-
- News
- Books
Featured Books
- smt007 Magazine
Latest Issues
Current IssueSupply Chain Strategies
A successful brand is built on strong customer relationships—anchored by a well-orchestrated supply chain at its core. This month, we look at how managing your supply chain directly influences customer perception.
What's Your Sweet Spot?
Are you in a niche that’s growing or shrinking? Is it time to reassess and refocus? We spotlight companies thriving by redefining or reinforcing their niche. What are their insights?
Moving Forward With Confidence
In this issue, we focus on sales and quoting, workforce training, new IPC leadership in the U.S. and Canada, the effects of tariffs, CFX standards, and much more—all designed to provide perspective as you move through the cloud bank of today's shifting economic market.
- Articles
- Columns
- Links
- Media kit
||| MENU - smt007 Magazine
Surface Treatment Enabling Low-Temperature Soldering to Aluminum
July 15, 2019 | Divyakant Kadiwala, Averatek CorporationEstimated reading time: 4 minutes
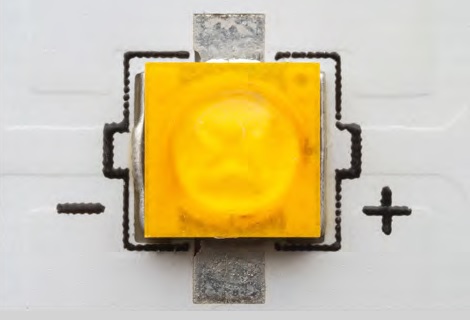
Abstract
The majority of flexible circuits are made by patterning copper metal that is laminated to a flexible substrate, which is usually polyimide film of varying thicknesses. An increasingly popular method to meet the need for lower cost circuitry is the use of aluminium on polyester (Al-PET) substrates. This material is gaining popularity and has found wide use in RFID tags, low-cost LED lighting, and other single-layer circuits. However, both aluminium and PET have their own constraints and require special processing to make finished circuits. Aluminum is not easy to solder components to at low temperatures, and PET cannot withstand high temperatures. Soldering to these materials requires either an additional surface treatment or the use of conductive epoxy to attach components. Surface treatment of aluminum includes the likes of electroless nickel immersion gold plating (ENIG), which is extensive wet chemistry and cost-prohibitive for mass adoption.
Conductive adhesives, including anisotropic conductive paste (ACP), are another alternative to soldering components. These result in component-substrate interfaces that are inferior to conventional solders in terms of performance and reliability. An advanced surface treatment technology will be presented that addresses all these constraints. Once applied on aluminum surfaces using conventional printing techniques such as screen, stencil, etc., it is thermally cured in a convection oven at low temperatures. This surface treatment is non-conductive. To attach a component, a solder bump on the component or solder printed on the treated pad is needed before placing the component. The aluminum circuit will pass through a reflow oven, as is commonly done in PCB assembly. This allows for the formation of a true metal-to-metal bond between the solder and the aluminum on the pads. This process paves the way for large-scale, low-cost manufacturing of Al-PET circuits.
Introduction
Aluminum is the most abundant metal in the earth’s crust. Its alloys have found wide use as a building material in the construction of automobiles, aircraft, bicycles, building frames, etc. Other uses range from electrical connectors, packaging cans and foils, and household utensils. While it is a material of choice in the above fields, it is second to copper in the field of flexible circuits.
This is despite the various advantages that aluminum has over copper. Aluminum is more than three times lighter than copper. The density of aluminum is 2.7 gm/cm3 while that of copper is 8.92 gm/cm3. Its electrical resistivity is 26.5 nΩ·m (at 20°C) while that of copper is 16.78 nΩ·m (at 20°C). Also, its thermal conductivity is 237 W/(m·K) while that of copper is 401 W/(m·K).
Although it is not as good an electrical and thermal conductor as copper, it can radiate heat better than copper due to its lower density. Overall, aluminum has 68% of the conductivity of copper but has only 30% of the weight of copper. This means that a bare wire of aluminum weighs half as much as a bare wire of copper that has the same electrical resistance. This will be similar for aluminium traces in the case of flexible circuits.
Also, aluminum is generally less expensive when compared to copper conductors. A recent check indicated the price of aluminium was 35% less than that of copper. It is three times less expensive than copper on an equal weight basis and six times less expensive on an actual usage basis. This is the biggest advantage that aluminum has over copper. Table 1 lists the comparative properties of the two metals relevant to flexible circuits.
Flexible Circuits and Al-PET Substrates
The majority of flexible circuits are made using copper on polyimide (Cu-PI) substrates. These consist of copper foil laminated onto polyimide film. Varying the thickness of copper and polyimide gives rise to various combinations of thicknesses of Cu-PI to suit the conductivity and dielectric requirements of the end applications. Traces are formed using photolithography followed by a print-and-etch process. Components are soldered on to make the finished circuits. A reasonable selection of solders is available that can easily bond to copper traces without the need for any special surface treatment.
Table 1: Properties of aluminum and copper.
An increasingly popular method to make flexible circuits is by using aluminum on PET (polyethylene terephthalate) or Al-PET substrates. These are available in varying thickness of aluminum foil laminated onto PET film (Figure 1).
While aluminum is less expensive than copper, PET is also significantly cheaper than polyimide film. Hence, lower material cost is a major driver for the increasing use of Al- PET substrates, but their use has been limited because of processing challenges.
Figure 1: Typical laminated construction of Al-PET substrates.
The process to generate the traces on aluminium substrates is similar to that of copper. A dry-film or liquid resist is used for photolithography, which is then followed by chemical print-and-etch to form aluminum traces. But attaching the components onto aluminium is a challenge. Unlike copper, it is not easy to solder to aluminum. Soldering to aluminum is difficult because of the presence of a thin layer of aluminum oxide. This layer forms naturally when the bare metal is exposed to air. Since most flexible circuit manufacturing is done under atmospheric conditions, all aluminum surfaces will have an oxide layer. While the formation of this natural oxide is self-limiting, its presence cannot be overcome by the flux used in existing solder pastes. If harsher fluxes are used within solder pastes to address the aluminum oxide problem, they will cause corrosion of the very thin aluminum layers and thus reliability problems.
There are two methods currently used to attach components to Al-PET substrates: one is the zincate and plating process while the second is using conductive epoxy.
To read the full article, which appeared in the July 2019 issue of SMT007 Magazine, click here.
Testimonial
"Our marketing partnership with I-Connect007 is already delivering. Just a day after our press release went live, we received a direct inquiry about our updated products!"
Rachael Temple - AlltematedSuggested Items
MS2 Technologies, LLC/P. Kay Focuses on Central America with First Installation in Honduras
08/24/2025 | P. Kay Metal, Inc.This year MS2 Technologies has turned their focused to the growing electronics market in Central America. With that focus came the adaptation of MS2 and the Akila System from a Honduras-based corporation with manufacturing plants in both Honduras and Mexico.
BEST Inc. Provides High-Reliability BGA Reballing and Component Rework Services
08/22/2025 | BEST Inc.BEST Inc., a leader in electronic component services, is pleased to announce its component rework services are available for all types of area array devices including ball grid array, land grid array and quad flat no-lead SMT packages.
Indium Corporation Promotes Two Leaders in EMEA (Europe, Middle East, and Africa) Markets
08/05/2025 | Indium CorporationWith its commitment to innovation and growth through employee development, Indium Corporation today announced the promotions of Andy Seager to Associate Director, Continental Sales (EMEA), and Karthik Vijay to Senior Technical Manager (EMEA). These advancements reflect their contributions to the company’s continued innovative efforts with customers across Europe, the Middle East, and Africa (EMEA).
MacDermid Alpha Electronics Solutions Unveils Unified Global Website to Deepen Customer, Talent, and Stakeholder Engagement
07/31/2025 | MacDermid Alpha Electronics SolutionsMacDermid Alpha Electronics Solutions, the electronics business of Elements Solutions Inc, today launched macdermidalpha.com - a unified global website built to deepen digital engagement. The launch marks a significant milestone in the business’ ongoing commitment to delivering more meaningful, interactive, and impactful experiences for its customers, talent, and stakeholders worldwide.
KOKI to Showcase Analytical Services and New HF1200 Solder Paste at SMTA Guadalajara 2025
07/31/2025 | KOKIKOKI, a global leader in advanced soldering materials and process optimization services, will exhibit at the SMTA Guadalajara Expo & Tech Forum, taking place September 17 & 18, 2025 at Expo Guadalajara, Salón Jalisco Halls D & E in Guadalajara, Mexico.