-
- News
- Books
Featured Books
- design007 Magazine
Latest Issues
Current IssueAll About That Route
Most designers favor manual routing, but today's interactive autorouters may be changing designers' minds by allowing users more direct control. In this issue, our expert contributors discuss a variety of manual and autorouting strategies.
Creating the Ideal Data Package
Why is it so difficult to create the ideal data package? Many of these simple errors can be alleviated by paying attention to detail—and knowing what issues to look out for. So, this month, our experts weigh in on the best practices for creating the ideal design data package for your design.
Designing Through the Noise
Our experts discuss the constantly evolving world of RF design, including the many tradeoffs, material considerations, and design tips and techniques that designers and design engineers need to know to succeed in this high-frequency realm.
- Articles
- Columns
- Links
- Media kit
||| MENU - design007 Magazine
Designing for Material Conservation Means Changing Attitudes
August 29, 2022 | I-Connect007 Editorial TeamEstimated reading time: 4 minutes
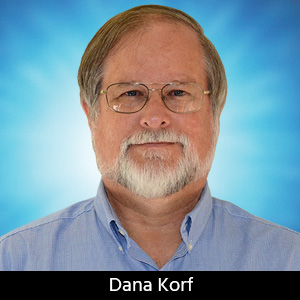
It makes a lot of sense: During times when the supply chain is stretched to the breaking point—and the last few years certainly qualify—what if PCB designers created boards that used fewer components and less laminate? Do PCBs still have to be 0.062" thick? Why not reduce layer count while they’re at it?
Andy Shaughnessy and Nolan Johnson spoke with I-Connect007 columnist Dana Korf about the idea of designing a PCB with material conservation in mind. Is it a great new idea, or are we opening a whole new can of worms and a separate group of problems?
Andy Shaughnessy: Dana, our August design issue focuses on material conservation, which has become a topic of conversation during the supply chain snafu. It seems simple—let’s just use fewer components and less laminate, right? What are your thoughts on that? You were working at this huge volume level in China, where saving a few ounces of copper or a few components here and there could mean millions of dollars. Was conserving materials something on your radar screen?
Dana Korf: Actually, I just saw an interesting email this morning that included Happy Holden on that subject. The one comment that struck me was someone saying that boards don’t have to be 0.062" thick anymore; that was set in the 1950s. Can we make thinner boards? Use thinner materials? Consume less of everything? That’s a very interesting comment. But they’re right; we’re stuck on a 1950s architecture, basically. And in a regular FR-4 board, traditionally the material cost is about 16-20% of the total cost.
With high-performance boards, it could be 80% of the board cost. People drive to use lower-end materials because as performance goes up, that ratio goes up. Could we use thinner materials and consume less? That’s one of the big advantages of 3D printing for circuit boards—we don’t waste anything. You don’t rout out a panel. You don’t use layers. You print your trace of any X, Y, Z fashion you want, so you don’t need to drill holes and you don’t consume drill bits, copper plating chemistries, etc. That very topic is one nice advantage about the 3D world; it’s one of the side advantages.
Do I see a lot of people thinking that way? No, but as someone pointed out in our email thread, on the average, our typical board is four or six layers, and 0.062" thick. Why can’t we make it 0.050"? Why not? We would save material. That’s very interesting. The industry needs to change the way we think.
Shaughnessy: As Happy was saying, if you start making the board itself thinner, you may run up against ultra HDI problems, as well as changing things like impedance, too. You’d have pros and cons.
Korf: Yes. In a traditional board shop, you’re trying to use the entire sheet size that the laminator makes, so they don’t throw away or have to recycle anything. Then you get to the panel, and you try to use everything because you pay for the entire panel whether you receive it or not. That work has been going on for a long time just to help reduce costs related to throwing material away. As I like to say, “Minimizing that effect to save money.” A lot of it is already recycled anyway.
I haven’t been in any meetings with designers who say, “I’m trying to use fewer materials to save the environment.” I’ve really never heard those words. Maybe in the back of their head they’re thinking that, but not in the forefront.
Nolan Johnson: It makes an interesting spin.
Korf: Yes. It’s a good, new way of thinking if you’re trying to lead the industry a little bit. It would be great to get people thinking about it more.
Johnson: This is yet another place to shave your margins, be more efficient, make more money, and release capacity to the whole industry.
Korf: From a cost standpoint? Absolutely, it’s true. You must go to the next level of expensive technology for the line width and space and/or interconnects, vias. It could be very true. I had a design one time, and the customer had one blind via, one laser via, on the whole board. I said, “We can make that a through-hole and save you 20%.” He says, “No, I need it.” I said, “Okay, it’s your money. We’ll make it for you.” Conservation is an interesting topic. How can we save money by using less material, changing the way we do layers and stackups?
Realistically, material conservation isn’t something that I’ve heard come up much at all; it’s usually more talk about performance and which technology you should use.
To read this entire conversation, which appeared in the August issue of Design007, click here.
Suggested Items
The Evolution of Picosecond Laser Drilling
06/19/2025 | Marcy LaRont, PCB007 MagazineIs it hard to imagine a single laser pulse reduced not only from nanoseconds to picoseconds in its pulse duration, but even to femtoseconds? Well, buckle up because it seems we are there. In this interview, Dr. Stefan Rung, technical director of laser machines at Schmoll Maschinen GmbH, traces the technology trajectory of the laser drill from the CO2 laser to cutting-edge picosecond and hybrid laser drilling systems, highlighting the benefits and limitations of each method, and demonstrating how laser innovations are shaping the future of PCB fabrication.
Day 2: More Cutting-edge Insights at the EIPC Summer Conference
06/18/2025 | Pete Starkey, I-Connect007The European Institute for the PCB Community (EIPC) summer conference took place this year in Edinburgh, Scotland, June 3-4. This is the third of three articles on the conference. The other two cover Day 1’s sessions and the opening keynote speech. Below is a recap of the second day’s sessions.
Day 1: Cutting Edge Insights at the EIPC Summer Conference
06/17/2025 | Pete Starkey, I-Connect007The European Institute for the PCB Community (EIPC) Summer Conference took place this year in Edinburgh, Scotland, June 3-4. This is the second of three articles on the conference. The other two cover the keynote speeches and Day 2 of the technical conference. Below is a recap of the first day’s sessions.
Preventing Surface Prep Defects and Ensuring Reliability
06/10/2025 | Marcy LaRont, PCB007 MagazineIn printed circuit board (PCB) fabrication, surface preparation is a critical process that ensures strong adhesion, reliable plating, and long-term product performance. Without proper surface treatment, manufacturers may encounter defects such as delamination, poor solder mask adhesion, and plating failures. This article examines key surface preparation techniques, common defects resulting from improper processes, and real-world case studies that illustrate best practices.
RF PCB Design Tips and Tricks
05/08/2025 | Cherie Litson, EPTAC MIT CID/CID+There are many great books, videos, and information online about designing PCBs for RF circuits. A few of my favorite RF sources are Hans Rosenberg, Stephen Chavez, and Rick Hartley, but there are many more. These PCB design engineers have a very good perspective on what it takes to take an RF design from schematic concept to PCB layout.