-
- News
- Books
Featured Books
- smt007 Magazine
Latest Issues
Current IssueIntelligent Test and Inspection
Are you ready to explore the cutting-edge advancements shaping the electronics manufacturing industry? The May 2025 issue of SMT007 Magazine is packed with insights, innovations, and expert perspectives that you won’t want to miss.
Do You Have X-ray Vision?
Has X-ray’s time finally come in electronics manufacturing? Join us in this issue of SMT007 Magazine, where we answer this question and others to bring more efficiency to your bottom line.
IPC APEX EXPO 2025: A Preview
It’s that time again. If you’re going to Anaheim for IPC APEX EXPO 2025, we’ll see you there. In the meantime, consider this issue of SMT007 Magazine to be your golden ticket to planning the show.
- Articles
- Columns
Search Console
- Links
- Media kit
||| MENU - smt007 Magazine
How to Improve PCB Reliability
November 9, 2016 | Patrick McGoff, Mentor Graphics Corp.Estimated reading time: 2 minutes
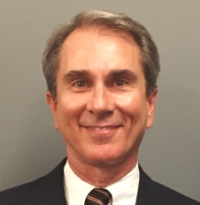
If you research electronics reliability for the automotive industry, for example, you will find they all address only the electronic components mounted on a PCB. One of the more referenced reliability studies for the industry was conducted by Telcordia Technologies, titled, "Reliability, Prediction Procedure for Electronic Equipment (SR-332)." Like most other electronics reliability studies, it excludes the PCB.
Automotive manufacturers need to have stringent reliability requirements, and thus they have set goals for reducing component defect rates. For example, a defect rate of less than 10 ppm for an engine control unit (ECU) or less than 1 ppm for a component within the ECU. The end game is "zero defect, zero failure."
The automotive industry has quantified the reliability rate for all the various component packages today and report defect rates as follows:
- ASIC—0.2 ppm
- Microprocessors—0.5 ppm
- Inductors—0.2 ppm
- Resistors—0.0 ppm
Component failure rates have steadily declined over the years to the point where non-component failure sources have become the dominant cause of failures for a PCB.
The problem with automotive-electronics reliability studies is they do not consider the PCB. If the reliability of the components is becoming a non-issue, then the only way to improve automotive electronics further is to look at the non-component aspects of the electronics, and a significant one is the PCB.
Each PCB design is a custom component, with its own unique, complex recipe:
- Material types and stackup
- Copper features
- Mechanical processes
- Chemical processes
- Electronic components
- Component mounting methodologies
- Impedance and capacitance concerns
All of the above form dependencies and constraints to every aspect of the PCB. How do you assess reliability for a “component” you have never used before? You measure the elements that make up the component, that is, the structure and features of the assembled PCB, including the solder-paste connection to the components.
First, measure and count the critical features of the PCB to assess the reliability of a custom component:
- Type of PCB—rigid, flex, flex-rigid, packaging substrate
- Size of PCB
- Number of layers
- Number of vias
- Size of vias
- Minimum annular ring
- Microvia stackup
- Number of component packages
- Double-sided SMT
- Range of package sizes
- Copper weight
- Copper distribution
- Test-point density
- Singulation method
- Zero-offset devices
- Gold fingers
- Vias in pad
- Embedded devices
- Aspect ratio
Second, list the electronic component and padstack details to be used to assess the reliability of a PCB assembly:
- Accurate body dimensions, preferably with tolerances
- Component standoff from PCB
- Lead type
- Pitch
- Smaller form packages are more susceptible to design and manufacturing issues
- Land pattern optimized for manufacturing
- TH pin diameter and length
- Solder mask-defined pads
Third, take into account the manufacturing processes used to produce the PCB:
- Conventional or sequential lamination
- Mechanical drill, laser drill or backdrill
- Number of panels stacked for drill
- Solder mask-defined pads
- Route or vscore singulation
- Flying prober or ICT
- Reflow, wave, or selective soldering
- Flow solder direction
- Conveyed edge for assembly
- SMT, auto-insertion, pressfit, or manual placement
- Stepped stencil
- Rework candidate
Manufacturing is a process, and processes also have tolerances. A reliability analysis needs to consider these fabrication tolerances.
To read this entire article, which appeared in the November 2016 issue of SMT Magazine, click here.
Suggested Items
Indium to Feature Power Electronics Solutions at SEMICON Southeast Asia 2025
05/19/2025 | Indium CorporationAs a trusted leader in materials science for advanced electronics assembly, Indium Corporation® is proud to showcase its innovative power electronics solutions at SEMICON Southeast Asia 2025, May 20–22, in Marina Bay Sands, Singapore.
The Test Connection Inc. Appoints USM Reps as Exclusive Sales Representative in Mexico
05/13/2025 | The Test Connection Inc.The Test Connection Inc. (TTCI), a leading provider of electronic test and manufacturing solutions, is pleased to announce the appointment of USM Reps as its exclusive sales representative in Mexico.
Innovative Technology Advancements in Test: HATS² Technology and Its Impact on Reliability Testing
05/14/2025 | Barry Matties, I-Connect007Ensuring the reliability of printed circuit boards (PCBs) has become increasingly difficult and critical, yet the development of advanced testing methodologies is essential to meeting industry demands and addressing persistent challenges. One significant innovation is the High Acceleration Thermal Shock (HATS²) test system, which transforms how reliability testing is conducted. After 40 years in the testing business at Microtek, Bob Neves is beginning a new journey with his company, Reliability Assessment Solutions Inc. (RAS).
ASC Acquires Cutting-Edge High Vacuum Plugging Machine CF 200 to Expand Via Fill Capabilities
05/12/2025 | American Standard CircuitsAnaya Vardya, President and CEO of American Standard Circuits and ASC Sunstone Circuits, has announced that the company has acquired and installed a state-of-the-art ITC Intercircuit CF 200 high vacuum plugging machine at its West Chicago manufacturing facility. This latest investment further strengthens ASC’s ongoing commitment to advanced manufacturing, precision engineering, and industry-leading process automation.
Indium Wins EM Asia Innovation Award
05/01/2025 | Indium CorporationIndium Corporation, a leading materials provider for the electronics assembly market, recently earned an Electronics Manufacturing (EM) Asia Innovation Award for its new high-reliability Durafuse® HR alloy for solder paste at Productronica China in Shanghai.