-
- News
- Books
Featured Books
- design007 Magazine
Latest Issues
Current IssueProper Floor Planning
Floor planning decisions can make or break performance, manufacturability, and timelines. This month’s contributors weigh in with their best practices for proper floor planning and specific strategies to get it right.
Showing Some Constraint
A strong design constraint strategy carefully balances a wide range of electrical and manufacturing trade-offs. This month, we explore the key requirements, common challenges, and best practices behind building an effective constraint strategy.
All About That Route
Most designers favor manual routing, but today's interactive autorouters may be changing designers' minds by allowing users more direct control. In this issue, our expert contributors discuss a variety of manual and autorouting strategies.
- Articles
- Columns
- Links
- Media kit
||| MENU - design007 Magazine
HyperLynx: There’s an App for That
August 5, 2022 | I-Connect007 Editorial TeamEstimated reading time: 10 minutes
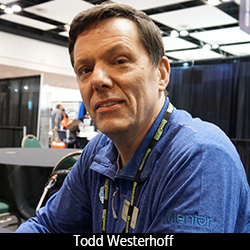
I recently spoke with Todd Westerhoff, product marketing manager for signal integrity software tools at Siemens. We discussed a new capability called HyperLynx Apps that offers a new take on traditional signal and power integrity analysis, and how that fits in with the Siemens plan to put SI and PI tools into the hands of more designers early in the design cycle.
Nolan Johnson: Todd, I understand there’s something new with HyperLynx.
Todd Westerhoff: That’s right. With HyperLynx our focus has always been about making signal and power integrity analysis accessible to a wider audience. Most SI/PI analysis today is performed by experts—people who do that analysis as their primary job. But there just aren’t enough SI/PI experts available to meet demand, and the problem is getting worse. We think it’s time to start looking at the problem differently.
I read a study from Semiconductor Engineering stating that the primary staffing problem electronics companies have is electrical engineers—they just can’t find enough of them, and it’s impacting project schedules. That study was pre-COVID, before the current exodus of experienced talent, and they were referring to general EEs, not SI/PI experts, who are much rarer. We recently searched LinkedIn for jobs relating to signal integrity and found over 2,000 jobs worldwide. Then we ran a more targeted search with just five companies with the acronym AMIGA—Apple, Microsoft, Intel, Google, and Amazon, and only in the United States. That focused search still listed 321 jobs.
That means it’s a great time to be a signal integrity expert, but it’s terrible time to try to hire one. We’ve been talking about the “expert crunch” and how it hasn’t been getting any better for a while now; we think it’s time to think about how we can approach analysis differently. This requires a new vision for how high-speed systems should be designed and verified.
Johnson: Do you all believe the high-speed system design methodology needs to change?
Westerhoff: Yes, because we need to change the way we look at the problem. Let’s take a broad perspective: The classic definition of “high-speed” relates a signal’s edge rate to the electrical delay of the net. It defines the point at which you must pay attention to how you lay out that net. Simply put, if you have to pay attention to how you route it, it’s “high-speed.”
The challenge is that by today’s standards, everything is high speed. Using modern devices and typical board materials, the longest a net can be before it runs into “high-speed” issues is about one-quarter inch, and basically everything is longer than that. That doesn’t necessarily mean designers have to simulate all those nets, but it does mean they need to pay attention to best practice techniques like matching impedance, receiver termination, crosstalk, etc. It’s not just DDR interfaces and serial channels that need to be treated as high-speed signals anymore; it’s every net on every board.
Most people would say, “Then use best practices and follow the manufacturer’s guidelines.” Which is fine as far as it goes, but in every design, there are probably a dozen design tradeoffs that require bending “the rules” and making a judgment call. You can’t follow the rules everywhere; it’s not practical.
But we have a chronic shortage of SI/PI experts, and it’s getting worse. Those experts are already tied up working on the hardest problems on the hardest boards. But if everything is high-speed and hard tradeoffs are common, that means the designers trying to make those tradeoffs are just making a judgment call and hoping for the best, with no analysis to back them up. The question becomes, “Can we provide tools that let a designer run basic (but useful) analyses by themselves, to increase their chance of success without bogging down the SI/PI experts?” That’s how we want to change the design process itself.
We’ve introduced a new capability in our 2.12 release called HyperLynx Apps. These are single-purpose tools that perform one analysis function, simply and automatically. They’re tools that a designer can use to compare design tradeoffs and decide which implementation is better, without requiring help from an SI/PI expert.
There are two types of HyperLynx apps. The first is a design app, which is meant to be run by a PCB designer or a hardware designer trying to make a layout decision. These apps run while you wait. You load the design, set the parameters, hit “run,” wait a few seconds, and a report pops up. Design apps are qualitative: You run the simulation with parameters that are representative of the design technology, but not device-specific. You’re not trying to qualify the design for fab-out; you’re trying to verify that the layout performs reasonably, and test changes to the layout to see if they make the design’s performance better or worse.
The second type of HyperLynx app is a regression app, which performs a complete post-route verification of a set of signals, including layout extraction, EM modeling, analysis, and post-processing. A regression app produces a report that compares the design’s behavior against an applicable standard, showing which signals passed, which signals failed, and by how much. We call them regression apps because they can be run overnight while PCB layout is still in progress, instead of waiting until layout is complete. We’re all understand software regression testing: test gets run automatically during software development to determine which functions work. We see regression apps as that same concept applied to standards-based PCB design. If I’m designing a PCIe-5 channel, the electrical requirements for that channel to be considered compliant with the spec are well-established, so why not verify the serial channels in a layout on a regular basis during layout to ensure the design remains on-track?
Both design and regression apps can be run by PCB and hardware designers, so they can discover and resolve problems much sooner than if they had to wait for an SI expert to run analysis for them. Typically, SI/PI analysis is only run once layout is complete—when it’s harder to make design changes. If problems can be discovered and corrected earlier in the design cycle, everybody wins: designers spend less time waiting for SI/PI experts, SI/PI experts spend less time solving basic problems for others, and the PCB gets to market sooner with better quality.
Johnson: Are HyperLynx Apps running inside the normal layout environment?
Westerhoff: We’re leveraging the integrations that already exist between multiple PCB tools and HyperLynx. Customers are already using HyperLynx with all the mainstream PCB layout tools, so it made sense to start with that.
Johnson: So, you’re plugged into the different PCB design flows to access the PCB database, but this is running as a standalone application? Which CAD tool is being used doesn’t matter?
Westerhoff: Correct. The apps run as a standalone application with their own GUI. The GUI itself is minimal, so the workflow is essentially: load the database, verify options, and press run.
Johnson: Can you give examples of what you called design apps?
Westerhoff: Good examples of a design app would be DC drop, loop inductance, and pulse response. Design apps are used to interactively analyze specific sections of a design for specific behaviors.
Page 1 of 2
Testimonial
"Our marketing partnership with I-Connect007 is already delivering. Just a day after our press release went live, we received a direct inquiry about our updated products!"
Rachael Temple - AlltematedSuggested Items
American Standard to Participate in European Microwave Week 2025
09/05/2025 | American Standard CircuitsAnaya Vardya, President, and CEO of American Standard Sunstone Circuits has announced that his company will once again be taking part in European Microwave Week, Europe’s premier RF, microwave, radar and wireless event, to be held from September 21-26, 2025 at Jaarbeurs in Utrecht, The Netherlands.
Kris Moyer Discusses His Emerging Design Technologies Class
09/04/2025 | Marcy LaRont, I-Connect007Kris Moyer, a design instructor for the Global Electronics Association, will be teaching his advanced PCB design class this fall. If you’re ready to level up your design education, you won’t want to miss this interview. The PCB Design for Emerging Design Technologies course is designed to provide the skills necessary to create PCB/PBA designs that require cutting-edge emerging design technologies and comply with all necessary IPC standards, including new standards being developed in this area.
Synopsys Announces Expanding AI Capabilities for its Leading EDA Solutions
09/04/2025 | SynopsysSynopsys announced expanding Synopsys.ai™ Copilot generative AI (GenAI) capabilities for its industry-leading semiconductor design solutions, enabling semiconductor engineering teams to accelerate development timelines, support significantly more complex designs, and increase engineering velocity amidst a workforce shortage.
UHDI Fundamentals: UHDI Technology and Industry 4.0
09/03/2025 | Anaya Vardya, American Standard CircuitsUltra high density interconnect (UHDI) technology is rapidly transforming how smart systems are designed and deployed in the context of Industry 4.0. With its capacity to support highly miniaturized, high-performance, and densely packed electronics, UHDI is a critical enabler of the smart, connected, and automated industrial future. Here, I’ll explore the synergy between UHDI and Industry 4.0 technologies, highlighting applications, benefits, and future directions.
Talking with Tamara: Floor Planning Policies
09/04/2025 | Andy Shaughnessy, Design007 MagazineTamara Jovanovic is an electrical engineer with Masimo, a medical equipment manufacturer. She’s been designing PCBs for seven years and earned a master’s degree in electrical engineering in 2022. I asked Tamara to share her thoughts on floor planning—the challenges, techniques, and advice for designers setting up floor planning strategies.