-
- News
- Books
Featured Books
- smt007 Magazine
Latest Issues
Current IssueIntelligent Test and Inspection
Are you ready to explore the cutting-edge advancements shaping the electronics manufacturing industry? The May 2025 issue of SMT007 Magazine is packed with insights, innovations, and expert perspectives that you won’t want to miss.
Do You Have X-ray Vision?
Has X-ray’s time finally come in electronics manufacturing? Join us in this issue of SMT007 Magazine, where we answer this question and others to bring more efficiency to your bottom line.
IPC APEX EXPO 2025: A Preview
It’s that time again. If you’re going to Anaheim for IPC APEX EXPO 2025, we’ll see you there. In the meantime, consider this issue of SMT007 Magazine to be your golden ticket to planning the show.
- Articles
- Columns
Search Console
- Links
- Media kit
||| MENU - smt007 Magazine
Industry 4.0: Nine Key Points Electronics Manufacturers Must Not Ignore
March 2, 2017 | Russell Poppe, JJS ManufacturingEstimated reading time: 3 minutes
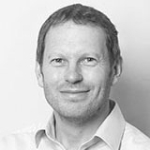
The Fourth Industrial Revolution is nothing if not massive and complicated. There is a huge amount of information out there, some useful and some perhaps less so. But, among the hype, waffle and thinly-disguised sales pitches, there are a few consistent themes that really must not be ignored by manufacturers wishing to remain competitive in the future.
The convergence of new technologies and innovative thinking is already transforming the way electronics manufacturers work, and this is set to continue.
Here are nine key concepts that ought to be considered as part of any strategy for the future:
1. Digital Darwinism
"It is not necessary to change. Survival is not mandatory" - W. Edwards Deming
Industry 4.0, and all that entails, is happening. This might not be clearly apparent as the process is far more advanced in some countries and industries than others, but many companies are already enjoying the competitive advantages of adopting new technologies and working practices. Never the less, there will be those who choose to ignore the digital revolution, and they may well be OK for a few years as the world changes around them. In the end, though, it will only be the fittest, most competitive that survive.
2. Facts-based business
Machines and processes are increasingly able to generate data that can be analyzed through digital business intelligence (BI) systems. These provide concrete facts on which to base decisions, rather than assumption, guesswork or gut feel. This leads to more efficient resolution of issues and improvement of processes, creating a more competitive environment.
3. Real time
With the increase in available information comes the need to interpret and act on it in real time. This might come from customers needing to know the status of their order or delivery, or from the manufacturing plant wanting to identify and fix process issues quickly, as they occur, reducing waste and increasing efficiency.
4. Digital infrastructures, physical manufacturing
We do and will still need machines and people to physically make products. Pretty much everything else, though, can be digital. IT systems have never been so important, and need to be structured in such a way to easily interface with the physical world.
5. Factory models
Manufacturing process models are changing. Requirements, such as late customization (i.e. configure to order just before shipping) and distributed manufacturing (making things on sites close to their end markets to reduce transport costs and lead times), are and will continue to dramatically change the way factories are set up and run. Automation and advanced IT systems are required to support this.
6. The circular economy
As the world runs short on resources – and yes it really is – then products will be increasingly designed for easy upgrade, recycling, servicing and repairs. Many will move to a "pay-per-use" supply rather than outright purchase. Again, this greatly affects the services that manufacturers will need to offer: spares, upgrade kits/services and so on will become as important as the production of the original equipment. The arguments for design-focused companies to move away from OEM to sub-contract manufacturing will become even stronger as the production and fulfillment operations become even more complex.
7. Digital collaboration
The flow of information between customer, manufacturer and materials suppliers is becoming increasingly digitized and shared. This provides many opportunities for much improved efficiency and flexibility. Data security does, however, become a primary concern.
8. Raw material takes control
Rather than a production system being programmed to perform actions on raw material, the material itself will tell the production system what to do with it. Why? Again, it's about flexibility and customization. This technology may be a little way off for many manufacturers, but it's a good example of how manufacturing sites might need to completely re-think their production operations.
9. Servitised business models
Manufacturers will have to recognize (though the good ones will have already) that they are a service organization that provides manufacturing as a part of the service offering. The opportunities for pure "manufacturers" will be very limited, as customers look for additional added value in the provision of other services, some of which are described above.
Of course, a lot of these ideas overlap, combine and complement each other. Many of the traditional boundaries around certain aspects of manufacturing are blurring and merging, and forming a coherent strategy to deal with all this is undoubtedly a challenge. Exciting times indeed for those willing to embrace it, but perhaps the beginning of the end for those who won't?
The article originally appeared on the JJS Manufacturing blog, which can be found here.
Suggested Items
Sanmina Announces Acquisition of Data Center Infrastructure Manufacturing Business of ZT Systems from AMD
05/19/2025 | PRNewswireSanmina Corporation, a leading integrated manufacturing solutions company, announced that it has entered into a definitive agreement to acquire the data center infrastructure manufacturing business of ZT Systems, a leading provider of Cloud and AI infrastructure to the world's largest hyperscalers, from AMD.
NEDME 2025 Announces Diverse and Distinguished Speaker Lineup
05/19/2025 | ASC SunstoneThe Northwest Electronics Design & Manufacturing Expo (NEDME) is thrilled to announce the impressive speaker lineup for the upcoming 2025 event. Taking place on Wednesday, October 22, 2025, at the Wingspan Event & Conference Center in Hillsboro, Oregon, NEDME 2025 will feature a dynamic array of thought leaders from across the electronics design and manufacturing sectors.
Creation Technologies Celebrates Ribbon Cutting of Expanded Denver Product Realization Center
05/19/2025 | Creation TechnologiesCreation Technologies, an end-to-end, scalable Specialty Global Electronic Manufacturing Services provider, proudly celebrated the official ribbon-cutting ceremony of its newly expanded Denver Product Realization Center on Monday, May 12, 2025.
Robust.AI Partners With Foxconn to Accelerate and Scale Manufacturing of Carter Warehouse Automation Robots
05/16/2025 | BUSINESS WIRERobust.AI, a leader in AI-driven warehouse automation, announced a strategic manufacturing partnership with Hon Hai Technology Group (Foxconn), the world’s largest electronics manufacturing services provider, to expand production of its flagship Carter™ multi-function collaborative robotics platform.
4FRONT Solutions Invests in Seica’s PILOT V8 NEXT Flying Probe Tester to Enhance Test Capabilities at DeLand, FL Facility
05/16/2025 | Seica, Inc.Seica, Inc. is pleased to announce that 4FRONT Solutions has purchased and installed a PILOT V8 NEXT Flying Probe Tester at its electronics manufacturing facility in DeLand, Florida.