-
- News
- Books
Featured Books
- design007 Magazine
Latest Issues
Current IssueAll About That Route
Most designers favor manual routing, but today's interactive autorouters may be changing designers' minds by allowing users more direct control. In this issue, our expert contributors discuss a variety of manual and autorouting strategies.
Creating the Ideal Data Package
Why is it so difficult to create the ideal data package? Many of these simple errors can be alleviated by paying attention to detail—and knowing what issues to look out for. So, this month, our experts weigh in on the best practices for creating the ideal design data package for your design.
Designing Through the Noise
Our experts discuss the constantly evolving world of RF design, including the many tradeoffs, material considerations, and design tips and techniques that designers and design engineers need to know to succeed in this high-frequency realm.
- Articles
- Columns
- Links
- Media kit
||| MENU - design007 Magazine
Sensible Design: Conformal Coatings - Beware the Boards that ‘Bare’ All!
September 21, 2016 | Phil Kinner, ElectrolubeEstimated reading time: 2 minutes
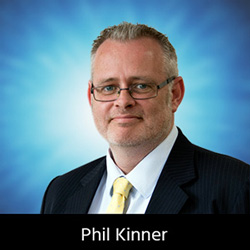
This month, I’m going to depart from my usual format of providing five essential facts about conformal coatings. Instead, I’m going to provide an account of a customer’s problem—no company names mentioned, of course—that brought into question the adhesion performance of a coating that they had been using successfully for some time.
This problem, and its eventual solution, illustrates rather well how good record-keeping, batch traceability, and the auditing of suppliers for quality control compliance can go a long way to help resolve manufacturing issues.
Always up for a challenge, and not wanting to ignore any production-related issue that appeared to cast a shadow over the performance of our products, we donned our detective hats and, with spyglasses at the ready, set about to discover the causes of this particularly challenging delamination problem. But first, let’s have a little bit of background.
Our customer—a multinational firm with sites around the world—contacted us about a coating they had been using without any problems for quite some time, but for some bizarre reason was “no longer sticking” to their boards. They reported that a newly delivered batch of this conformal coating, when applied, could be peeled from the solder mask areas in a single sheet. Our preliminary queries revealed that there had been no changes made to the coating process itself. So, was the coating at fault, or was there something else we were missing?
Delving a little deeper, we discovered that our customer was using this batch of coating material at several of its sites, both within the same country as the problem site, as well as sites located in other countries. It turned out these other sites had no issues to report regarding the coating, and they confirmed that they were experiencing neither the delamination problems we were investigating, nor indeed any problems related to a lack of adhesion. It was time to check the records.
Following a search through their database, the customer discovered they had coated four different styles of boards using the same batch of conformal coating material. Significantly, however, all of the adhesion issues were confined to a single board style. Moreover, these adhesion issues were first reported and recorded at about the same time.
On checking the serial numbers of the coated boards, it became apparent that the adhesion issues all began on a batch of bare boards that had been obtained from a new vendor as part of a cost-cutting measure. Samples of these incoming bare boards were subsequently analysed and found to have a surface energy of 26 dyne/cm (i.e., much, much less than the 40 dyne/cm level recommended for good adhesion).
Our customer then decided that perhaps it was high time to audit the new board supplier. During this process, they found many corners had been cut to save time and money, but two things, in particular, stood out. Firstly, the board shop was performing multiple passes through a UV oven to “cure” the solder resist, instead of the single recommended UV pass and a secondary thermal bake. Secondly, the auditor noted a “shiny film” floating on the surface of the rinse bath during the final rinse process.
To read this entire article, which appeared in the August 2016 issue of The PCB Design Magazine, click here.
Suggested Items
Driving Innovation: Direct Imaging vs. Conventional Exposure
07/01/2025 | Simon Khesin -- Column: Driving InnovationMy first camera used Kodak film. I even experimented with developing photos in the bathroom, though I usually dropped the film off at a Kodak center and received the prints two weeks later, only to discover that some images were out of focus or poorly framed. Today, every smartphone contains a high-quality camera capable of producing stunning images instantly.
Hands-On Demos Now Available for Apollo Seiko’s EF and AF Selective Soldering Lines
06/30/2025 | Apollo SeikoApollo Seiko, a leading innovator in soldering technology, is excited to spotlight its expanded lineup of EF and AF Series Selective Soldering Systems, now available for live demonstrations in its newly dedicated demo room.
Indium Corporation Expert to Present on Automotive and Industrial Solder Bonding Solutions at Global Electronics Association Workshop
06/26/2025 | IndiumIndium Corporation Principal Engineer, Advanced Materials, Andy Mackie, Ph.D., MSc, will deliver a technical presentation on innovative solder bonding solutions for automotive and industrial applications at the Global Electronics A
Fresh PCB Concepts: Assembly Challenges with Micro Components and Standard Solder Mask Practices
06/26/2025 | Team NCAB -- Column: Fresh PCB ConceptsMicro components have redefined what is possible in PCB design. With package sizes like 01005 and 0201 becoming more common in high-density layouts, designers are now expected to pack more performance into smaller spaces than ever before. While these advancements support miniaturization and functionality, they introduce new assembly challenges, particularly with traditional solder mask and legend application processes.
Knocking Down the Bone Pile: Tin Whisker Mitigation in Aerospace Applications, Part 3
06/25/2025 | Nash Bell -- Column: Knocking Down the Bone PileTin whiskers are slender, hair-like metallic growths that can develop on the surface of tin-plated electronic components. Typically measuring a few micrometers in diameter and growing several millimeters in length, they form through an electrochemical process influenced by environmental factors such as temperature variations, mechanical or compressive stress, and the aging of solder alloys.