-
- News
- Books
Featured Books
- design007 Magazine
Latest Issues
Current IssueShowing Some Constraint
A strong design constraint strategy carefully balances a wide range of electrical and manufacturing trade-offs. This month, we explore the key requirements, common challenges, and best practices behind building an effective constraint strategy.
All About That Route
Most designers favor manual routing, but today's interactive autorouters may be changing designers' minds by allowing users more direct control. In this issue, our expert contributors discuss a variety of manual and autorouting strategies.
Creating the Ideal Data Package
Why is it so difficult to create the ideal data package? Many of these simple errors can be alleviated by paying attention to detail—and knowing what issues to look out for. So, this month, our experts weigh in on the best practices for creating the ideal design data package for your design.
- Articles
- Columns
- Links
- Media kit
||| MENU - design007 Magazine
Q&A: The Learning Curve for Ultra HDI
October 20, 2022 | Andy Shaughnessy, Design007 MagazineEstimated reading time: 2 minutes
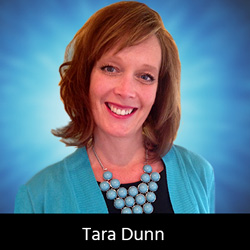
For this issue on ultra HDI, we reached out to Tara Dunn at Averatek with some specific questions about how she defines UDHI, more about the company’s patented semi-additive process, and what really sets ultra HDI apart from everything else. Do designers want to learn a new technology? What about fabricators? We hope this interview answers some of those questions that you may be having about these capabilities and what it could mean for your designs.
Q: How do you define ultra HDI? What is the cutoff in mils or microns?
A: That is an excellent question. At this point I think it means different things to different people depending on where their current HDI capabilities are. IPC has created an ultra HDI working group and I believe the definition they are working with is that to be considered ultra-HDI, a design needs to include one or more of these parameters: Line width below 50 µm, spacing below 50 µm, dielectric thickness below 50 µm, and microvia diameter below 75 µm.
Q: Averatek has developed the A-SAP™ semi-additive process, which can produce traces down into the UHDI space. Can you clear up the differences between mSAP and A-SAP, and what this means to designers and design engineers?
A: In general, SAP, or a semi-additive process, is a process that starts with a very thin layer of copper and then builds the trace patterns from there. One common differentiating factor in these two approaches to SAP is the starting copper thickness. Typically, copper thickness that is 1.5 microns or above would be considered mSAP, or a modified semi-additive process. Because the copper is a little thicker than other SAP processes, it requires more etching, which can have impacts on trace width and space and also the sidewalls of the trace. This process can typically provide features as small as 30 microns in highly specialized facilities that are running extremely high-volume manufacturing. This technology is commonly seen in our smartphones.
Averatek’s A-SAP begins with a much thinner electroless copper, typically 0.2 µm and this copper thickness, or thinness if you will, enables the fabricator to produce much finer feature sizes. The technology is capable of traces and spaces as small as 1 micron if the fabricator has advanced imaging equipment. Typically, PCB fabricators have equipment that can image traces to 12.5 µm today. There are also signal integrity benefits to this process. Because the base copper is so thin, there is minimal impact on the trace sidewalls, and greater control to line width resulting in impedance control tolerance improvements.
One other difference between the mSAP and A-SAP technologies is in the ratio of trace height to trace width; mSAP processes allow a 1:1 ratio of height to width and A-SAP traces can be produced with aspect ratio of 2:1 or greater. For example, a 25 µm wide trace could be 40 µm tall. This has gotten a lot of attention from a signal integrity perspective.
To read this entire article, which appeared in the October 2022 issue of Design007 Magazine, click here.
Suggested Items
Copper Price Surge Raises Alarms for Electronics
07/15/2025 | Global Electronics Association Advocacy and Government Relations TeamThe copper market is experiencing major turbulence in the wake of U.S. President Donald Trump’s announcement of a 50% tariff on imported copper effective Aug. 1. Recent news reports, including from the New York Times, sent U.S. copper futures soaring to record highs, climbing nearly 13% in a single day as manufacturers braced for supply shocks and surging costs.
I-Connect007 Editor’s Choice: Five Must-Reads for the Week
07/11/2025 | Andy Shaughnessy, Design007 MagazineThis week, we have quite a variety of news items and articles for you. News continues to stream out of Washington, D.C., with tariffs rearing their controversial head again. Because these tariffs are targeted at overseas copper manufacturers, this news has a direct effect on our industry.I-Connect007 Editor’s Choice: Five Must-Reads for the Week
Digital Twin Concept in Copper Electroplating Process Performance
07/11/2025 | Aga Franczak, Robrecht Belis, Elsyca N.V.PCB manufacturing involves transforming a design into a physical board while meeting specific requirements. Understanding these design specifications is crucial, as they directly impact the PCB's fabrication process, performance, and yield rate. One key design specification is copper thieving—the addition of “dummy” pads across the surface that are plated along with the features designed on the outer layers. The purpose of the process is to provide a uniform distribution of copper across the outer layers to make the plating current density and plating in the holes more uniform.
Trump Copper Tariffs Spark Concern
07/10/2025 | I-Connect007 Editorial TeamPresident Donald Trump stated on July 8 that he plans to impose a 50% tariff on copper imports, sparking concern in a global industry whose output is critical to electric vehicles, military hardware, semiconductors, and a wide range of consumer goods. According to Yahoo Finance, copper futures climbed over 2% following tariff confirmation.
Happy’s Tech Talk #40: Factors in PTH Reliability—Hole Voids
07/09/2025 | Happy Holden -- Column: Happy’s Tech TalkWhen we consider via reliability, the major contributing factors are typically processing deviations. These can be subtle and not always visible. One particularly insightful column was by Mike Carano, “Causes of Plating Voids, Pre-electroless Copper,” where he outlined some of the possible causes of hole defects for both plated through-hole (PTH) and blind vias.