-
- News
- Books
Featured Books
- design007 Magazine
Latest Issues
Current IssueAll About That Route
Most designers favor manual routing, but today's interactive autorouters may be changing designers' minds by allowing users more direct control. In this issue, our expert contributors discuss a variety of manual and autorouting strategies.
Creating the Ideal Data Package
Why is it so difficult to create the ideal data package? Many of these simple errors can be alleviated by paying attention to detail—and knowing what issues to look out for. So, this month, our experts weigh in on the best practices for creating the ideal design data package for your design.
Designing Through the Noise
Our experts discuss the constantly evolving world of RF design, including the many tradeoffs, material considerations, and design tips and techniques that designers and design engineers need to know to succeed in this high-frequency realm.
- Articles
- Columns
- Links
- Media kit
||| MENU - design007 Magazine
A New Power Design Methodology for PCB Designs
March 15, 2017 | Dingru Xiao, Cadence Design SystemsEstimated reading time: 2 minutes
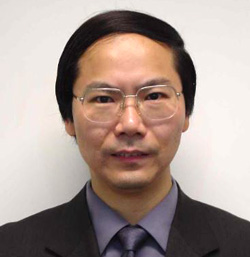
Abstract
Advanced PCB design is an iterative process of analysis-fix-analysis. Historically, this process is very time-consuming, requiring analysis experts and PCB designers to work together to find and fix layout problems. This article describes a new PCB design methodology that allows a PCB designer to perform the power design without having to run expert-level analysis tools. This methodology provides the setup automation for advanced analysis without the need to understand every minute parameter, and can be completed in a few steps.
User-friendly analysis reports guide the PCB designer to the exact location where design changes must be made to meet specifications. IPC standard-based constraint of automatic calculations helps PCB designers understand how good is good enough for the layout changes. All violations of IPC standards can be marked directly in the layout, so PCB designers can easily find the problems in the layout and fix them before handing the design over to the power integrity (PI) experts. This allows PI experts focus on performance optimization, cost reduction, and other issues, so a high-quality design can be produced in a shorter amount of time.
For modern electronic systems, power design has become more important with the requirements of low power, minimization, high density and high-speed data rate for high-end applications. Usually, the planes, copper pours, routed power traces and vias on a PCB serve as power distribution, signal return paths, heat dissipation and so on.
The following questions must be considered:
- How does the PI engineer communicate with the hardware engineer and PCB designer about problems with the design and guidance on how to fix it?
- How does the PCB designer communicate with the PI engineer about solutions to those problems?
- How can the design engineer and PCB designer determine whether a solution is good in the early stage?
Generally, PI engineers communicate with PCB designers by email, phone calls, or meeting face to face to discuss the issues and the solutions to fix problems with the layout.
Unlike when analyzing signal integrity, PI engineers are not usually involved in the early stages of the design because of the lack of pre-layout analysis tools for power analysis in the industry. The first cut of PCB power design usually is based on experience and industry conventions, so many power problems only surface late in the process, leaving PI engineers to focus mainly on the post-layout verifications for power systems. Also, PCB designers generally do not want to use professional analysis tools because of their complicated settings and different EDA tools/platforms.
This lag time greatly affects the efficiency of design and the time-to-market of the products.
To read this entire article, which appeared in the February 2016 issue of The PCB Design Magazine, click here.
Suggested Items
Trouble in Your Tank: Can You Drill the Perfect Hole?
07/07/2025 | Michael Carano -- Column: Trouble in Your TankIn the movie “Friday Night Lights,” the head football coach (played by Billy Bob Thornton) addresses his high school football team on a hot day in August in West Texas. He asks his players one question: “Can you be perfect?” That is an interesting question, in football and the printed circuit board fabrication world, where being perfect is somewhat elusive. When it comes to mechanical drilling and via formation, can you drill the perfect hole time after time?
The Evolution of Picosecond Laser Drilling
06/19/2025 | Marcy LaRont, PCB007 MagazineIs it hard to imagine a single laser pulse reduced not only from nanoseconds to picoseconds in its pulse duration, but even to femtoseconds? Well, buckle up because it seems we are there. In this interview, Dr. Stefan Rung, technical director of laser machines at Schmoll Maschinen GmbH, traces the technology trajectory of the laser drill from the CO2 laser to cutting-edge picosecond and hybrid laser drilling systems, highlighting the benefits and limitations of each method, and demonstrating how laser innovations are shaping the future of PCB fabrication.
Day 2: More Cutting-edge Insights at the EIPC Summer Conference
06/18/2025 | Pete Starkey, I-Connect007The European Institute for the PCB Community (EIPC) summer conference took place this year in Edinburgh, Scotland, June 3-4. This is the third of three articles on the conference. The other two cover Day 1’s sessions and the opening keynote speech. Below is a recap of the second day’s sessions.
Day 1: Cutting Edge Insights at the EIPC Summer Conference
06/17/2025 | Pete Starkey, I-Connect007The European Institute for the PCB Community (EIPC) Summer Conference took place this year in Edinburgh, Scotland, June 3-4. This is the second of three articles on the conference. The other two cover the keynote speeches and Day 2 of the technical conference. Below is a recap of the first day’s sessions.
Preventing Surface Prep Defects and Ensuring Reliability
06/10/2025 | Marcy LaRont, PCB007 MagazineIn printed circuit board (PCB) fabrication, surface preparation is a critical process that ensures strong adhesion, reliable plating, and long-term product performance. Without proper surface treatment, manufacturers may encounter defects such as delamination, poor solder mask adhesion, and plating failures. This article examines key surface preparation techniques, common defects resulting from improper processes, and real-world case studies that illustrate best practices.