-
- News
- Books
Featured Books
- smt007 Magazine
Latest Issues
Current IssueIntelligent Test and Inspection
Are you ready to explore the cutting-edge advancements shaping the electronics manufacturing industry? The May 2025 issue of SMT007 Magazine is packed with insights, innovations, and expert perspectives that you won’t want to miss.
Do You Have X-ray Vision?
Has X-ray’s time finally come in electronics manufacturing? Join us in this issue of SMT007 Magazine, where we answer this question and others to bring more efficiency to your bottom line.
IPC APEX EXPO 2025: A Preview
It’s that time again. If you’re going to Anaheim for IPC APEX EXPO 2025, we’ll see you there. In the meantime, consider this issue of SMT007 Magazine to be your golden ticket to planning the show.
- Articles
- Columns
Search Console
- Links
- Media kit
||| MENU - smt007 Magazine
Increasing Reliability through Predictive Analysis
November 4, 2016 | Patty Goldman, I-Connect007Estimated reading time: 4 minutes
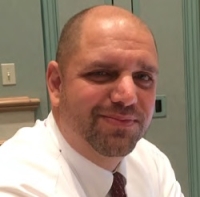
At SMTA International 2016, I caught up with Joe Russeau, president of Precision Analytical Laboratory, to discuss the paper he was presenting, which was co-authored by Mark Northrup and Tim Estes. Entitled, “Chemical Data vs. Electrical Data: Is One a Better Reliability Predictor,” the paper presents early data comparing the results of two different analytical test methods to determine how well they correlate with each other as predictors of PC board cleanliness and reliability.
Patty Goldman: Joe, can you please tell me, and our readers, a little bit about your co-authors?
Russeau: Mark Northrup is the VP of Technology for IEC Electronics. He’s the one that got us started on this project. Tim Estes is the CEO for Conductor Analysis Technologies.
Goldman: Tim is the PCQR² guy. So tell me about your involvement.
Russeau: As for my involvement, I own and operate a cleanliness testing lab. My focus at the lab is on residue analysis, so we do ion chromatography, surface insulation resistance and electrochemical migration testing. In my view, the three of us, with our different backgrounds, were an excellent fit to work together on this kind of study.
Goldman: So tell us about the paper and what prompted this testing.
Joe Russeau: Basically our paper is trying to compare whether or not there's any correlation between the electrical data generated by the PCQR² test—that's a conductive anodic filament (CAF) test—and IPC's ion chromatography test (IPC-TM-650, method 2.3.28). The concern here is that within the industry, there is an increasing drive to smaller devices. Component population densities are increasing as board real estate shrinks. Hence, there is an increased urgency in understanding cleanliness impacts to product reliability and how to accurately measure those risks before product goes into the field. The basis of the study was to compare what is currently available industry wide to ascertain which technique was better at predicting reliability. Mark Northrup, who is the primary researcher on this project, approached me and asked a couple of questions. The first question he asked was, “Do you know of any studies that show a correlation between the chromatography testing and any IPC electrical test?” To which I responded, “No, I wasn’t aware of any.” He followed up with a second question, which was, “Is one a better predictor of reliability?” To that I said, “I don’t have an answer.” Then he asked me if I'd be interested in participating in a study to try and determine an answer and that's how I got involved.
Goldman: I take it you guys have worked on this for some time now?
Russeau: Well, Mark and I have had numerous discussions about the limitations of circuit board cleanliness testing for the past few years. Mark motivated us a little over a year ago to initiate this study, and we did the testing over a span of about six months. We looked at a total of eight different groups of CAF coupons. The CAF coupons we used were the ones that the PCQR² document calls out. We looked at the ionic cleanliness of the coupons before they went into CAF using ion chromatography as a baseline. Subsequently, these tested coupons were submitted for CAF testing. Upon completion of the CAF testing, coupons were retested via ion chromatography for cleanliness again. The idea was to compare residue levels before and after to determine what changes occurred and if the chromatography could predict a CAF failure. Our hypothesis was that we would see a correlation between the CAF and IC tests. We applied IEC Electronics ionic cleanliness limits to the ion chromatography test results and the current criteria used for the PCQR2 test results to evaluate our hypothesis. We postulated that if there were residues that exceeded IEC Electronics ionic cleanliness limits before the CAF test, that corresponding failures should occur in the CAF test results. Of the eight groups, we had four groups that failed IC testing based on IEC Electronics ionic cleanliness limits and also failed CAF testing. The other four groups failed IEC Electronics ionic cleanliness limits, but passed CAF testing.
Based on this data, we drew the conclusion that there wasn't a significant correlation between the two tests, and in addition to that, we could not say definitively that either one of the tests was a better reliability predictor. We are still in the process of reviewing our methodologies and the variables that we want to do to try to improve the testing. We're just here today to present our initial data, hopefully get other people interested in the topic, solicit input as well for other ideas, and start a discussion of how to improve risk prediction for modern devices. Remember, this is just an initial test and is in no way definitive.
Goldman: I understand you’re presenting some early data; it sounds like there's much more to be done.
Russeau: That’s correct. We have a lot more testing to do. Within IPC, I am the chairman of the 7-11 Test Methods subcommittee. I also sit on other task groups related to chromatography and board cleanliness. We deal with these issues within those task groups all the time. We know there are limitations in the IPC test methods and that industry demands improved testing methods as electronics continuously increase in density. We're working both from the standpoint of industry people who are coming together on their own to look for ways to make improvements, and then we're also supporting the IPC test methods committees (e.g., 7-11 subcommittee where we're starting to require validation of methods). Ultimately, we're trying to make sure that IPC test methods correlate and have solid data to support their intended purpose, so we can get to better reliability predictors.
To read this entire article, which appeared in the November 2016 issue of SMT Magazine, click here.
Suggested Items
Indium to Feature Power Electronics Solutions at SEMICON Southeast Asia 2025
05/19/2025 | Indium CorporationAs a trusted leader in materials science for advanced electronics assembly, Indium Corporation® is proud to showcase its innovative power electronics solutions at SEMICON Southeast Asia 2025, May 20–22, in Marina Bay Sands, Singapore.
NEDME 2025 Announces Diverse and Distinguished Speaker Lineup
05/19/2025 | ASC SunstoneThe Northwest Electronics Design & Manufacturing Expo (NEDME) is thrilled to announce the impressive speaker lineup for the upcoming 2025 event. Taking place on Wednesday, October 22, 2025, at the Wingspan Event & Conference Center in Hillsboro, Oregon, NEDME 2025 will feature a dynamic array of thought leaders from across the electronics design and manufacturing sectors.
Incap Celebrates 40 Years with a Focus on Future Talent and Community Impact
05/19/2025 | IncapIncap Corporation, a global Electronics Manufacturing Services (EMS) provider and one of the top EMS companies in Europe, celebrates its 40th anniversary in 2025 by strengthening its commitment to community engagement and youth development in the regions where it operates.
4FRONT Solutions Invests in Seica’s PILOT V8 NEXT Flying Probe Tester to Enhance Test Capabilities at DeLand, FL Facility
05/16/2025 | Seica, Inc.Seica, Inc. is pleased to announce that 4FRONT Solutions has purchased and installed a PILOT V8 NEXT Flying Probe Tester at its electronics manufacturing facility in DeLand, Florida.
Flexible PCB Market to Reach $61.75B by 2032, Driven by the Demand for Compact Electronics, Automotive and Medical Applications
05/16/2025 | Globe NewswireAccording to the SNS Insider, “The Flexible PCB Market was valued at USD 21.42 billion in 2023 and is expected to reach $61.75 billion by 2032, growing at a CAGR of 12.52% over the forecast period 2024-2032.”