-
- News
- Books
Featured Books
- design007 Magazine
Latest Issues
Current IssueShowing Some Constraint
A strong design constraint strategy carefully balances a wide range of electrical and manufacturing trade-offs. This month, we explore the key requirements, common challenges, and best practices behind building an effective constraint strategy.
All About That Route
Most designers favor manual routing, but today's interactive autorouters may be changing designers' minds by allowing users more direct control. In this issue, our expert contributors discuss a variety of manual and autorouting strategies.
Creating the Ideal Data Package
Why is it so difficult to create the ideal data package? Many of these simple errors can be alleviated by paying attention to detail—and knowing what issues to look out for. So, this month, our experts weigh in on the best practices for creating the ideal design data package for your design.
- Articles
- Columns
- Links
- Media kit
||| MENU - design007 Magazine
Leo Lambert on Training the Next Generation of Technologists
September 25, 2019 | Andy Shaughnessy, Design007 MagazineEstimated reading time: 3 minutes
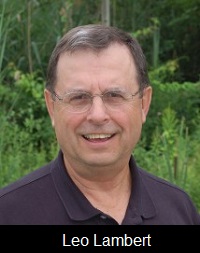
I sat down for an interview with Leo Lambert, VP of technical director for EPTAC Corporation, during the IPC Summer Meetings in Raleigh, North Carolina. We discussed the company’s growth, including plans to have training centers across different regions of the country to help cut down on students’ travel times, and why training methods must constantly evolve to remain effective.
Andy Shaughnessy: Leo, what’s new at EPTAC?
Leo Lambert: We’re very busy. The issue happening now is to get instructors located around the country because it costs us a lot to travel. By having instructors in various parts of the country, we eliminate a lot of travel, so it is a big deal for our customers and us.
Shaughnessy: Because it is a service industry, more or less.
Lambert: Correct. New state government rulings on taxation for services rendered are going to impact us, and we need to be aware of those impact relative to the total cost of the programs. Secondly, from a training perspective, one of the things that happened at the IPC meetings is the new IPC policies and procedures. At EPTAC, we try to follow those to the letter, but there are so many changes that we are questioning the validity of those changes; for example, they are now going to allow people to change the visual PowerPoint presentations. Individuals were not allowed to change them previously as they were all copyrighted; allowing this to happen automatically changes all of the presentations, so the commonality disappears between the same program, which will impact the industry.
So, my function is to make sure the instructors don’t have four different versions for the same specification. Because if they have modified their presentations, we don’t want to hear, “I heard this from instructor A. Now, I have instructor B, but instructor A said this, and instructor B said that.” It becomes a big effort to standardize the presentation and knowledge being disseminated to the students.
Another issue is IPC has a philosophical bent while creating the programs to do three things: “Let me tell you what I’m going to tell you, let me tell you, and then let me tell you what I told you. To present the material in this fashion produces many slides. So, I question the need to have so many repetitive slides. If the instructor goes through every slide, it ends up being a long day, so again, my question is do we really need all that material to certify the individual.?
Shaughnessy: And you’re talking about 200–300 slides.
Lambert: Yes, and if it could be reduced by a larger number of slides, it would eliminate most of the duplications being experienced. Because of this repetitive process, the instructors have to balance the class during the day to compensate for the total time of the presentation. This also involves taking into consideration where the students are coming from, as we get students traveling on Sunday. Therefore, by having students and instructors around the country, we can help save the students’ travel time. The other thing we’re looking at is online training; we’ve done some, but it hasn’t caught on in our industry.
Shaughnessy: What do you see as the value in online learning? I don’t think it will ever replace face-to-face training.
Lambert: There’s definitely some value in online training. Anything picked up and learned is going to add value to the programs. What they, the students, want is to keep the training program interesting by having video snippets in the PowerPoint slides. With the lecture, you could also have a 30-second video to show you how it’s done. We’ve mentioned it to the developers that they need to have physical demonstrations to provide some perspective of the application as it changes the concept of understanding.
To read this entire interview, which appeared in the August 2019 issue of Design007 Magazine, click here.
Suggested Items
TRI to Exhibit at SMTA Queretaro Expo 2025
07/16/2025 | TRITest Research, Inc. (TRI), the leading provider of test and inspection systems for the electronics manufacturing industry, is pleased to announce plans to exhibit at the SMTA Querétaro Expo 2025, scheduled to take place on July 24, 2025, at the Querétaro Centro de Congresos y Teatro Metropolitano.
Global PCB Connections: Let the Spec Fit the Board, Not Just the Brand
07/17/2025 | Jerome Larez -- Column: Global PCB ConnectionsIf you’ve ever seen an excellent PCB quote delayed, or worse, go cold because of a single line on the fab print, you’re not alone. Often, that line reads something like, “Use 370HR only,” or “IT-180A required.” These and other brand-name materials are proven performers, but unless your design needs that specific resin system (say, for RF performance, thermal reliability, or stringent CAF resistance), you may inadvertently be holding your job hostage.
IPC Hall of Fame Spotlight Series: Highlighting Lionel Fullwood
07/15/2025 | Dan Feinberg, I-Connect007Many IPC members who have contributed significantly to IPC and our industry have been awarded the IPC Raymond E. Pritchard Hall of Fame (HOF) Award. Though many early HOF members have passed away and are unknown to today’s IPC membership, their contributions still resonate. This special series on IPC Hall of Fame members provides a reminder of who was honored and why. As a bonus, for those who are still around, we get to find out what these talented individuals are up to today.
TRI Unveils New Platform for Diverse Board Sizes
07/14/2025 | TRITest Research, Inc. (TRI), the leading test and inspection systems provider for the electronics manufacturing industry, proudly introduces a new size configuration for SPI and AOI Models.
Seeing a Future in Mexico
07/09/2025 | Michelle Te, I-Connect007The Global Electronics Association (formerly known as IPC) has been instrumental in fostering a partnership with Guanajuato, a state north of Mexico City with 12 industrial clusters and close to 150 companies involved in electronics. This past spring, Alejandro Hernández, the undersecretary for investment promotion in Guanajuato, attended IPC APEX EXPO 2025 at the invitation of IPC Mexico Director Lorena Villanueva, where he met with several companies to discuss the opportunities available in Mexico. He is inviting electronics-related companies seeking long-term investment in a centrally located area with access to highways, railways, and ports.