-
- News
- Books
Featured Books
- design007 Magazine
Latest Issues
Current IssueProper Floor Planning
Floor planning decisions can make or break performance, manufacturability, and timelines. This month’s contributors weigh in with their best practices for proper floor planning and specific strategies to get it right.
Showing Some Constraint
A strong design constraint strategy carefully balances a wide range of electrical and manufacturing trade-offs. This month, we explore the key requirements, common challenges, and best practices behind building an effective constraint strategy.
All About That Route
Most designers favor manual routing, but today's interactive autorouters may be changing designers' minds by allowing users more direct control. In this issue, our expert contributors discuss a variety of manual and autorouting strategies.
- Articles
- Columns
- Links
- Media kit
||| MENU - design007 Magazine
Estimated reading time: 2 minutes
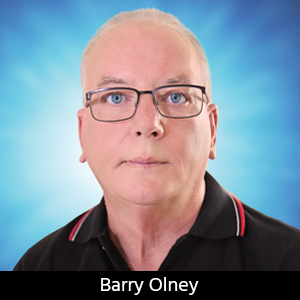
Beyond Design: Rock Steady Design
How do we ensure that our high-speed digital design performs to expectations, is stable given all possible diverse environments, and is reliable over the product’s projected life cycle? One word: Impedance!
For the perfect transfer of energy and to benefit from the highest possible bandwidth, the impedance of the driver must match the impedance of the transmission line and be constant along its entire length. Also, the power distribution network (PDN) must provide low AC impedance up to the maximum bandwidth and deliver an undisrupted, minimal return path for high-current switching devices. These two seemingly unrelated concepts are controlled by the PCB stackup configuration including material selection and should be analyzed concurrently.
For a sufficiently large number of electronics products, failures are distributed in time as shown in Figure 1. This curve is called “the bathtub curve” and displays the typical reliability of diverse products regardless of their functionality. One would expect a product to fail after some years of service, but preferably long after the product becomes obsolete. Premature failures are of particular concern and are typically the result of poor design practice or substandard manufacture. This column will focus on the design aspects.
In a previous column, Intro to Board-Level Simulation and the PCB Design Process, I mentioned that the cost of development is dramatically reduced if simulation is employed early in the design cycle. If changes are made late in the design process, then it takes more time, people, material and therefore money to complete the project. The advantage of simulation is that it identifies issues early in the design process and rectifies them before they become a major problem. Design changes that occur:
- In the conceptual stage cost nothing;
- During the design stage requires just a little extra time;
- During the test stage means that you have to regress one stage;
- During production, or worse still, in the field, can cost millions to fix and possibly damage the company’s reputation.
Reference designs are arguably the cause of many reliability issues. Many reference designs are developed by academics who are lacking the knowledge of DFM and reliability and have little appreciation for real-world industry expectations. And although their design may work on the test bench, it may not work in an adverse environment or with a variance of vendor components where the margins become borderline.
To read this entire article, which appeared in the October 2016 issue of The PCB Design Magazine, click here.
More Columns from Beyond Design
Beyond Design: Effective Floor Planning StrategiesBeyond Design: Refining Design Constraints
Beyond Design: The Metamorphosis of the PCB Router
Beyond Design: Radiation and Interference Coupling
Beyond Design: Key SI Considerations for High-speed PCB Design
Beyond Design: Electro-optical Circuit Boards
Beyond Design: AI-driven Inverse Stackup Optimization
Beyond Design: High-speed Rules of Thumb