-
- News
- Books
Featured Books
- design007 Magazine
Latest Issues
Current IssueAll About That Route
Most designers favor manual routing, but today's interactive autorouters may be changing designers' minds by allowing users more direct control. In this issue, our expert contributors discuss a variety of manual and autorouting strategies.
Creating the Ideal Data Package
Why is it so difficult to create the ideal data package? Many of these simple errors can be alleviated by paying attention to detail—and knowing what issues to look out for. So, this month, our experts weigh in on the best practices for creating the ideal design data package for your design.
Designing Through the Noise
Our experts discuss the constantly evolving world of RF design, including the many tradeoffs, material considerations, and design tips and techniques that designers and design engineers need to know to succeed in this high-frequency realm.
- Articles
- Columns
- Links
- Media kit
||| MENU - design007 Magazine
Mike Carano on the First PCB Executive Forum Held at IPC APEX EXPO 2017
March 27, 2017 | Patty Goldman, I-Connect007Estimated reading time: 13 minutes
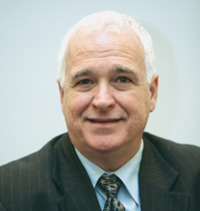
When John Mitchell came on board as president of IPC, he decided to tap the members of the Raymond E. Pritchard Hall of Fame for suggestions and advice. So he established the IPC Ambassador Council and tasked them to create special programs for IPC conferences. It is this group of people who put together the recent PCB Executive Forum that was presented at IPC APEX EXPO 2017. A few of those individuals were highly instrumental in developing that program, especially Gene Weiner of Weiner Associates, Mike Carano, of RBP Chemical Technology, and Jack Fisher.
The morning after the event, I sat down with Mike to hear his thoughts.
Patty Goldman: Mike, we’ve been discussing the PCB Executive Forum with other Council members and I thought perhaps you would like to comment on that. We could start with a little background on the Council.
Mike Carano: The team here at the Ambassador Council is made up of the elected members of the Raymond E. Pritchard IPC Hall of Fame, recognizing those individuals that have made significant lifetime contributions to IPC and to the membership. I'm chairman of the Council and you are a member as well. This group gets together at these meetings along with monthly conference calls, and we are trying to provide more give-back to our industry by organizing webinars, mentoring some of the younger engineers and other folks who are in this industry. We organized the PCB Executive Forum, which was held on Monday here at IPC APEX EXPO, to provide content, actionable items, and useful information for the PCB fabricator community.
Goldman: It was for executives in the PCB industry, correct?
Carano: Yes, for both the suppliers to the PCB industry and the fabricators, but we really focused on attracting the PCB fabricators. And we did get a number of fabricators who found the program useful, including Colonial Circuits, FTG, IMI, Flex Interconnect, and several others. Kudos to the organizers, particularly Gene Weiner and Jack Fisher who put together the program. The content covered a broad spectrum—everything from technology scans to how a company like Flex/Multek actually goes about investing in emerging technologies and how they continue to grow their company. Dr. Joan Vrtas spoke about that. We also had gentlemen from the Department of Commerce talking about their PWB survey of capabilities.
Goldman: I found that to be very interesting.
Carano: It was very interesting and eye opening as to how the printed circuit board fabrication landscape in North America shapes up. In particular, the reason the study was done was to determine how many of these fabricators in North America, being U.S. owned, are truly capable of supplying technology and circuit boards to the U.S. military. Because that's a key issue with all the regulations of ITAR and MIL specs, and this study, while not fully complete and published yet, was giving us a sneak peek at the survey results and it did show that there are some areas that could be improved for the fabrication base. But by and large it showed that quite a few of the fabricators in the United States and, indeed in North America who are MIL-spec approved, are capable of supplying to the military. The question is: Where does that go from here? There's a lot of concern about where the political landscape will be over the next two years. So this was valuable information.
In addition, there was the great panel discussion comprised of fabricators and suppliers, including equipment and chemical, as well as three fabricators. They talked about their challenges in this industry and what it's like to compete as a privately held small company in an era where capital formation and getting loans and being able to grow their business is not exactly robust. It was interesting as they talked about everything from tax reforms to capital expenditures to getting people. You know, that's a big thing right now. We're getting grayer in this industry and the ability to attract younger engineers to take over the reins and get excited about our industry is a challenge right now.
Goldman: It’s also a challenge to find experienced people. Finding anyone with engineering experience is almost impossible, so I understand. What were some of the other presentations?
Carano: We heard from several other companies or speakers talking about new technologies. Dan Feinberg gave an interesting presentation. As you know, Dan Feinberg is also a member of the Hall of Fame, and he is a regular attendee of CES, the Consumer Electronics Show in Las Vegas. He has an inside track and being a techie himself, Dan attends this show every year and spends quite a bit of time looking at new technology—everything from IoT developments to autonomous cars to disruptive technology. What's going to change our industry? What new technologies might make it either more difficult to compete if you don't invest, or could potentially obsolete your technology?
One of the things that's been coming up in the last couple of years has been 3D printing, or as we like to call it, additive technology. Regardless, additive technology is here. It's necessary. If you want to get finer lines in places, you must find a way to make finer circuits reliably and the conventional, subtractive ways of doing things, where you put an ounce of copper on and strip it away is not going to cut it. So additive technology has been around, but it needs to be further refined in terms of the dielectrics and the process. So 3D printing is a big deal and Dan showed how some companies were actually making quick-turn prototype multi-layer boards with this technology.
Goldman: He had some really interesting photos.
Carano: Then of course both Dr. Vrtas and Dan Feinberg talked about the autonomous car and autonomous driving.
Goldman: And virtual reality. Joan showed such an interesting video on virtual reality.
Carano: Yes, you could be sitting in your living room with your virtual reality glasses on and talking to your kids who are in Europe or somewhere and it looks like they're sitting right there with you, the entire image of your kids, and you're basically touching a screen that's, well, virtual. So these technologies are there and it's about time that the mainstream comes forth and starts to push that. Now, to further that, Joan Vrtas from Flex/Multek also talked about these very same things and how these opportunities are very important. Because, as she said, everything needs to be interconnected.
Everything starts with a circuit board. Whether it's flex, rigid-flex or both, everything needs to be right in terms of printed circuit board technology. Suppliers, fabricators, have to adapt to what those changes are. Will they invest in the technology to get the finer features and smaller holes? But she was very encouraging about how their view, and Multek knows what they're talking about, is moving forward. She also talked about how Flex watches technologies that might be emerging. They do a technology scan and they watch these things. Some may pan out, some may not, some may be totally disruptive, but they watch these things.
Goldman: They've got their finger on the pulse.
Carano: Right, and they even sometimes invest in these small companies or these ideas, using them as incubators. So that was a great idea. Then there was Brad Bourne, CEO and president of FTG Circuits, which is a publicly traded, Canadian printed circuit board company dealing in cockpit displays for airplanes and printed circuit boards—high-end, particularly for military. He talked about the struggles even as a company that's not that small, maybe $70–80 million and publicly traded, he talked about the challenges of the company and currency fluctuations, but he especially talked about the importance of focus. Focusing your company, sticking to your knitting, try not to be all things to all people, and I think his two big messages were first that you have to persevere, you have to stay the course. Stick with it, and you can't be all things to all people. The second thing was there are certain things you can't fight. For example, he has to deal with currency fluctuations because he's a Canadian company, he bills in Canadian dollars, he pays his people in Canadian dollars, but he has a U.S. operation. So there's a company that has made great strides over the last couple of years, but it shows how a company that can focus and make the right investments can move forward.
Goldman: The other thing he pointed out was that overnight success doesn't happen overnight, and he was happy to admit that sometimes things took ten years for them, but that's why you need that perseverance. You’ve got to stick with it.
Carano: Yes, and when companies do stick to a strategy and they're going down the right path and they see that, sometimes they have to resist the temptation of trying to do more when they're already on the right path. You know, narrow it down to a focus. I know in our business we can't have a hundred projects going on at one time. At RBP Chemical Technology, we focus on those three or four and we stick to them until they're complete. Now if we find out the time has ended for one, then we'll kill the project and we'll do it quickly, but when you're on the right track and it's what your customers want and it's what their needs are, you can't take on another 30, 40, or 50% more projects.
Goldman: No matter how exciting they look, right? You've got to finish up something first.
Carano: Otherwise you'll be looking at two years from now and you'll have more projects and none of them are done. So that was a great message yesterday. I think for the folks in the room, both the attendees who are in the fabrication supply business, as well as those who participate either on the panel discussions or were presenters, it showed how if you do focus and you do work hard, you can survive and prosper like Colonial Circuits and Chemcut, on the equipment side, and Flex Interconnect, IMI with Peter Bigelow, and Eagle Circuits. They've all been around, we've all known them for years, and they're all still in business. They're doing something right and they should pat themselves on the back and I think it was very encouraging. I believe we're going to do this Executive Forum next year.
Goldman: I was just going to ask about that.
Carano: We made the decision as a group here among the Ambassador Council members and we're going to push it hard again and we've got some great opportunities for people to participate. So we encourage everyone to participate and don't say that IPC is not hearing your voice. You’ve got to speak or say something, not just be unhappy when something doesn't go your way. You can't just take your ball and go home. You’ve come in and play and if you get knocked down at least we know you're there. That's really the message, and we hope that more people will get involved in the next forum—and IPC in general.
Goldman: I understand there's also another educational forum coming up.
Carano: There are several. For one of them I'm chairman and a session organizer and that will be the Reliability Conference in Chicago on April 26th and 27th. We're going to have a heavy military/auto twist to it. Phil Titterton, who is the president of the mil/aero group at TTM, will be there. Phil will be the keynote and we're proud to have him. We also have some other great speakers from the mil/aero side and the automotive side.
Goldman: And I saw Lockheed Martin was on the list.
Carano: That's correct, and then later, June 27 and 28, we're having the European Reliability Conference that will also be heavily automotive. Major European OEMs like Bosch, Siemens, and Mercedes will be participants; this will be the fourth forum that we've put on in Germany and they've all been successful. I participated in those as well and we're going to be there again to keep pushing the envelope. Then later in October we're going to host the IPC HDI flexible circuit conference, a two-day event in the Minneapolis area near the airport, all about HDI and flex.
Two years ago, when we had the forum in Minneapolis, we had 110 people for the two days on a standalone conference, and we decided we were going to talk about both HDI and flex, instead of just one or the other. I'm also chair of that session and chair of the organization along Sanjay Huprikar from IPC, and we encourage people who have something to say, if you want to attend, that is great; but if you want to speak and you've got a topic in the area of HDI and flex, whether it's on materials, reliability, process, new ideas about how to manage that type of thing, software that you want to talk about, and how to design HDI.
Goldman: Speak up and be part of the solution!
Carano: That's right.
Goldman: I had another question for you. We also had a group dinner last night which combined the PCB executive forum attendees with the EMS forum attendees and I thought that was a great time to have a lot of interaction back and forth between the PCB companies and EMS companies. That was a good time to exchange information, views, and meet new people.
Carano: Networking is critical. You get different views, you get people from all industries, or segments within our supply chain. But let's face it, if you remember the old CSI: New York crime drama that used to be on TV, Gary Sinise was the chief investigator in the crime lab, and he said, “Everything's connected.” Basically, everything in our supply chain is connected: assembly, design, fabrication, chemical and material suppliers, end users. Everything's connected and the way to do this is to network and be part of these forums where you bring the entire supply chain together.
Goldman: I always have to make a plug for the IMPACT Washington, D.C. event that will take place at the beginning of May this year. Along the same lines of speaking up, it's the best year ever to get your voice heard in Washington, so I don't know if you've been involved, but I'll tell you, it's really worthwhile.
Carano: It's a great forum. We'll be having our spring IPC board meeting in conjunction with that, so the board members will be there, too.
Goldman: So you'll be there, and I’m hoping we'll have a really large group to make a big impression on congress and beyond down there.
Carano: That again is the thing though. It's about participation, Patty.
Goldman: If you don't speak up, you're not going to get heard.
Carano: Now granted, I know some IPC members and non-members do, during the year, host their local officials, but many of them don't and they want to know why this organization can't do more for them on the government level, but that's not the point. The IPC is doing a huge amount. They’ve focused, and they have a team of government advocates in Washington, D.C. fighting these battles every day.
Goldman: The thing about IMPACT is they set up the meetings for you and guide you every step of the way. But you’ve got to go because congress wants to hear from their constituents, not some guy we hired to be there.
Carano: Exactly, you’ve got to be there. Meet me halfway, show up.
Goldman: They'll also set up the whole visit at your company for a government official, but you’ve got to have the doors open and you have to meet them halfway, like you said. A lot of things are going on. Mike, thank you so much and we'll talk later.
Carano: Thanks Patty.
Suggested Items
Trouble in Your Tank: Can You Drill the Perfect Hole?
07/07/2025 | Michael Carano -- Column: Trouble in Your TankIn the movie “Friday Night Lights,” the head football coach (played by Billy Bob Thornton) addresses his high school football team on a hot day in August in West Texas. He asks his players one question: “Can you be perfect?” That is an interesting question, in football and the printed circuit board fabrication world, where being perfect is somewhat elusive. When it comes to mechanical drilling and via formation, can you drill the perfect hole time after time?
The Evolution of Picosecond Laser Drilling
06/19/2025 | Marcy LaRont, PCB007 MagazineIs it hard to imagine a single laser pulse reduced not only from nanoseconds to picoseconds in its pulse duration, but even to femtoseconds? Well, buckle up because it seems we are there. In this interview, Dr. Stefan Rung, technical director of laser machines at Schmoll Maschinen GmbH, traces the technology trajectory of the laser drill from the CO2 laser to cutting-edge picosecond and hybrid laser drilling systems, highlighting the benefits and limitations of each method, and demonstrating how laser innovations are shaping the future of PCB fabrication.
Day 2: More Cutting-edge Insights at the EIPC Summer Conference
06/18/2025 | Pete Starkey, I-Connect007The European Institute for the PCB Community (EIPC) summer conference took place this year in Edinburgh, Scotland, June 3-4. This is the third of three articles on the conference. The other two cover Day 1’s sessions and the opening keynote speech. Below is a recap of the second day’s sessions.
Day 1: Cutting Edge Insights at the EIPC Summer Conference
06/17/2025 | Pete Starkey, I-Connect007The European Institute for the PCB Community (EIPC) Summer Conference took place this year in Edinburgh, Scotland, June 3-4. This is the second of three articles on the conference. The other two cover the keynote speeches and Day 2 of the technical conference. Below is a recap of the first day’s sessions.
Preventing Surface Prep Defects and Ensuring Reliability
06/10/2025 | Marcy LaRont, PCB007 MagazineIn printed circuit board (PCB) fabrication, surface preparation is a critical process that ensures strong adhesion, reliable plating, and long-term product performance. Without proper surface treatment, manufacturers may encounter defects such as delamination, poor solder mask adhesion, and plating failures. This article examines key surface preparation techniques, common defects resulting from improper processes, and real-world case studies that illustrate best practices.