-
- News
- Books
Featured Books
- pcb007 Magazine
Latest Issues
Current IssueInventing the Future with SEL
Two years after launching its state-of-the-art PCB facility, SEL shares lessons in vision, execution, and innovation, plus insights from industry icons and technology leaders shaping the future of PCB fabrication.
Sales: From Pitch to PO
From the first cold call to finally receiving that first purchase order, the July PCB007 Magazine breaks down some critical parts of the sales stack. To up your sales game, read on!
The Hole Truth: Via Integrity in an HDI World
From the drilled hole to registration across multiple sequential lamination cycles, to the quality of your copper plating, via reliability in an HDI world is becoming an ever-greater challenge. This month we look at “The Hole Truth,” from creating the “perfect” via to how you can assure via quality and reliability, the first time, every time.
- Articles
- Columns
- Links
- Media kit
||| MENU - pcb007 Magazine
Substrates for Advanced PCB Technologies: What Will the Future Hold?
November 6, 2018 | Pete Starkey, I-Connect007Estimated reading time: 9 minutes
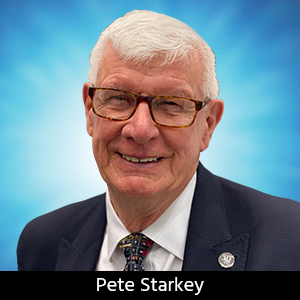
The UK chapter of the global IMAPS community of electronics and microelectronic packaging engineers shared a wealth of knowledge and wisdom about PCB substrate technology trends, developments, and future requirements in a webinar on the first of November. The webinar was introduced on behalf of IMAPS-UK by National Physical Laboratory’s electronics interconnection expert Martin Wickham and featured presentations by Piers Tremlett and Jim Francey.
“Who knows which future substrate will be successful?” Aware of a need to exercise caution when attempting predictions, Piers Tremlett, engineering specialist at Microsemi, quoted an example from ancient Greece: “The Oracle at Delphi knew how to error-proof her future predictions. Everyone else gets it wrong; it’s just a question of by how much.” Nevertheless, his presentation painted a very clear picture of the future for printed circuit substrates, even exploring the possibilities for “substrateless” circuits.
Driven by a need to satisfy the desires of users, substrate technology aimed to improve performance and eliminate waste whilst minimising cost. Tremlett discussed the fluidity of future circuit structures, the potential growth of flexible substrates, the rise in substrates for handling power and heat, and trends from two-dimensional to three-dimensional circuit assemblies. He focused on four relevant topics: miniaturisation for mobile products, heat and power, printed electronics, and substrateless circuits.
Mobile products, especially smartphones, and the cost savings of using less material were the primary drivers for miniaturisation. As an example, Tremlett showed a cross-section of an iPhone 7 with a coreless 10-layer 500-micron substrate and sub-20-micron tracks densely populated with components and a lot of interconnect in a very small space. The interconnect was realised by semi-additive processing, pattern plating on a very thin base copper, and flash etching. As laser direct imaging capability improved and track widths trended towards 10 microns, it was preferred to embed them into the substrate surface to improve reliability, as demonstrated by the Daisho Denshi ultra-narrow pitch flush pad interposer. In his iPhone 7 example, the memory chip was mounted on a very thin three-layer PCB, underneath which was the processor chip with no substrate as such—all the tracks were laid on the packaging material itself and had produced significant performance improvements. He commented that fan-out wafer-level packaging was moving from silicon wafer technology to PCB technology with more than one component inside the mould compound, which could be seen as a paradigm shift away from FR-4 and surface mount.
Conventional assembly technology was giving way to embedded die technology and ultra-thin chip technology, leading to smaller and thinner devices. But whereas the trend had always been to push components off the PCB and on to the silicon, this was now becoming a more expensive option, and the components were being pushed back up into the packaging fab to continue the drive towards integration. Packaging was moving towards complete subsystems, placing more emphasis on substrate capability in terms of layer count and track width and presenting considerable competition to conventional PCB concepts.
Tremlett turned his attention to thermal management, increasing heat being generated by faster processors, RF chips, power chips and LEDs. It was becoming less practicable to use ceramic substrates except for special applications because of considerations of cost, small panel geometries, and high-temperature processing. So, could organic substrates be used as alternatives? He discussed thermal via designs, several forms of integrated metal substrates, metal inserts, and even water-cooled PCBs, and compared their efficiencies as a means of heat dissipation. He reviewed innovations in chip embedding for power packaging that had proven benefits for low- and high-power analogue and digital and RF products and described proprietary embedding package solutions such as SESUB and aEASI. The EmPower project was an international consortium developing embedded power semiconductors for the drive electronics in electric vehicle applications in a module that enabled heat removal on both sides over the shortest possible heat conduction paths.
Page 1 of 3
Testimonial
"The I-Connect007 team is outstanding—kind, responsive, and a true marketing partner. Their design team created fresh, eye-catching ads, and their editorial support polished our content to let our brand shine. Thank you all! "
Sweeney Ng - CEE PCBSuggested Items
How Good Design Enables Sustainable PCBs
08/21/2025 | Gerry Partida, Summit InterconnectSustainability has become a key focus for PCB companies seeking to reduce waste, conserve energy, and optimize resources. While many discussions on sustainability center around materials or energy-efficient processes, PCB design is an often overlooked factor that lies at the heart of manufacturing. Good design practices, especially those based on established IPC standards, play a central role in enabling sustainable PCB production. By ensuring designs are manufacturable and reliable, engineers can significantly reduce the environmental impact of their products.
50% Copper Tariffs, 100% Chip Uncertainty, and a Truce
08/19/2025 | Andy Shaughnessy, I-Connect007If you’re like me, tariffs were not on your radar screen until a few months ago, but now political rhetoric has turned to presidential action. Tariffs are front-page news with major developments coming directly from the Oval Office. These are not typical times. President Donald Trump campaigned on tariff reform, and he’s now busy revamping America’s tariff policy.
Global PCB Connections: Understanding the General Fabrication Process—A Designer’s Hidden Advantage
08/14/2025 | Markus Voeltz -- Column: Global PCB ConnectionsDesigners don’t need to become fabricators, but understanding the basics of PCB fabrication can save you time, money, and frustration. The more you understand what’s happening on the shop floor, the better you’ll be able to prevent downstream issues. As you move into more advanced designs like HDI, flex circuits, stacked vias, and embedded components, this foundational knowledge becomes even more critical. Remember: the fabricator is your partner.
MKS’ Atotech to Participate in IPCA Electronics Expo 2025
08/11/2025 | AtotechMKS Inc., a global provider of enabling technologies that transform our world, announced that its strategic brands ESI® (laser systems) and Atotech® (process chemicals, equipment, software, and services) will showcase their latest range of leading manufacturing solutions for printed circuit board (PCB) and package substrate manufacturing at the upcoming 17th IPCA Show to be held at Pragati Maidan, New Delhi from August 21-23, 2025.
MKS Showcases Next-generation PCB Manufacturing Solutions at the Thailand Electronics Circuit Asia 2025
08/06/2025 | MKS Instruments, Inc.MKS Inc, a global provider of enabling technologies that transform our world, today announced its participation in Thailand Electronics Circuit Asia 2025 (THECA 2025), taking place August 20–22 at BITEC in Bangkok.