-
-
News
News Highlights
- Books
Featured Books
- design007 Magazine
Latest Issues
Current IssueAll About That Route
Most designers favor manual routing, but today's interactive autorouters may be changing designers' minds by allowing users more direct control. In this issue, our expert contributors discuss a variety of manual and autorouting strategies.
Creating the Ideal Data Package
Why is it so difficult to create the ideal data package? Many of these simple errors can be alleviated by paying attention to detail—and knowing what issues to look out for. So, this month, our experts weigh in on the best practices for creating the ideal design data package for your design.
Designing Through the Noise
Our experts discuss the constantly evolving world of RF design, including the many tradeoffs, material considerations, and design tips and techniques that designers and design engineers need to know to succeed in this high-frequency realm.
- Articles
- Columns
- Links
- Media kit
||| MENU - design007 Magazine
Estimated reading time: 6 minutes
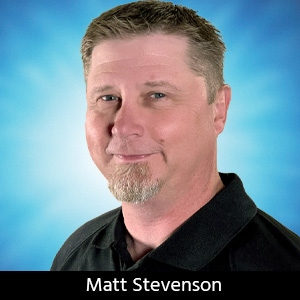
Connect the Dots: Designing for Reality—Solder Mask and Legend
In the previous episode of I-Connect007’s On the Line with… podcast, we discussed the strip, etch, and strip process. At this point, we have a functioning board, but we still need to protect the PCB from environmental effects and document the circuit components. This brings us to the solder mask and legend phase of production.
Before the process begins, we must inspect the boards to ensure that the plating and etching process is effective and the PCB meets customer functionality requirements. We have two inspection methods: visual and automated optical inspection (AOI).
A visual inspection under magnification by an inspector is adequate for simpler designs. Inspectors examine the board components for various issues, such as ragged traces or copper where it does not belong, and reject those that do not pass the test. For more complex boards or where a customer requests higher than Class 2 IPC-A-600 inspection, we use an AOI process that performs a near pixel-to-pixel comparison between the physical board and the original design data.
Pro Tips for a More Effective Board Inspection
Designers can help the inspection process run more smoothly and effectively by providing their manufacturers with clean data files. The size of the files and the memory required can affect the speed and accuracy of the AOI process, so it is important not to overload the design file with unnecessary data.
Roughening the Copper
Once the board has passed inspection, we begin the solder mask process by slightly roughing up the board’s copper. This is to promote adhesion and create a good bond between the copper on the surface and the solder mask.
We use three different methods to rough up the copper, each with distinct advantages and disadvantages. Designers should consider which is best for their designs.
- A mechanical scrub, depending on how aggressively it is performed, can create gouges, troughs, and rivers that impact performance for boards requiring high-speed signals. For most boards, a mechanical scrub will not create issues and is a common, cost-effective method for roughening copper.
- The second method involves running the panels through a slurry of a soft pumice material that can also create pits and gouges. This process does not have as much impact on the trace performance as a mechanical scrub, and it creates great adhesion. This method has a downside for manufacturers because the pumice becomes a hazardous waste that requires extra care upon disposal.
- The last method is an adhesion promoter that chemically roughens the surface. This is the least likely to create performance-impacting abnormalities on the PCBs.
Designers can communicate their method preferences by consulting with their CAM engineer and calling it out with thorough design notes in the design specifications.
Solder Mask Application
There are two common methods for applying solder mask. Most of us think of the classic flood-coating the board with liquid solder mask and removing it in the areas we want to remain solderable. However, additive printing works like an inkjet printer. It is cool, but for this discussion, we will focus on the tried-and-true methodology.
There are a couple of different ways to apply solder mask to panels. Screening of the solder mask involves placing the boards in a tight mesh screen contraption—a rectangle with a wood or metal frame with the mesh stretched across it. We use a squeegee to apply the solder mask by pushing it through the mesh onto the board’s surface with a uniform thickness.
With this process, we coat every square inch of the panel that can contain a circuit board, effectively flood-coating the entire side. To ensure we leave holes where the solder goes, we use a liquid photo-imageable solder mask (LPI) that allows us to transfer the solder mask file onto the board and make the solderable areas visible.
After thermally drying (a fancy way of saying baking) the panel to remove some solvents used, we transfer the image onto the board. We have two methods for doing this: photolithography and laser direct imaging (LDI).
The first method involves creating a film with all the board components such as solderable surfaces, through-holes, pads, and traces blacked out. We then run the boards through a developing process that removes the solder mask everywhere else. LDI achieves the same result by “marking” the LPI that needs to be removed during exposure to the laser and protecting the solderable areas from it.
After running through the chemical development process, we have a board that is the familiar green (or other color of choice) with the pads exposed. At this point, we have applied the solder mask and exposed it, but before we final-cure the panel, we will put the silkscreen (legend) layer on top of it so there is a good bonding adhesion in place. Then, we bake the panel again to remove the remaining solvents. Once it comes out of the oven and cools, the solder mask becomes hard and durable, exposing all the solderable pads.
Solder mask has always been a relatively straightforward element of the manufacturing process, but as designs become tighter, high-speed requirements more frequent, and copper on the layers thicker, solder mask becomes a more critical part of the manufacturing process. In tight pitch areas of the board, designers need to be sure they have enough solder mask web or dam between fine pitch pads.
Most manufacturers can resolve and maintain a 2 to 3-mil wide web between pads. Keeping as much of the spacing between pads to accommodate a smaller dam or web between features is important. If pad spacing leaves something like a 1-mil web, most manufacturers will struggle to produce boards that meet design requirements. Narrow pad spacing can create solder bridging during assembly and shorting defects.
Why Are PCBs Green?
PCB boards can come in more than one color, but these days, they are often green. Green became the standard mostly because of the contrast of color it provides with other components of the board, such as copper traces. It offers the most visibly inspectable color to contrast the PCB’s features.
Over time, manufacturing best practices increasingly aligned with using green solder mask during production, and now it is the predominant color for PCBs. Other colors were and are used for several reasons. Some manufacturers use different-colored boards to differentiate prototypes from production-ready boards, and many designers choose different colors for aesthetic reasons. For high performance, green is the best choice because it is the most well-understood across the industry.
Solder Mask Design Considerations
As with any phase of production, designers should be aware of what can go wrong during solder mask and how to prevent issues before they occur. Thickness can impact the manufacturing process, and so can the type of solder mask. When we get down to an impedance tolerance of plus or minus 5%, every little thing can have an impact, including the thickness and pigmentation of the solder mask. Solder pad shapes, sizes, and locations should allow sufficient room for solder mask webs and dams—considering the swell of the solder mask. Knowing your tolerances and making sure you have design consistency is key to a smooth solder mask process.
We are nearing the end of the manufacturing process and are ready for the surface finish. Keep an eye out for my next article on that subject. If you can’t wait, listen to the Designing for Reality: Surface Finish episode of On the Line with… and to hear our in-depth conversation about solder mask and legend, please listen to episode 10.
Read Matt’s book, The Printed Circuit Designer’s Guide to… Designing for Reality, or listen to his podcast here.
This column originally appeared in the December 2024 issue of Design007 Magazine.
More Columns from Connect the Dots
Connect the Dots: Proactive Controlled ImpedanceConnect the Dots: Involving Manufacturers Earlier Prevents Downstream Issues
Connect the Dots: Stop Killing Your Yield—The Hidden Cost of Design Oversights
Connect the Dots: Designing for Reality—Routing, Final Fab, and QC
Connect the Dots: Designing for Reality—Surface Finish
Connect the Dots: Designing for Reality: Strip-Etch-Strip
Connect the Dots: Designing for Reality—Pattern Plating
Connect the Dots: Designing for Reality—Outer Layer Imaging