-
- News
- Books
Featured Books
- design007 Magazine
Latest Issues
Current IssueAll About That Route
Most designers favor manual routing, but today's interactive autorouters may be changing designers' minds by allowing users more direct control. In this issue, our expert contributors discuss a variety of manual and autorouting strategies.
Creating the Ideal Data Package
Why is it so difficult to create the ideal data package? Many of these simple errors can be alleviated by paying attention to detail—and knowing what issues to look out for. So, this month, our experts weigh in on the best practices for creating the ideal design data package for your design.
Designing Through the Noise
Our experts discuss the constantly evolving world of RF design, including the many tradeoffs, material considerations, and design tips and techniques that designers and design engineers need to know to succeed in this high-frequency realm.
- Articles
- Columns
- Links
- Media kit
||| MENU - design007 Magazine
Resins: Five Essentials to Achieve the Right Cure
December 19, 2016 | Alistair Little, ElectrolubeEstimated reading time: 1 minute
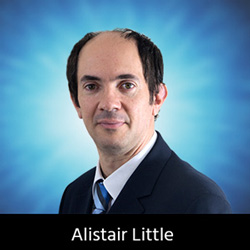
Last month, I looked at some of the critical things you need to consider before selecting your resin, which covered hardness, colour, viscosity and cure time. I do hope readers found this simple back-to-basics guide a useful starting point for further study and consultation. Of course, when it comes to the choice and application of resins, there’s a lot of information to take in, and over the following months I hope to distill this and provide some useful tips and design advice that will help you in your quest for reliable circuit protection.
Right, you’ve now chosen your two-part resin and it’s time to mix the components and get to work, so this month I’m going to turn my attention to the all-important job of mixing the resin (Part A, to use the terminology) and hardener (Part B), taking care that you get the ratio right and that you are conducting this critical part of the procedure under the right atmospheric conditions, and with all due regard for safety procedures. Get the mix wrong at this early stage and you will not achieve a satisfactory cure, which will ultimately lead to all sorts of problems later for the product you are potting or encapsulating. Anyway, continuing the five-point guide format that I introduced last month, here are five things to make yourself aware of before you start mixing.
Mix Ratio
Quite possibly the most critical aspect of resin mixing, which will have long term adverse repercussions if you get it wrong! There are two methods of mixing a resin with its associated hardener: by hand or using specialist dispensing equipment. If mixing by hand, then the ratio of the weight of the two components is the more useful method to employ. If mixing using dispensing equipment, then the volume ratio is used.
If the job is relatively small, then you are likely to use a resin pack, which provides the resin and hardener in precise quantities, in separate compartments of the pack. When you are ready to use the product, you simply remove the clip or other separating device between the compartments and ‘massage’ the resulting pouch, ensuring that both components are completely mixed.
To read this entire article, which appeared in the November 2016 issue of The PCB Design Magazine, click here.
Suggested Items
I-Connect007’s Editor’s Choice: Five Must-Reads for the Week
07/04/2025 | Marcy LaRont, I-Connect007For our industry, we have seen several bullish market announcements over the past few weeks, including one this week by IDC on the massive growth in the global server market. We’re also closely watching global trade and nearshoring. One good example of successful nearshoring is Rehm Thermal Systems, which celebrates its 10th anniversary in Mexico and the official opening of its new building in Guadalajara.
Count On Tools Recognizes Donna Orr’s Ongoing Leadership and Impact Across 27+ Years
06/26/2025 | Count On ToolsCount On Tools, Inc. (COT), a leading provider of precision components and SMT spare parts, is proud to recognize Donna Orr, Executive Manager, for her continued dedication and leadership as she marks more than 27 years with the company.
A Record Year for the 75th Annual IEEE Electronic Components and Technology Conference (ECTC)
06/26/2025 | ECTCThe 75th annual 2025 IEEE Electronic Components and Technology Conference (ECTC), held at the Gaylord Texan Resort & Convention Center here May 27-30, had record attendance, a record number of paper submissions/presentations, record international and student participation, and a record number of exhibitors in a sold-out exhibition hall:
The Death of the Microsection
06/26/2025 | Bob Neves, Reliability Assessment Solutions, Inc.I got my start out of college grinding and polishing PCB microsections. My thumbs are a bit arthritic today because of the experience (microsection grinders know what I mean). Back then, via structures were rather large, and getting to the center in six steps of grinding and polishing was easy compared to what my team has been doing recently at the lab.
Specially Developed for Laser Plastic Welding from LPKF
06/25/2025 | LPKFLPKF introduces TherMoPro, a thermographic analysis system specifically developed for laser plastic welding that transforms thermal data into concrete actionable insights. Through automated capture, evaluation, and interpretation of surface temperature patterns immediately after welding, the system provides unprecedented process transparency that correlates with product joining quality and long-term product stability.