-
- News
- Books
Featured Books
- design007 Magazine
Latest Issues
Current IssueAll About That Route
Most designers favor manual routing, but today's interactive autorouters may be changing designers' minds by allowing users more direct control. In this issue, our expert contributors discuss a variety of manual and autorouting strategies.
Creating the Ideal Data Package
Why is it so difficult to create the ideal data package? Many of these simple errors can be alleviated by paying attention to detail—and knowing what issues to look out for. So, this month, our experts weigh in on the best practices for creating the ideal design data package for your design.
Designing Through the Noise
Our experts discuss the constantly evolving world of RF design, including the many tradeoffs, material considerations, and design tips and techniques that designers and design engineers need to know to succeed in this high-frequency realm.
- Articles
- Columns
- Links
- Media kit
||| MENU - design007 Magazine
EIPC 2017 Winter Conference Review of Day 2
February 14, 2017 | Pete Starkey, I-Connect007Estimated reading time: 9 minutes
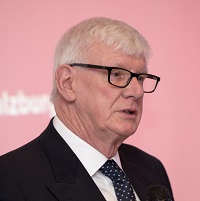
To read "EIPC 2017 Winter Conference Review of Day 1", click here.
Almost everyone made it back to the conference room for the start of the second day of the EIPC Winter Conference in Salzburg, even those who had enjoyed the late networking session into the early hours!
I had the privilege of moderating the first session, the theme of which was “Future Electronic Application and Impact on Reliability and Safety,” and my first presenter was Emma Hudson, UL’s Industry Lead for PCBs in Europe, the Middle East, Africa, and Latin America, and a member of the EIPC Board of Directors. She expertly steered delegates through the myths and mysteries of the safety certification process in a presentation entitled “UL PCB Recognition: A 20-minute guide to the UL 796 Safety Standard.”
She began by explaining that UL Recognition of components was driven by end-product safety concerns around fire and electric shock, and that UL’s PCB Requirements provided data characterising the behaviour of materials and PCBs, for use by the material manufacturer, the PCB fabricator and the end-product manufacturer as a guide in the design for safety in the use of components in devices or appliances.
There were four primary sections in UL 796: Introduction, Construction, Performance and Markings, plus a supplement to cover follow-up inspection. The standard only applied to rigid PCBs; flexible constructions were covered separately under UL 796F. Some of the terminology differed from common industry jargon; for example, a “single layer board” meant one with a single dielectric layer, not a single copper layer.
The Introduction section defined the parameters that would be evaluated. The section on Construction covered all the details required for a PCB to be “Recognized”—materials, build-up, parameters and manufacturing process. The Performance section covered test sample build-up requirements and test coupon design, and details of all the testing required. For full recognition, it was necessary to carry out all the tests; for flame-only recognition, only thermal shock and flammability were required. The Marking section defined all the mandatory marking requirements: company identification, factory identification, board type designation and UL recognition mark.
She made it clear that UL standards were consensus-based, and that the Standards Technical Panel (STP) process was governed by ANSI approved regulations. UL itself had only one vote, and of the 45 current panel members only two were from Europe. More representation from Europe was welcomed. “You can help to shape the UL Standards.”
Against the background picture that Emma Hudson had painted, a PCB industry user-perspective was presented by Jürgen Deutschmann, Supplier Quality Manager for AT&S Austria with responsibility for UL across the global AT&S group.
“What does the customer want to have?” was the fundamental question the PCB manufacturer needed to be sure to understand at the outset of a customer project. Full recognition? Flame-only recognition? What kind of maximum operating temperature? What kind of flammability class? What materials or material combinations? Then, having clearly understood the customer requirement, to check what was in the PCB manufacturer’s existing UL file and whether it was necessary to start a new UL project, in the knowledge that if any of the materials used was not UL recognized it cost a lot more money and running time. In Deutschmann’s experience, to get a material recognised took 2−3 months for flame-only recognition, and 5−6 months for full recognition, and he illustrated the sequence of release and the extensive schedule of testing that had to be completed.
He showed an example of a PCB manufacturer’s UL listing file and explained the significance of pattern limits, solder limits, maximum operating temperature, UL 94 flammability class and applicable solder resists, then clarified the procedure for correct UL-marking—what was mandatory and what was at the customer’s request.
“And now for something completely different:” I then introduced solder resist specialist Don Monn from Taiyo America, always a popular speaker at EIPC events, who prompted enormous interest from delegates with his presentation on heat-spreading solder resists.
Monn explained that conventional liquid photoimageable solder resists are relatively poor conductors of heat, but that dense PCB assemblies generate heat that needs to be dissipated by all means possible. And this had been an incentive for Taiyo to develop a new high-thermal-conductivity solder resist. Whereas a conventional resist formulation had small amounts of pigments and inorganic fillers in a continuous resin phase, and these components contributed little in the way of thermal conduction, the new formulation was heavily loaded with a thermally conductive ceramic material which provided a heat path between the PCB substrate and the outside environment where it releases the heat by radiation and convection.
The thermal conductivity of the new resist had been measured by the laser flash method, in which a laser pulse of 1 millisecond or less was used to momentarily heat the front side of a 2 mm thick sample, and the back-side temperature change was measured. The back-side temperature increased until it reached a constant value and the coefficient of thermal diffusivity could be calculated, which when multiplied by specific heat and density gave a thermal conductivity figure in Watts per metre Kelvin (W/m-K). The actual figure for the new formulation was 2.2W/m-K, compared to 0.2 W/m-K for a standard liquid photoimageable solder resist.
Monn demonstrated diagrammatically the routes by which the thermally-conductive solder resist acted to dissipate heat from component terminations and circuit features, supported by test results showing measured reduction in chip operating temperatures. The material had been subjected to exhaustive thermal cycling, with no cracking or peeling observed. It had very low moisture absorption characteristics and good resistance to ENIG chemistry. Because of the high filler content, photospeed was reduced, although the material remained suitable for laser direct imaging, with resolution equivalent to that of a standard liquid photoimageable solder resist.
The final session of the conference was moderated by EIPC Technical Director Michael Weinhold, on the theme of reliability of PCBAs and PCBs. His first presenter was Robert Boguski, president of Datest, a company of specialist test engineers for
assembled boards based in the USA. Boguski gave an enlightening insight into the world of non-destructive failure analysis, subtitled “Image and reality—matching findings (facts) with expectations (theories)—or not: Case studies from the coalface.”
Highly experienced in the interpretation of 2D and 3D X-ray images, backed by CT scanning capability, Boguski’s team effectively acted as a second pair of eyes to objectively examine what the customer had identified as a defective assembly. Was the customer always correct? Not very often! Customers with failed boards generally had predetermined notions of why their boards failed, often accompanied by assumptions that the root cause of failure lay with the highest-density components, for example BGAs, but these failures tended to lie elsewhere, for example resistors, capacitors, and other areas of the board. Boguski’s people had no preconceived ideas, just the benefit of understanding what they were looking at, and were particularly skilled in pattern recognition and spotting anomalies.
He showed many examples of case histories, in each case quoting what the customer had originally assumed was wrong and what was eventually found to be the real case—often a completely different story and often much more wrong than was originally thought. Significantly, bare-board defects were rarely seen—most were assembly-workmanship problems.
In some cases, Datest could identify and repair faults and bring failed assemblies back to full working order, in many instances recovering thousands of dollars-worth which would otherwise have been written-off. “Bone-pile rehabilitation” Boguski termed it, to the amusement of delegates. Whatever, Boguski was pleased to report: “Customers arrive confused and under pressure, and leave relieved and enlightened!”
Because Polar Instruments is nowadays recognised as the generic source of stack-up software for high-speed circuits, it is often overlooked that ever since its foundation 40 years ago, Polar has been involved in testing assembled boards. Hermann Reischer from Polar Instruments GmbH in Austria, gave a very informative presentation on efficient test methods for prototype builds and small batch production in electronics assembly.
Reischer reviewed the principles, advantages and limitations of a range of test methods: Functional Test, which checked for component internal functions, correct programming, etc. but located the result of a fault, not the root cause; In-Circuit-Test, which required complex programming and complex board interfacing; and Boundary-Scan-Test, which had simple interfacing but required complex programming; before discussing the principles of Analog Signature Analysis.
He explained that Analog Signature Analysis relied on a change in electrical characteristics to detect problems on a circuit board and would find typical production faults and defective components. It required no component library, was technology-independent, tested in the unpowered condition and programming was simple from a golden board. The technique did not measure component values or tolerances, gave limited test coverage for component internal faults and timing or thermal faults, and required some interpretation by the user.
The technique was to apply a current-limited AC sinewave across two points of a component or circuit, and display the resulting current/voltage waveform as a unique analog signature superimposed over a reference signature of a known good board. By comparing the signatures of known good circuit boards to those of suspect boards, faulty nets and components could be quickly identified. Reicher showed a series of illustrations of typical faults that had been identified. Polar had launched a new semi-automated graphical repair system, suitable for low volume high value production or R&D prototype testing and field returned repairs on high density loaded circuit boards.
The final presentation of the second day was given by Andreas Gombert from Ilfa in Germany, with a PCB manufacturer´s view on tolerance requirements for reliable PCBs. He explained that there were many tolerances defined for different features of PCBs, for example for annular rings, barrel thickness, registration, dielectric spacings and conductor patterns. Some were defined in standards such as IPC-2221. Some were based on specific project requirements, for example high-speed designs or HDI applications.
It was generally anticipated that conformity with the design ensured reliability for the complete assembly, although in general it was difficult to prove that conformity equalled reliability. He therefore presented the viewpoint of a PCB manufacturer on what he considered to be five of the most critical tolerances based on empirically gained experience: annular rings, barrel thickness, dielectric spacing, solder mask thickness and surface finishing. For each topic, he discussed the tolerance requirements in detail and gave examples of characteristic findings that would indicate a potential failure and therefore a reliability concern.
He concluded that the definition of minimum pad sizes to achieve annular rings in accordance with IPC-2221 was justified for difficult material combinations. Depending on the stack-up, smaller production tolerances were feasible but require case-by-case consideration. With respect to barrel thickness, his recommendation was to fulfil IPC Class 3 requirements even for Class 2 boards. He also recommended having positive etch-back in the range 5−10 microns. Dielectric spacing was critical for impedance-controlled conductors; the smaller the dielectric spacing, the larger was the impact of variations on impedance. The solder mask thickness had an impact on solderability, dielectric strength, and protection against the chemistry used in surface finishing, as well as on impedance. Finally, the tolerances of the surface finish influenced solderability, bondability and corrosion. He concluded by suggesting that anyone buying PCBs should first talk to their board supplier about tolerances: “They know what works and what does not, and what can be achieved…”
The proceedings were brought to a close by Alun Morgan, who thanked all present for supporting the event; the speakers for sharing their knowledge and experience the delegates for their attention and their participation, the sponsors Adeon, Isola, Polar and Ventec, and especially to Kirsten Smit-Westenberg and Carol Pelzers for their superb organisation of another successful EIPC conference. Morgan extended a warm invitation to everyone to come to Birmingham in the UK for the Summer Conference on 1st−2nd June.
I am grateful to Alun Morgan for allowing me to use his photographs.
Suggested Items
Driving Innovation: Direct Imaging vs. Conventional Exposure
07/01/2025 | Simon Khesin -- Column: Driving InnovationMy first camera used Kodak film. I even experimented with developing photos in the bathroom, though I usually dropped the film off at a Kodak center and received the prints two weeks later, only to discover that some images were out of focus or poorly framed. Today, every smartphone contains a high-quality camera capable of producing stunning images instantly.
Hands-On Demos Now Available for Apollo Seiko’s EF and AF Selective Soldering Lines
06/30/2025 | Apollo SeikoApollo Seiko, a leading innovator in soldering technology, is excited to spotlight its expanded lineup of EF and AF Series Selective Soldering Systems, now available for live demonstrations in its newly dedicated demo room.
Indium Corporation Expert to Present on Automotive and Industrial Solder Bonding Solutions at Global Electronics Association Workshop
06/26/2025 | IndiumIndium Corporation Principal Engineer, Advanced Materials, Andy Mackie, Ph.D., MSc, will deliver a technical presentation on innovative solder bonding solutions for automotive and industrial applications at the Global Electronics A
Fresh PCB Concepts: Assembly Challenges with Micro Components and Standard Solder Mask Practices
06/26/2025 | Team NCAB -- Column: Fresh PCB ConceptsMicro components have redefined what is possible in PCB design. With package sizes like 01005 and 0201 becoming more common in high-density layouts, designers are now expected to pack more performance into smaller spaces than ever before. While these advancements support miniaturization and functionality, they introduce new assembly challenges, particularly with traditional solder mask and legend application processes.
Knocking Down the Bone Pile: Tin Whisker Mitigation in Aerospace Applications, Part 3
06/25/2025 | Nash Bell -- Column: Knocking Down the Bone PileTin whiskers are slender, hair-like metallic growths that can develop on the surface of tin-plated electronic components. Typically measuring a few micrometers in diameter and growing several millimeters in length, they form through an electrochemical process influenced by environmental factors such as temperature variations, mechanical or compressive stress, and the aging of solder alloys.