-
- News
- Books
Featured Books
- smt007 Magazine
Latest Issues
Current IssueDo You Have X-ray Vision?
Has X-ray’s time finally come in electronics manufacturing? Join us in this issue of SMT007 Magazine, where we answer this question and others to bring more efficiency to your bottom line.
IPC APEX EXPO 2025: A Preview
It’s that time again. If you’re going to Anaheim for IPC APEX EXPO 2025, we’ll see you there. In the meantime, consider this issue of SMT007 Magazine to be your golden ticket to planning the show.
Technical Resources
Key industry organizations–all with knowledge sharing as a part of their mission–share their technical repositories in this issue of SMT007 Magazine. Where can you find information critical to your work? Odds are, right here.
- Articles
- Columns
Search Console
- Links
- Media kit
||| MENU - smt007 Magazine
X-Ray Inspection of Lead and Lead-Free Solder Joints
July 31, 2017 | Glen Thomas, Ph.D., and Bill Cardoso, Ph.D., Creative Electron Inc.Estimated reading time: 13 minutes
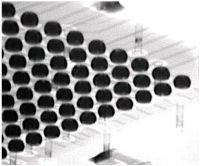
ABSTRACT
X-rays are widely used to inspect solder joints in the electronics industry. Environmental concerns related to the impact of lead waste led the electronics industry to reduce or eliminate the use of lead in their manufacturing processes in 2007. Due to reliability concerns related to the use of lead-free solders in mission critical products, military and aerospace companies have been temporarily exempt from this requirement. However, as the availability of commercially available lead parts becomes scarce, some of the companies in the aerospace and military markets are considering the use of lead-free parts.
As aerospace companies consider the shift to lead-free solder alloys and glues, concerns have been raised about whether their current X-ray inspection and quality-control procedures will still be valid. With lead solder, joints are easily interpreted by the operator or the system imaging software because lead provides excellent image contrasts due to relatively high X-ray absorption compared to that of PCB and component materials. Will this hold true as they shift to lead-free solder compounds?
In this paper, we study how the physics of X-ray requires the change of settings and procedures for an accurate inspection. The atomic number of a material (Z) drives its X-ray absorption. Materials with high Z absorb more X-rays than materials with low Z. Tin (Z = 50), for example, is a common material found in lead-free solders. Lead, on the other hand, has atomic number 82. This difference in atomic numbers—and the different alloys present in the market today—may drive the need to change the settings and modes of the X-ray inspection system to match the chemistry of the solder joints. An accurate X-ray technique can only be achieved once the imaging system can produce similar contrast for both lead and lead-free solder inspection.
INTRODUCTION
It has been over a decade now since environmental concerns over contamination due to lead waste led the electronics industry to migrate solder processes away from the usage of eutectic tin-lead solder and towards utilization of lead-free compounds. Such a process change had several ramifications. The first major impact in the industry was the initial investment in equipment and materials to adapt to RoHS requirements. Another critical impact was the necessity to redesign reflow processes to bring the new assemblies with lead-free solders to an equivalent yield as the industry experienced prior to the migration to lead-free.
Although most companies have successfully moved to lead-free SMT lines, a considerable portion of manufacturers working in aerospace and military programs are still required to use lead solder. These companies routinely use X-ray inspection systems to assess and validate the quality of their assemblies. However, an X-ray inspection system will only be useful in a lead-free world if the changes in solder compounds do not have a significant deleterious effect on its imaging characteristics. To mitigate the concerns related to the inspection migration from lead to lead-free solder, in this paper we provide theoretical and practical studies of some of the effects of lead-free solder on an X-ray imaging capability. This is done primarily by comparison of X-ray attenuation properties for eutectic tin-lead solder and various lead-free solder compounds. We additionally show both actual images of solder joints made with lead and lead-free solder pastes. The conclusion of this analysis is that we found little contrast variation when using lead-free solders, which implies little change in inspectability.
X-RAY GENERATION AND ATTENUATION
X-rays have been used for non-invasive high-resolution imaging of industrial and biological specimens since their discovery in 1895. Recently, a number of new contrast methodologies have emerged which are expanding X-ray's applications to functional as well as structural imaging. Figure 1 shows how the interaction of the X-ray photon with the atom inside the sample are leveraged by the different X-ray inspection techniques.
Figure 1: PTH process window by alloy.
X-rays are generated by accelerating electrons across a high voltage to collide with an anode composed of a high atomic number, high melting point material (commonly tungsten). Interactions between the electrons and the tungsten anode lead to the production of X-rays with a broad energy spectrum. The maximum energy of the X-ray spectrum is determined by the voltage applied in the X-ray tube. As tube voltage increases, the mean X-ray energy and number of photons produced both increase. This is demonstrated in Figure 2A for a tungsten anode operating at two different voltages: 80 and 140kV. The energy of the produced X-rays is an important determinant of their absorption by a given material. This energy spectrum can be modified by filtration through metal filters. Filtration is primarily used to increase the mean energy of the X-ray spectrum by removing low energy photons. Filtration can be used to both reduce radiation dose and improve image quality, and filtration can be optimized depending on the imaging[1]. Microfocus X-ray tubes used in high-end X-ray inspection machines have a small focal spot (area where the electron beam interacts with the anode), which reduces the source function blur (i.e., penumbra blurring) and thereby greatly improves the maximum image resolution. This increased resolution is necessary for imaging small features in electronic assemblies.
Figure 2: X-ray production and attenuation. (A) X-ray energy spectra produced at two different tube voltages: 80 and 140kV. Both the number of photons produced and the mean energy of the spectrum increases with higher voltage. (B) X-ray attenuation as a function of X-ray energy for multiple materials. In general, the X-ray attenuation rapidly drops with increasing X-ray energy. At the K-edge of each material, there is a sharp rise in attenuation due to the photoelectric absorption at that energy.
Page 1 of 5
Suggested Items
KYZEN Focuses on Aqueous Cleaning and Stencil Cleaning at SMTA Wisconsin
04/24/2025 | KYZEN'KYZEN, the global leader in innovative environmentally responsible cleaning chemistries, will exhibit at the SMTA Wisconsin Expo and Tech Forum, scheduled to take place Tuesday, May 6 at the Crowne Plaza Milwaukee Airport. KYZEN will be on-site to provide attendees with information about aqueous cleaning chemistry AQUANOX A4618 and stencil cleaner KYZEN E5631J.
SMTA Bridging the Skills Gap in Arizona
04/24/2025 | Marcy LaRont, I-Connect007One area where SMTA really excels is through its local chapters. On April 16, 2025, I-Connect007's Marcy LaRont attended the Workforce Breakfast during the SMTA Arizona Expo & Tech Forum in Mesa, which featured more than 50 electronics professionals from the local area, including defense OEMs, and others who were attending for the first time. Blackfox and Hyrel Technologies sponsored the event. The keynote presentation featured Sean Denny, a professor at Estrella Mountain Community College, who emphasized a clear need for skilled hand soldering technicians.
IPC Releases Version 2.0 of IPC-2591, Connected Factory Exchange, with Expanded Device Coverage and Smarter Data
04/23/2025 | IPCIPC announces the release of IPC-2591, Connected Factory Exchange (CFX), Version 2.0, the global standard for plug-and-play, machine-to-machine, and machine-to-system communication for digital manufacturing.
ViTrox Marks 25 Years of Innovation with Cutting-Edge Solutions at NEPCON China 2025 in Shanghai
04/18/2025 | ViTrox TechnologiesViTrox, which aims to be the World’s Most Trusted Technology Company, is proud to announce its participation in NEPCON China 2025, taking place from April 22–24, 2025, at Booth #1E45, Shanghai World Expo Exhibition & Convention Centre (SWEECC).
Indium Experts to Present on Power Electronics at PCIM Europe 2025
04/17/2025 | Indium CorporationAs one of the leading materials providers to the power electronics assembly and e-Mobility industries, Indium Corporation experts will share their technical insight and knowledge on a variety of industry-related topics throughout PCIM Europe, May 6-8, in Nuremberg, Germany.