-
- News
- Books
Featured Books
- pcb007 Magazine
Latest Issues
Current IssueThe Hole Truth: Via Integrity in an HDI World
From the drilled hole to registration across multiple sequential lamination cycles, to the quality of your copper plating, via reliability in an HDI world is becoming an ever-greater challenge. This month we look at “The Hole Truth,” from creating the “perfect” via to how you can assure via quality and reliability, the first time, every time.
In Pursuit of Perfection: Defect Reduction
For bare PCB board fabrication, defect reduction is a critical aspect of a company's bottom line profitability. In this issue, we examine how imaging, etching, and plating processes can provide information and insight into reducing defects and increasing yields.
Voices of the Industry
We take the pulse of the PCB industry by sharing insights from leading fabricators and suppliers in this month's issue. We've gathered their thoughts on the new U.S. administration, spending, the war in Ukraine, and their most pressing needs. It’s an eye-opening and enlightening look behind the curtain.
- Articles
- Columns
- Links
- Media kit
||| MENU - pcb007 Magazine
Elga Europe Reality and Ultra-High-Resolution Photoresist
April 24, 2018 | Patty Goldman, I-Connect007Estimated reading time: 4 minutes
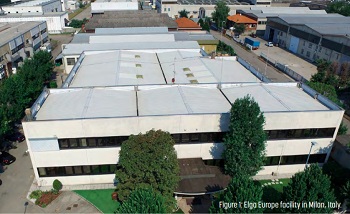
While walking around the PCB hall at productronica, I was approached by my good friend Gene Weiner. Gene emphatically directed me to the Elga booth to find out about their new extra-thick dry film that can image extremely fine features with a perfectly perpendicular sidewall. Elga Europe CEO Giorgio Favini filled me in on the details.
Patty Goldman: Giorgio, I understand you have a new photoresist that is pretty amazing, but why don’t we start with a little bit about you and your company.
Giorgio Favini: Elga Europe was founded as Elga in 1973. At that time the company was very small with only one employee and a share capital value of €250. In 1979, an important joint venture with Lea Ronal began and the name changed to Elga Ronal. In 1989, the company started to import the dry film master rolls from Tokyo Ohka Kogyo, located in Japan, to supply the Italian market, with much success. Thanks to this success, in 1995 Elga Ronal made an important joint venture with TOK and built the actual dry film coating facility close to Milan. In 1999, Elga Ronal bought back the shares of Lea Ronal, changing the name to Elga Europe.
In 2003, for strategic reasons, Elga started its own independent R&D on dry film, and in 2010 my family decided to buy back the shares of TOK and then owned the company at 100%. In 2013, we began the first joint venture with Eternal, the largest worldwide dry film producer, based in Taiwan. This merger was completed in 2017 and Elga became part of the Eternal Chemical group.
This year I became CEO of Elga Europe and second shareholder of the company after Eternal. Today Elga is the market leader in Europe for dry film with a market share greater than 70%; we are also selling ultrapure chemicals for semiconductors, chemicals for the PCB industry, as well as solder mask and copper foil.
At this moment Elga is following many different projects with European PCB producers and one of them we recently did was with one of our German customers, to develop the first radar boards in the automotive industry. We were very successful with them and for this reason, we are involved in practically all the European production of radar boards at this time.
Together we developed a new dry film dedicated to the mass production of radar boards. Elga also recently developed some other dry films which are dedicated to very high technological production. One of these is ultra-fine line dry film, which is the FP400 and FP700.
It is a dry film with a very particular characteristic, which is that it allows the producer to use a dry film of double the thickness of the line width that you want to obtain, which is a 1:2 aspect ratio—and in some cases our customers have achieved 1:4. We developed a dry film with this characteristic because during PCB production, theoretically, the thickness of the dry film used is equal to the line size we want to produce—but with very thin dry films the dust presence in the cleanroom becomes critical with a consequent increase in scrap rate.
The lowest thickness we produce for these dry films lines is 15 microns, with a theoretical resolution of the lines below five microns. Another recent and important project of Elga’s is developing a very thick dry film for some special production applications. We were successful with the production of 130-micron dry film and at this moment Elga Europe is the only company able to supply this dry film thickness to customers which is also for DDI/LDI exposure technology.
Goldman: Is the dry film that thick so they can plate thicker lines and features? Is that the idea?
Favini: Honestly speaking, I don’t know, because the project just started with them, but I suppose it’s dedicated for high copper thickness deposition.
Goldman: How are things in the European economy?
Favini: After 10 years of a difficult European ecomonic situation we are realizing an increase and improvement. This is very important for us, of course, because you know very well what happened in 2008–2009 when it was a complete disaster. But right now, all our customers are at capacity with their production.
Some of them for the first time in their history are refusing orders and many are close to 1.8 as a book-to-bill ratio. So it is very, very positive. The problem is that everybody is a little bit afraid to invest again in Europe after what happened 10 years ago, but I think that if this situation goes on in this way for a medium/long period, new investment will be done in Europe with the opening of new PCB facilities.
Goldman: Along with the expansion of existing companies.
Favini: Yes. Some of our customers also started to use Elga dry film in their facilities located outside Europe, mainly in Asia, to be able to meet the high European order requests. This is very important for us because it’s a big chance to export our dry films to Asia where we can produce locally thanks to the fact that Elga recently became part of Eternal Group.
Regarding the European market, right now we are leader with a market share of 71%, and the forecast for next year is 76%. We are also very strong in Russia with a market share of 62% thanks to excellent cooperation with our local distribution, Petrocommerz. Other very important markets for Elga are Israel and the U.K. where we practically have control of 100% of the market.
Editor's Note: This article originally appeared in the March 2018 issue of PCB007 Magazine, click here.
Suggested Items
SHENMAO Strengthens Semiconductor Capabilities with Acquisition of PMTC
07/10/2025 | SHENMAOSHENMAO America, Inc. has announced the acquisition of Profound Material Technology Co., Ltd. (PMTC), a premier Taiwan-based manufacturer of high-performance solder balls for semiconductor packaging.
KYZEN to Highlight Understencil and PCB Cleaners at SMTA Querétaro Expo and Tech Forum
07/09/2025 | KYZEN'KYZEN, the global leader in innovative environmentally responsible cleaning chemistries, will exhibit at the SMTA Querétaro Expo & Tech Forum, scheduled to take place Thursday, July 24, at Centro de Congresos y Teatro Metropolitano de Querétaro.
Driving Innovation: Direct Imaging vs. Conventional Exposure
07/01/2025 | Simon Khesin -- Column: Driving InnovationMy first camera used Kodak film. I even experimented with developing photos in the bathroom, though I usually dropped the film off at a Kodak center and received the prints two weeks later, only to discover that some images were out of focus or poorly framed. Today, every smartphone contains a high-quality camera capable of producing stunning images instantly.
Hands-On Demos Now Available for Apollo Seiko’s EF and AF Selective Soldering Lines
06/30/2025 | Apollo SeikoApollo Seiko, a leading innovator in soldering technology, is excited to spotlight its expanded lineup of EF and AF Series Selective Soldering Systems, now available for live demonstrations in its newly dedicated demo room.
Indium Corporation Expert to Present on Automotive and Industrial Solder Bonding Solutions at Global Electronics Association Workshop
06/26/2025 | IndiumIndium Corporation Principal Engineer, Advanced Materials, Andy Mackie, Ph.D., MSc, will deliver a technical presentation on innovative solder bonding solutions for automotive and industrial applications at the Global Electronics A