrade solderability of the printed board which requires extra handling and increases the likelihood of handling damage or contamination. In general, both the printed board fabricator and the user should strive to avoid baking by practicing effective handling, packaging, storage, and process controls…”
In addition to moisture management at key steps in the fabrication process, 1601 also makes clear that boards should be protectively packaged to limit their exposure to ambient humidity during processing and storage. And packaged only after determining that their moisture content is below the maximum acceptable moisture content (MAMC) level, which is typically between 0.1% and 0.5% moisture weight to resin weight.
The document also states “Baking is not recommended for OSP coatings, as it deteriorates the OSP finish. If baking is deemed necessary, the use of the lowest possible temperature and dwell time is suggested as a starting point.”
Organic solderability preservative (OSP) coatings are among the leading surface finish options in lead free soldering because they provide an attractive combination of solderability, ease of processing and low cost. Compared to alternatives, however, they tend to be the most prone to oxidation. The cause for this lies in the pure copper surface protected only by the OSP coating layer. Under normal climatic conditions in a manufacturing process, after only a few minutes there will be a separation of a water film at the surface (3–5 atom layers). This then starts a diffusion process which leads to a vapor pressure balance through the OSP coat. Baking also accelerates solid diffusion between metals, and increases intermetallic growth. This can lead to a "weak knee" or other solderability issues if the intermetallic layer reaches the surface and oxidizes. Effects upon other finishes (immersion tin, immersion silver, ENIG) are further detailed in the guidelines.
Just as with components, 125°C baking temperatures degrade the solderability of PCBs. 1601 warns that as little as 4–6 hours at that temperature can render HASL finished boards unsolderable. Over the decades that passed since the J-STD-033 standard was created, new technologies were developed and proven to safely reset component floor life using low temperatures and ultra-low humidity without requiring extensive time. These 40–60°C and
The same methods were applied to PCBs, and engineers from the company SMT and Hybrid GmbH published their findings in "Production of Printed Circuit Boards and Systems"1. They stated, "Circuit board manufacturers are extremely hesitant at providing instructions on drying their circuit boards. Information from the ZVEI2 should also be regarded critically. The cardinal problem is the high temperature which is recommended for tempering. If this is applied, the result is often de-lamination and distortion of the circuit boards. Corrosion and the formation of intermetallic phases of the metallic surfaces are also to be expected."
Figure 1: Chart and legend QFP.
Their research investigated “whether gentle drying at 45°C or 60°C and at low relative humidity achieves the same result as tempering at high temperatures.”
They began first with QFP components, which were saturated and then dried in seven different environments, referencing J-STD-033 standards in their report.
They then selected four PCB types and repeated the same procedures of saturation then drying and weighing to 0.1% water weight. This was done using 60°C at
Figure 2: PCB drying chart.
Conclusion
Figure 3: In addition to extending the safe storage time, defects and damage such as popcorning and delamination during the reflow process caused by moisture can be avoided.
Their research was conducted just prior to the publication of IPC 1601, which now provides detailed guidelines for the packaging and storage of PCBs, both from the PCB manufacturer and at the assembler’s manufacturing floor. It also describes the solderabilty risks associated with high temperature baking. Ultra-low RH and low temperatures can significantly mitigate those risks while preventing moisture damage during reflow.
References
1. G. Schubert, Th. Schonfeld, and A. Friedrich, SMT & HYBRID Gmbh, “Drying Printed Circuit Boards,” Production of Printed Circuit Boards and Systems, September 2009.
2. Richtwerte/Empfehlung des ZVEI, Fachverband der Leiterplattenindustrie.
More Columns from More Than Just Dry Air
Controlling Oxidation and Intermetallics in Moisture-sensitive DevicesLong-Term Storage of Electronic Components and Compositions
More Than Just Dry Air: Solutions for Long-term Storage of Electronic Components and Compositions
More Than Just Dry Air: Prodrive Technologies - 4.0 in Action
More Than Just Dry Air: In Pursuit of 4.0
More Than Just Dry Air: Controlling Oxidation and Intermetallics in Moisture-Sensitive Devices