-
- News
- Books
Featured Books
- design007 Magazine
Latest Issues
Current IssueAll About That Route
Most designers favor manual routing, but today's interactive autorouters may be changing designers' minds by allowing users more direct control. In this issue, our expert contributors discuss a variety of manual and autorouting strategies.
Creating the Ideal Data Package
Why is it so difficult to create the ideal data package? Many of these simple errors can be alleviated by paying attention to detail—and knowing what issues to look out for. So, this month, our experts weigh in on the best practices for creating the ideal design data package for your design.
Designing Through the Noise
Our experts discuss the constantly evolving world of RF design, including the many tradeoffs, material considerations, and design tips and techniques that designers and design engineers need to know to succeed in this high-frequency realm.
- Articles
- Columns
- Links
- Media kit
||| MENU - design007 Magazine
Sensible Design: The Little Guide to Resins
October 17, 2016 | Alistair Little, ElectrolubeEstimated reading time: 2 minutes
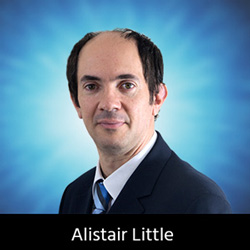
Over past months, this column has seen Electrolube’s Phil Kinner provide The PCB Design Magazine readers with information, guidance and practical tips on the uses and application of conformal coatings. He now hands over the reins to me, and I plan to do the same for resins, starting this month with a “back to basics” piece that questions the core rationale for potting—why and how do we do it, and what are we trying to achieve or protect?
First, a little background. I joined Electrolube as global business technical director for the Resins Division in January 2016. I currently head up a team of chemists developing formulations that encompass epoxy, polyurethane and silicone resin systems for encapsulating or potting electrical devices or electronic components in order to protect them against a wide range of environments.
In my previous appointment at Gurit (UK) I held the position of senior product development chemist, responsible for the development of new epoxy and vinyl ester resin systems for aerospace, automotive, engineering and marine composite systems. Prior to this, I worked for 2K Polymer Systems, where I developed civil engineering and structural adhesives, and at SI Group, where I worked on UV curing and high-performance resins.
I have wide experience working within ISO 9000, 14001 and 18001 accredited systems, and I am an expert in vinyl ester resin systems (for which I am in the process of completing a PhD in Polymer Chemistry at Loughborough University). I am a Chartered Chemist, an active member of the Royal Society of Chemistry, and a member of the Society of Adhesion and Adhesives.
Resins: Why, Where and How?
I would like to start this series of columns by going back to basics, questioning the core rationale for potting and encapsulation with resins, their fundamental chemistries and how each resin type differs one from the other—indeed, how their individual properties can be exploited to maximise performance under a wide range of environmental conditions.
Let’s start with moisture, the archenemy of electrical and electronic devices that, quite apart from causing short-circuits, can also lead to premature deterioration of components due to corrosion. Polyurethane resins—usually supplied as two-part products, which, when mixed achieve the desired cure—provide that all-important moisture resistance, as well as excellent electrical insulation, flexibility and good adhesion to most substrates, both metal and plastic. Some polyurethane resin systems provide exceptional resistance to sea water, as well as temperature extremes, making them an ideal choice for marine applications such as sensor encapsulation. A good outdoor example of a polyurethane resin encapsulated component that requires maximum protection against water ingress is an LED lighting unit; these resins are also optically clear and UV stable, making them ideal for the task.
To read this entire article, which appeared in the September 2016 issue of The PCB Design Magazine, click here.
Suggested Items
Moog Announces Acquisition of COTSWORKS
07/07/2025 | BUSINESS WIREMoog Inc., a worldwide designer, manufacturer and systems integrator of high-performance precision motion and fluid controls and control systems, announced the acquisition of COTSWORKS Inc., an aerospace and defense fiber optics transceiver component manufacturer, for a purchase price of $63 million.
S&K Aerospace Awarded Major Contract Under DLA Maritime Acquisition Advancement Program
07/02/2025 | BUSINESS WIRES&K Aerospace, LLC has been awarded a significant contract under the Defense Logistics Agency’s (DLA) Maritime Acquisition Advancement Program, managed by the U.S. Naval Supply Command - Weapon Systems Support (NAVSUP WSS) in Mechanicsburg, PA.
Green Circuits to Exhibit Full-Service Electronics Manufacturing Solutions at 2025 SMD Symposium
07/02/2025 | Green CircuitsGreen Circuits, a full-service Electronics Manufacturing Services (EMS) partner to leading OEMs, is pleased to announce its participation in the 2025 SMD Symposium, taking place August 5-7 at the Von Braun Center in Huntsville, Alabama.
I-Connect007 Editor’s Choice: Five Must-Reads for the Week
06/27/2025 | Nolan Johnson, I-Connect007While news outside our industry keeps our attention occupied, the big news inside the industry is the rechristening of IPC as the Global Electronics Association. My must-reads begins with Marcy LaRont’s exclusive and informative interview with Dr. John Mitchell, president and CEO of the Global Electronics Association. For designers, have we finally reached the point in time where autorouters will fulfill their potential?
Knocking Down the Bone Pile: Tin Whisker Mitigation in Aerospace Applications, Part 3
06/25/2025 | Nash Bell -- Column: Knocking Down the Bone PileTin whiskers are slender, hair-like metallic growths that can develop on the surface of tin-plated electronic components. Typically measuring a few micrometers in diameter and growing several millimeters in length, they form through an electrochemical process influenced by environmental factors such as temperature variations, mechanical or compressive stress, and the aging of solder alloys.