-
- News
- Books
Featured Books
- design007 Magazine
Latest Issues
Current IssueShowing Some Constraint
A strong design constraint strategy carefully balances a wide range of electrical and manufacturing trade-offs. This month, we explore the key requirements, common challenges, and best practices behind building an effective constraint strategy.
All About That Route
Most designers favor manual routing, but today's interactive autorouters may be changing designers' minds by allowing users more direct control. In this issue, our expert contributors discuss a variety of manual and autorouting strategies.
Creating the Ideal Data Package
Why is it so difficult to create the ideal data package? Many of these simple errors can be alleviated by paying attention to detail—and knowing what issues to look out for. So, this month, our experts weigh in on the best practices for creating the ideal design data package for your design.
- Articles
- Columns
- Links
- Media kit
||| MENU - design007 Magazine
The Material Witness: Nonwoven Aramid Reinforcement is Back
October 22, 2015 | Chet Guiles, Arlon Electronic MaterialsEstimated reading time: 3 minutes
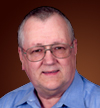
In the 1st century AD, there was significant debate among Jewish theologians as to whether resurrection was possible. PCB designers in the early 21st century have had a similar concern about future availability of 85NT nonwoven aramid laminate and prepreg. The stakes may be somewhat less critical, depending on your theological bent, but the future of a wide variety of programs designed around the properties of (dare I mention the name?) Thermount® have been hanging in the balance. What was Thermount exactly and why was there such a furor when DuPont announced its premature demise? And where do we stand now with the redevelopment of a nonwoven aramid product?
The original 85NT product was based on high tensile-strength para-aramid fiber with a meta-aramid fibrid binder. The para-aramid fibers have a high tensile modulus (fiber modulus of about 19 mpsi) and a negative linear coefficient of thermal expansion with a CTE of about -4 ppm/oC meaning that the material shrank when heated, and the fibrid held the fibers together in a uniform matrix. Produced in a high-end papermaking process, the resulting substrate was a yellow aramid paper material that produced laminates with a unique and useful set of properties. For a polyimide aramid composite the benefits look like this:
- Tg of pure polyimide (250oC)
- Low in-plane (X,Y) expansion of 7-9 ppm/°C
- Excellent dimensional stability and enhanced registration
- Decomposition temperature of 426°C, compared with 300-360°C for typical high-performance epoxies, offering outstanding high-temperature life
- Polymeric reinforcement results in PCBs typically 25% lighter in weight than conventional glass-reinforced laminates
- Laser ablatable for high-speed formation of microvias as small as 25μm in clad laminates as thin as 0.002”
- Electrical and mechanical properties meeting the requirements of IPC-4101/53
- Compatible with lead-free processing
- RoHS/WEEE compliant
The earliest military adoption of aramid reinforced laminates was in the guidance system for the Tomahawk cruise missile, a significant success in terms of test results (thermal cycled better than the prior woven aramid technology) and field performance. The combat-proven Tomahawk gave the then relatively new substrate a kick-start. I still have the jacket patch that the Tomahawk PWB development staff gave me. And there was some real pride in achievement in the ongoing field success of that program.
Later uses of 85NT materials included a wide variety of military and commercial avionics. The first-generation avionics for the Boeing 777 were designed on this platform, and it replaced heavy copper-invar-copper (CIC) in a number of older designs. In addition to these, the Iridium telecommunications satellite constellation used 85NT for a number of its PWBs.
In July of 2006 the imminent demise of the DuPont Thermount product was announced to its customer base. In November 2006, a letter from Ralph Hutton, president of DuPont Teijin Advanced Papers, said, “Due to a dramatic reduction in demand for Thermount reinforcement for consumer applications in Japan, and a corresponding reduction in global demand for the foreseeable future, we are unable to continue accepting orders for Thermount reinforcement of any kind beyond December 31, 2006.”
Working with senior officials at major military and commercial OEMs, Arlon procured and stocked sufficient NWA product to sustain existing programs during the period required to find a suitable alternative source.
Well, nonwoven aramid is back. Although I have tried to keep this column non-commercial, Arlon is, as best I know, the only company that has committed the resources and time to work with potential suppliers to develop a polyimide NWA that meets all the performance criteria of the original 85NT product.
In fact, what we have now is a drop-in replacement that will match both in process and properties of the original. That was not easy to accomplish and several very well qualified vendors tried and failed to meet the exacting requirements for the substrate. The project took longer than had originally been expected, though stocks of the old material have held up well enough to protect ongoing programs for the entire duration of the development program.
As you can see from the following microphotographs, the registration and hole quality of the new aramid reinforcement is essentially identical to that of the original DuPont product. The12-layer test coupons were made in the same press and lamination cycle using parameters developed for the original 85NT product.
For those who have been frustrated trying to find alternative technologies for their critical SMT boards, I think I can say with a great degree of confidence that Arlon’s 85NT is back and that you won’t be disappointed with its processability or performance.
Until next time, this is the Material Witness wishing you happy fabrication and a great fall 2015.
Chet Guiles is a consultant for Arlon Electronic Materials.
Testimonial
"The I-Connect007 team is outstanding—kind, responsive, and a true marketing partner. Their design team created fresh, eye-catching ads, and their editorial support polished our content to let our brand shine. Thank you all! "
Sweeney Ng - CEE PCBSuggested Items
Creating Connections in Mexico
07/30/2025 | Michelle Te, Community MagazineA concerted effort by the Global Electronics Association—Mexico team over the past year has created inroads for the Global Electronics Association (formerly IPC) with leading electronics companies, government offices, and academic institutions in Mexico. “Our goal is to bring more awareness to what the Global Electronics Association is and what it offers,” says Lorena Villanueva, senior director. “We also aim to increase our membership. Of 3,200 members of the Global Electronics Association, only 180 are in Mexico.”
Powering Progress: Summer 2025 Community Magazine Now Available
07/22/2025 | Community MagazineIn the new Summer 2025 edition of Community Magazine, members of the Global Electronics Association demonstrate what progress really looks like—through innovation on the factory floor, influence on public policy, and investment in the next generation of engineers.
TRI to Exhibit at SMTA Queretaro Expo 2025
07/16/2025 | TRITest Research, Inc. (TRI), the leading provider of test and inspection systems for the electronics manufacturing industry, is pleased to announce plans to exhibit at the SMTA Querétaro Expo 2025, scheduled to take place on July 24, 2025, at the Querétaro Centro de Congresos y Teatro Metropolitano.
Global PCB Connections: Let the Spec Fit the Board, Not Just the Brand
07/17/2025 | Jerome Larez -- Column: Global PCB ConnectionsIf you’ve ever seen an excellent PCB quote delayed, or worse, go cold because of a single line on the fab print, you’re not alone. Often, that line reads something like, “Use 370HR only,” or “IT-180A required.” These and other brand-name materials are proven performers, but unless your design needs that specific resin system (say, for RF performance, thermal reliability, or stringent CAF resistance), you may inadvertently be holding your job hostage.
IPC Hall of Fame Spotlight Series: Highlighting Lionel Fullwood
07/15/2025 | Dan Feinberg, I-Connect007Many IPC members who have contributed significantly to IPC and our industry have been awarded the IPC Raymond E. Pritchard Hall of Fame (HOF) Award. Though many early HOF members have passed away and are unknown to today’s IPC membership, their contributions still resonate. This special series on IPC Hall of Fame members provides a reminder of who was honored and why. As a bonus, for those who are still around, we get to find out what these talented individuals are up to today.