-
- News
- Books
Featured Books
- design007 Magazine
Latest Issues
Current IssueAll About That Route
Most designers favor manual routing, but today's interactive autorouters may be changing designers' minds by allowing users more direct control. In this issue, our expert contributors discuss a variety of manual and autorouting strategies.
Creating the Ideal Data Package
Why is it so difficult to create the ideal data package? Many of these simple errors can be alleviated by paying attention to detail—and knowing what issues to look out for. So, this month, our experts weigh in on the best practices for creating the ideal design data package for your design.
Designing Through the Noise
Our experts discuss the constantly evolving world of RF design, including the many tradeoffs, material considerations, and design tips and techniques that designers and design engineers need to know to succeed in this high-frequency realm.
- Articles
- Columns
- Links
- Media kit
||| MENU - design007 Magazine
Rigid-flex Design Tips and Best Practices
April 10, 2017 | Craig Armenti, Mentor GraphicsEstimated reading time: 1 minute
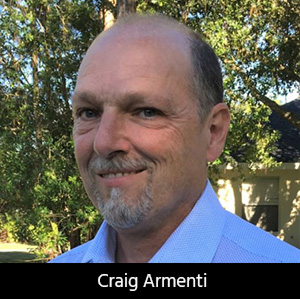
As rigid-flex design becomes commonplace across many industry segments, education on terminology, requirements, processes and best practices are all critical in order to ensure a high probability for first-pass success. As the name indicates, rigid-flex circuits are comprised of a combination of rigid and flexible board technologies. These types of designs consist of multiple layers of flexible circuit substrates attached internally and/or externally to one or more rigid boards.
By combining the advantages of the two technologies, designers have more options when working with dense designs that must conform to a specific form factor. Rigid-flex is a truly enabling technology that lets product development teams cost-efficiently apply greater functionality to a smaller volume of space while at the same time providing the mechanical stability required by most applications.
Prior to the advent of rigid-flex design, when a product required a flex PCB (or multiple flex PCBs), the flex and rigid PCBs were designed separately. Each PCB contained one or more physical connectors in order to assemble the individual boards into a product-level design. In this design methodology, the flex designs were assigned to a specialist who was familiar with stackup and material options along with the best practices and requirements for flex-specific items such as bend regions and stiffeners. There is, after all, a certain science to flex design that, when properly applied, can help ensure first-pass success. While this traditional “design-separately-then-assemble” approach minimized potential issues with the flex portions of the product, it also had several inherent disadvantages. These include the cost associated with the physical connectors; the space required for the physical connectors; the need to properly manage interconnects that have to transition between the separate rigid and flex PCBs (through the connectors); and, of course, the time and cost associated with assembly. The move to the current generation of rigid-flex technology mitigates these issues; however, they are replaced with a different set of challenges and concerns. The good news is these challenges and concerns can be alleviated simply by following some key best practices and guidelines.
To read this entire article, which appeared in the March 2017 issue of The PCB Design Magazine, click here.
Suggested Items
Facing the Future: Time for Real Talk, Early and Often, Between Design and Fabrication
07/08/2025 | Prashant Patel -- Column: Facing the FutureThere has always been a subtle but significant divide between those who design and those who build printed circuit boards. It’s not a hostile gap, but it is a real one, and in today’s high-speed, high-complexity, high-stakes environment, that gap is costing us more than time and yield. It’s costing us innovation.
DownStream Acquisition Fits Siemens’ ‘Left-Shift’ Model
06/26/2025 | Andy Shaughnessy, I-Connect007I recently spoke to DownStream Technologies founder Joe Clark about the company’s acquisition by Siemens. We were later joined by A.J. Incorvaia, Siemens’ senior VP of electronic board systems. Joe discussed how he, Rick Almeida, and Ken Tepper launched the company in the months after 9/11 and how the acquisition came about. A.J. provides some background on the acquisition and explains why the companies’ tools are complementary.
Elementary Mr. Watson: Retro Routers vs. Modern Boards—The Silent Struggle on Your Screen
06/26/2025 | John Watson -- Column: Elementary, Mr. WatsonThere's a story about a young woman preparing a holiday ham. Before putting it in the pan, she cuts off the ends. When asked why, she shrugs and says, "That's how my mom always did it." She asks her mother, who gives the same answer. Eventually, the question reaches Grandma, who laughs and says, "Oh, I only cut the ends off because my pan was too small." This story is a powerful analogy for how many PCB designers approach routing today.
Connect the Dots: The Future of PCB Design and Manufacturing
07/02/2025 | Matt Stevenson -- Column: Connect the DotsFor some time, I have been discussing the increasing complexity of PCBs and how designers can address the constantly evolving design requirements associated with them. My book, "The Printed Circuit Designer’s Guide to… Designing for Reality," details best practices for creating manufacturable boards in a modern production environment.
Siemens Turbocharges Semiconductor and PCB Design Portfolio with Generative and Agentic AI
06/24/2025 | SiemensAt the 2025 Design Automation Conference, Siemens Digital Industries Software today unveiled its AI-enhanced toolset for the EDA design flow.