-
- News
- Books
Featured Books
- design007 Magazine
Latest Issues
Current IssueProper Floor Planning
Floor planning decisions can make or break performance, manufacturability, and timelines. This month’s contributors weigh in with their best practices for proper floor planning and specific strategies to get it right.
Showing Some Constraint
A strong design constraint strategy carefully balances a wide range of electrical and manufacturing trade-offs. This month, we explore the key requirements, common challenges, and best practices behind building an effective constraint strategy.
All About That Route
Most designers favor manual routing, but today's interactive autorouters may be changing designers' minds by allowing users more direct control. In this issue, our expert contributors discuss a variety of manual and autorouting strategies.
- Articles
- Columns
- Links
- Media kit
||| MENU - design007 Magazine
Polar Instruments’ Martyn Gaudion Discusses Tools and Books
October 22, 2017 | Andy Shaughnessy, PCBDesign007Estimated reading time: 9 minutes
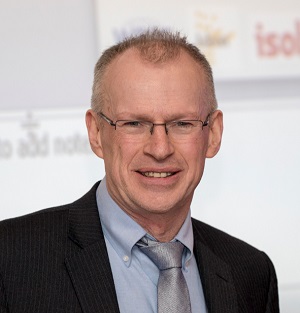
Polar Instruments has pretty been busy lately. In the last year, Managing Director Martyn Gaudion has written two books for I-Connect007, and the company has been working to upgrade its tools, especially library functionality.
I met with Martyn at PCB West. We discussed Polar’s newest tool updates, Martyn’s new side job as an author of technical books, and the continuing growth of the EDA segment, including among young people.
ANDY SHAUGHNESSY: Tell me, Martyn, what's been going on with Polar?
MARTYN GAUDION: Yes, it's been a very busy year and it’s great to be back speaking to you again, Andy. A lot of our customers in the design sector are keen that we have very good library information, but sometimes they are dreaming to a certain extent in that they think if they could perfectly specify the material, they would get the exact PCB they think they're going to get.
And one of the things we think they are overlooking is the fact that PCB fabrication is a manufacturing process; it's not like making a sandwich. You can't disassemble the finished product, because it is a process things happen to the component materials that you put in there, so that what you put in is not exactly what comes out. That's an area we'd like to work on educating designers, because we come under a lot of pressure to say, "You must improve your library, so that what's in the library is what we get.” But we say, "Actually, the only way to get that is to speak to the fabricator, because you need to know what they're going to do to those materials to make a reliable finished product.”
SHAUGHNESSY: You’ve called it the myth of the perfect library.
GAUDION: Right. It’s back to our old broken record, really. We think it's important that the designers establish a relationship with their fabricator, or if not with the fabricator, with a value-added broker who knows enough about fabrication to put two people in touch. What we have done in our tools this year, is we've put our libraries online, so we’ve made it much easier to access materials and put real materials into the stack-up, direct from all the major laminate suppliers. We're adding to that, but what we want to make sure is that we educate our customers and say, "These are the correct data sets for those materials, but once your fabricator purchases those, they're going to process them, and prepare the surface chemically, which helps for one example to adjust the copper to prepare for adhesion, so what you see in the library isn't what appears in your finished product." That's really quite important.
The other area would be developing and really enhancing the high-frequency capability of SpeedStack. At the moment, we've got two field solvers, one for impedance up to 2 gigahertz, and the other one runs up to 50, 60, 70 gigahertz. They link in with our stack-up tool, Speedstack, but, at the moment, Speedstack really stores the principal documentation information for lossless stack, but doesn’t store the roughness, loss tangent and modeling methods for ultra high-speed designs. So it's useful; it documents the information and tells the fabricator what materials they have to choose and how much flexibility they've got. But if an SI engineer wants to use it for multi GHz designs, you need to key a lot more information into the field solver that isn’t archived the stack-up tool. Until now.
So, for 2018, we’ve got a new version of the stack-up tool which will actually do insertion loss calculations as well, so you don't have to go into our Si9000e environment. You can still use Si9000e if you want to do extensive analysis, but you can have all of the graphics , the length of line, the type of dielectric constant or base material, and have that all saved away with every structure in Speedstack Si. It makes it a lot easier for a designer to work backwards and forwards with SI engineers.
The other thing we've done with that, and it’s a request we have very often, is to include the insertion loss graph in the Speedstack printout. So for 2018, we include all the insertion loss graphs in the Speedstack printouts, so that's something that saves people a whole lot of work. They can tell you, "I've got these different signals, these different net classes, and here’s the insertion loss I'm predicting and the allotted budget for each of those structures.”
SHAUGHNESSY: I understand you've written a couple of books now.
Gaudion: Yes, and we're having them printed, so we should have some hardback copies. We're thrilled to have a hardback book that really distills some of the information that I've gathered over the years, and I'd love to personally thank I-Connect007 European Editor Pete Starkey for putting the idea in my head all those years ago. He suggested that, based on the application notes on the Polar website, that I write a column for The PCB Design Magazine, and that column gave me the discipline to put enough chapters together to write a book. It's nice to distill all that together into one book.
It's called The Printed Circuit Designer’s Guide to…Secrets of High-Speed PCBs. It has the kind of things that catch you out, but it’s information that isn’t in the normal textbooks. In fact, the myth of the perfect library could be another chapter which we can talk about further in a future version.
SHAUGHNESSY: I like how you throw in little anecdotes that break it up, because this content can be so dry, even if it's good technical information. I like your story about figuring out why your Audi is smoking, or how picking the right airport is like routing a circuit board.
GAUDION: The point I try to make is that you shouldn't get seduced by the precision that's apparent in the tools, when actually we're working with materials that actually have tolerances. In fact, I was at a seminar on stack-up yesterday given by Bill Hargin from Nan Ya. Someone in the audience asked, "If we have all this technology, why can't I have this stack-up that's plus or minus 1%? I’ve got 10% variation." And Bill said, “You have all these materials that actually need to be pressed, and the copper varies, and everything else, and when you've got 14 layers and they're all pressed together, actually, you should be really pleased that you've got a 10% variation.”
That's really very good, and that's kind of interesting. You can look at all these decimal places and tools and think, "Wow, I can do this accurately," but really what you have to figure out is how much design space you have to work in, you have to center up your processes so that the average is in the middle, and you need to know what kind of yields you’re going to get. That's an example of how computer software can make you think that life is more precise than it really is. Actually, as we push frequencies up, we've all got to start being comfortable dealing with statistics. Most likely, it's going to look like this.
SHAUGHNESSY: It's like that old saying, "We can put a man on the moon; why can't we have 1%?" So, what are your plans for the next couple of years? What do you hope to accomplish?
GAUDION: We've got a huge amount of work in our stack-up tools, so that's the biggest area where I can request more enhancement. I think we can do a lot, but people want to do more with flex-rigid, and they want to do more with high speeds, so that's a big growth area. We see a lot of work as people have pushed into low-loss laminates. That's really nailed the loss issue, but what it's brought to the fore now is that copper roughness is the major driver for loss. While there are very sophisticated ways of modeling it, like the Huray model, it's quite difficult to actually measure the roughness of the copper surface. So there's some areas in terms of data gathering, and actually closing the loop between the model and the measurement. So, we've done a lot of work with our tools where we can import our insertion loss data, not only for our own measurement tools, but also from VNAs. So you can pull a VNA file into our measurement modeling systems, and then you can cross-correlate the measure for the model. So that's an area of interest driving us ahead at the moment.
SHAUGHNESSY: Is there anything else you want to add?
GAUDION: Just to say that the industry appears busy. Appears to be in good shape. For us, it's an unusual situation in that, typically, we sell fairly equally in the U.S., Europe, and Asia, but usually, one market's up, one's down, and actually this year, everybody's up. I've never had that in 25 years, to have all areas going well. That doesn't mean there's something bad coming, but I think it's an indication that automotive, medical, everything has electronics. You see companies in all sorts of areas where we were never involved with before, and suddenly there's electronics in everything. I think there's a general uptick in the amount of electronic content everywhere. All the people who work in the electronics supply chain, like ourselves, seem to be benefiting for the moment. There seemed to be a lull for one but now all this stuff is going to take off.
SHAUGHNESSY: A lot of these people are hiring too.
GAUDION: Yes, we have staff wanting to retire and we need to replace them, and the U.S. office has been growing, and that's really a change for us, and time to do that as well, because the industry is getting gray, and we need to get some young blood in.
SHAUGHNESSY: I've seen a few young people out. Your product specialist, Geoffrey Hazelett, is young and super smart.
GAUDION: Yes, we also have a young intern in her second year, she's doing her EE, and she wants to go into biomedical, so it’s that blend of electronics, and she wants to look into that area. Her name is Regan Garner. It's great to have somebody who's young and enthusiastic and prepared to ask questions, and really take on board some of what we're doing. Her heart lies in a different direction, but it's really good for her to come through and experience what life's like in a niche supplier to the industry.
SHAUGHNESSY: We have some young people working with us now, and they're so excited, they're not jaded. They don't wish it was 1995 again.
GAUDION: Sure. We've been through some bad times. Actually now, there's a lot of positive stuff going on in the industry, so that's really a good change.
SHAUGHNESSY: It’s been great talking with you, Martyn. Thanks for your time.
GAUDION: Thank you, Andy. My pleasure.
Testimonial
"Our marketing partnership with I-Connect007 is already delivering. Just a day after our press release went live, we received a direct inquiry about our updated products!"
Rachael Temple - AlltematedSuggested Items
Trouble in Your Tank: Minimizing Small-via Defects for High-reliability PCBs
08/27/2025 | Michael Carano -- Column: Trouble in Your TankTo quote the comedian Stephen Wright, “If at first you don’t succeed, then skydiving is not for you.” That can be the battle cry when you find that only small-diameter vias are exhibiting voids. Why are small holes more prone to voids than larger vias when processed through electroless copper? There are several reasons.
The Government Circuit: Navigating New Trade Headwinds and New Partnerships
08/25/2025 | Chris Mitchell -- Column: The Government CircuitAs global trade winds continue to howl, the electronics manufacturing industry finds itself at a critical juncture. After months of warnings, the U.S. Government has implemented a broad array of tariff increases, with fresh duties hitting copper-based products, semiconductors, and imports from many nations. On the positive side, tentative trade agreements with Europe, China, Japan, and other nations are providing at least some clarity and counterbalance.
How Good Design Enables Sustainable PCBs
08/21/2025 | Gerry Partida, Summit InterconnectSustainability has become a key focus for PCB companies seeking to reduce waste, conserve energy, and optimize resources. While many discussions on sustainability center around materials or energy-efficient processes, PCB design is an often overlooked factor that lies at the heart of manufacturing. Good design practices, especially those based on established IPC standards, play a central role in enabling sustainable PCB production. By ensuring designs are manufacturable and reliable, engineers can significantly reduce the environmental impact of their products.
50% Copper Tariffs, 100% Chip Uncertainty, and a Truce
08/19/2025 | Andy Shaughnessy, I-Connect007If you’re like me, tariffs were not on your radar screen until a few months ago, but now political rhetoric has turned to presidential action. Tariffs are front-page news with major developments coming directly from the Oval Office. These are not typical times. President Donald Trump campaigned on tariff reform, and he’s now busy revamping America’s tariff policy.
Global PCB Connections: Understanding the General Fabrication Process—A Designer’s Hidden Advantage
08/14/2025 | Markus Voeltz -- Column: Global PCB ConnectionsDesigners don’t need to become fabricators, but understanding the basics of PCB fabrication can save you time, money, and frustration. The more you understand what’s happening on the shop floor, the better you’ll be able to prevent downstream issues. As you move into more advanced designs like HDI, flex circuits, stacked vias, and embedded components, this foundational knowledge becomes even more critical. Remember: the fabricator is your partner.