-
- News
- Books
Featured Books
- design007 Magazine
Latest Issues
Current IssueAll About That Route
Most designers favor manual routing, but today's interactive autorouters may be changing designers' minds by allowing users more direct control. In this issue, our expert contributors discuss a variety of manual and autorouting strategies.
Creating the Ideal Data Package
Why is it so difficult to create the ideal data package? Many of these simple errors can be alleviated by paying attention to detail—and knowing what issues to look out for. So, this month, our experts weigh in on the best practices for creating the ideal design data package for your design.
Designing Through the Noise
Our experts discuss the constantly evolving world of RF design, including the many tradeoffs, material considerations, and design tips and techniques that designers and design engineers need to know to succeed in this high-frequency realm.
- Articles
- Columns
- Links
- Media kit
||| MENU - design007 Magazine
Stephen Chavez and Happy Holden on Designing Reliable Vias
December 2, 2020 | I-Connect007 Editorial TeamEstimated reading time: 3 minutes
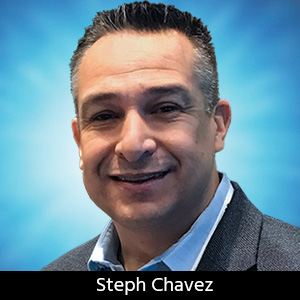
Andy Shaughnessy and Happy Holden speak with Stephen Chavez, a staff engineer with an aerospace company and chairman of the Printed Circuit Engineering Association (PCEA), about designing vias for greater reliability. They also address several areas where they can look to improve reliability, a variety of steps that designers should take to help ensure more robust vias, and some testing and educational resources that PCB designers and design engineers should be aware of.
Andy Shaughnessy: Welcome, gentlemen. Companies keep having problems with vias. Some OEMs will send out a dozen test boards with different-sized vias to a dozen different fabricators, and they’ll come back built a dozen different ways. What can the designers do? What are your thoughts on via design for reliability?
Stephen Chavez: My initial thought on this is that at the earliest stages of the design cycle, communication with your suppliers is an extremely important part of your overall PCB design success. Collaborating with your supplier to lock in your PCB stackup is also a vital step in the early stages of your design. This leads to solidifying your constraints before parts are placed and any traces are routed, which includes the types of via technology that will be implemented in the design. By collaborating with your suppliers and applying industry best practices for PCB design, the odds of achieving a robust, high-reliability DFM design is very good.
As today’s printed circuit engineers strive to meet today’s challenges, there are three competing perspectives for success when designing PCBs: design for layout solvability (DFS); design for performance (DFP), meaning SI/ EMC, power delivery, and thermal; and design for manufacturability (DFM). In the end, the main goal is to get it right the first time. Make Revision 1 work by maximum placement and routing density, optimum electrical performance, and efficient, defect?free manufacturing to achieve high yield and lower cost.
When I talk about meeting today’s challenges when designing multilayer PCBs while keeping in mind the three competing perspectives for success, the via strategy and quality of the via structure is very important. No matter which via technology you utilize in your design—whether it is standard PTH, HDI, microvias, or a combination of the three—you want it designed so that the via is in the board fabricator’s sweet spot while meeting your design requirements and DFM for downstream optimization. If you’re not doing that, you’ll be having a lot of problems. I am still surprised to find there are many people who aren’t talking to their suppliers, and they’re just throwing the design over the fence.
Then, you have to understand the material you’re choosing. Are you choosing the right material for your application and the widget that you’re building? Are you designing in the core sweet spots for success, or are you pushing the rail on complexity? You had better be speaking and understanding the industry terminology and language when talking to your supplier to make sure that you’re on the same page so that there are no surprises at the end.
Happy Holden: If an OEM is naïve enough to send a board out to multiple vendors, they shouldn’t be surprised that they’ll come back different because every fabricator optimizes drilling, desmear, metallization, and plating to be as reliable as they can possibly make it. But because of the multiple vendors, machines, and processes, there are 10,000 different permutations and combinations that make up every multilayer. An OEM deserves whatever they lose if that’s the way they’re going to manage their supply chain. They should develop a qualification process that’s statistically significant, but they won’t, and the fabricators won’t tell them that they’re foolish.
To read this entire interview, which appeared in the November 2020 issue of Design007 Magazine, click here.
Suggested Items
FTG Announces Q2 2025 Financial Results
07/09/2025 | Globe NewswireFiran Technology Group Corporation announced financial results for the second quarter 2025. Revenue: Recorded at $48.7 million, a 25.6% increase over Q2 2024.
Moog Announces Acquisition of COTSWORKS
07/07/2025 | BUSINESS WIREMoog Inc., a worldwide designer, manufacturer and systems integrator of high-performance precision motion and fluid controls and control systems, announced the acquisition of COTSWORKS Inc., an aerospace and defense fiber optics transceiver component manufacturer, for a purchase price of $63 million.
S&K Aerospace Awarded Major Contract Under DLA Maritime Acquisition Advancement Program
07/02/2025 | BUSINESS WIRES&K Aerospace, LLC has been awarded a significant contract under the Defense Logistics Agency’s (DLA) Maritime Acquisition Advancement Program, managed by the U.S. Naval Supply Command - Weapon Systems Support (NAVSUP WSS) in Mechanicsburg, PA.
Green Circuits to Exhibit Full-Service Electronics Manufacturing Solutions at 2025 SMD Symposium
07/02/2025 | Green CircuitsGreen Circuits, a full-service Electronics Manufacturing Services (EMS) partner to leading OEMs, is pleased to announce its participation in the 2025 SMD Symposium, taking place August 5-7 at the Von Braun Center in Huntsville, Alabama.
I-Connect007 Editor’s Choice: Five Must-Reads for the Week
06/27/2025 | Nolan Johnson, I-Connect007While news outside our industry keeps our attention occupied, the big news inside the industry is the rechristening of IPC as the Global Electronics Association. My must-reads begins with Marcy LaRont’s exclusive and informative interview with Dr. John Mitchell, president and CEO of the Global Electronics Association. For designers, have we finally reached the point in time where autorouters will fulfill their potential?