-
- News
- Books
Featured Books
- smt007 Magazine
Latest Issues
Current IssueSupply Chain Strategies
A successful brand is built on strong customer relationships—anchored by a well-orchestrated supply chain at its core. This month, we look at how managing your supply chain directly influences customer perception.
What's Your Sweet Spot?
Are you in a niche that’s growing or shrinking? Is it time to reassess and refocus? We spotlight companies thriving by redefining or reinforcing their niche. What are their insights?
Moving Forward With Confidence
In this issue, we focus on sales and quoting, workforce training, new IPC leadership in the U.S. and Canada, the effects of tariffs, CFX standards, and much more—all designed to provide perspective as you move through the cloud bank of today's shifting economic market.
- Articles
- Columns
- Links
- Media kit
||| MENU - smt007 Magazine
Estimated reading time: 2 minutes
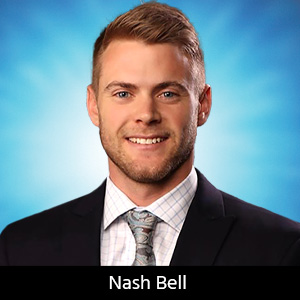
Knocking Down the Bone Pile: Opening a Trace on the Surface of a PCB
Because of PCB layout problems or required circuit modifications, at times a trace on the surface of a PCB needs to be severed. In this procedure a small section of the trace is removed, thereby forming a “break” in the circuit. In general practice, the length of this trace cut is as least as wide as the minimum conductor spacing. In most cases, a very sharp-edged knife or high-speed mill will make the cut. After cutting the area is tested and sealed with epoxy.
To make this cut, the following should be on hand to the intermediate-level PCB rework and repair technician, including but not limited to:
- Isopropyl alcohol for cleaning
- Continuity meter and test probes for measuring electrical continuity
- PCB epoxy
- Oven for curing the epoxy
- Sharp knife for precision cutting of trace
- Stereo microscope with proper lighting for inspection
- Low lint wipes for cleanup
- Colorant matching the PCB mask color
The first step (Figure 1) is to make sure the proper location of the cut can be determined given the physical limitations of the neighboring components to the cut location. Use the mechanical assembly drawings in addition to the Gerber files. Determine where the minimum trace-width cut will take place. Clean the area using the isopropyl and the lint-free cloth. The cut should be perpendicular to the trace edges.
Make the cuts (Figure 2) by using a straight edge and the knife, making the two cuts perpendicular to the trace direction cuts. Apply even pressure using a straight edge as a guide, slowly cutting through the trace so as to not damage other areas of the board. Remove the cut-out trace piece and discard.
An alternative to using the knife would be to clamp the board onto the milling bed making sure the board is parallel to the cutting tool. Size the cutting tool at half the width of the cut to be made. Make sure to protect the cut area so no foreign debris is left on the PCB. Clean after cutting as previously described.
Next use the continuity checker to make sure there is an electrical open between the cuts.
Mix the epoxy per the manufacturers’ recommendations making sure you are aware of the humidity, temperature, and working time of the epoxy. In some cases, colorant needs to be added to color match the assembly. Using the edge of your knife, carefully fill in in the gap (Figure 3) left by the missing trace. Cure the epoxy in an oven per the manufacturer’s guidelines.
As a final step make sure the modification of board repair did not leave behind unintended damage to surrounding circuits while you were concentrating on the repair. Perform any remaining electrical tests as required.
Resource
IPC 7711/7721 Rework and Repair Modification of Printed Boards and Electronic Assemblies, January 2017.
This column originally appeared in the September 2022 issue of SMT007 Magazine.
More Columns from Knocking Down the Bone Pile
Knocking Down the Bone Pile: Addressing End-of-life Component Solderability Issues, Part 4Knocking Down the Bone Pile: Tin Whisker Mitigation in Aerospace Applications, Part 3
Knocking Down the Bone Pile: Gold Mitigation for Class 2 Electronics
Knocking Down the Bone Pile: Basics of Component Lead Tinning
Knocking Down the Bone Pile: Package on Package Rework—Skill Required
Knocking Down the Bone Pile: 2023’s Top Challenges in BGA Rework
Knocking Down the Bone Pile: Eliminating Solder Balls in Hand Soldering
Knocking Down the Bone Pile: Soldering for QFPs and Other Gull Wing Leaded Parts