-
- News
- Books
Featured Books
- smt007 Magazine
Latest Issues
Current IssueIntelligent Test and Inspection
Are you ready to explore the cutting-edge advancements shaping the electronics manufacturing industry? The May 2025 issue of SMT007 Magazine is packed with insights, innovations, and expert perspectives that you won’t want to miss.
Do You Have X-ray Vision?
Has X-ray’s time finally come in electronics manufacturing? Join us in this issue of SMT007 Magazine, where we answer this question and others to bring more efficiency to your bottom line.
IPC APEX EXPO 2025: A Preview
It’s that time again. If you’re going to Anaheim for IPC APEX EXPO 2025, we’ll see you there. In the meantime, consider this issue of SMT007 Magazine to be your golden ticket to planning the show.
- Articles
- Columns
Search Console
- Links
- Media kit
||| MENU - smt007 Magazine
Your In-depth Guide to Reducing Electronics Manufacturing Waste
April 24, 2017 | Danielle Olivier, JJS ManufacturingEstimated reading time: 8 minutes
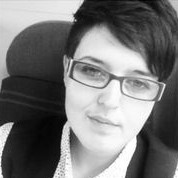
Waste is a common problem within the electronics manufacturing industry. Whether large volumes of faulty smartphones need recalling or small batches of complex PCB assemblies need reworking, waste can be time consuming and costly to rectify.
In essence, waste is a non-value adding process. If left unnoticed, it can damage reputations and, ultimately, lead to businesses becoming uncompetitive. The good news is there are a number of techniques that can help you identify processes that contribute to high volumes of waste.
In this guide, we introduce you to the principles of DMAIC, Six Sigma and Lean manufacturing, so that you can implement a suitable strategy to minimize your waste output.
What is Waste?
Waste can present itself in various formats but, in simple terms, it can be defined as a product or process that causes delay or defect. Keeping within these two categories, and according to Lean principles, waste (or muda) can be split into seven sub-categories:
1. Transport – this doesn't solely relate to the shipping of goods, it can also include other unnecessary transportation – i.e. moving people, products and information to places they don't need to be.
2. Inventory – the storage of parts, products, pieces or documentation awaiting appropriate processing.
3. Motion – people or equipment moving or walking more than is required to perform the processing.
4. Waiting – the downtime caused by waiting for the next production step - for example, during shift changeover or delayed receipt of vital parts.
5. Overproduction – production ahead of demand.
6. Over processing – relying on inspection to catch issues rather than designing the process to eliminate problems upfront.
7. Defects – rework, scrap, incorrect documentation, etc.
It is important to note that these seven categories are not exhaustive. Other forms of waste have been identified, such as manufacturing goods or services that do not meet customer demands or needs and the under-utilization of skills. By identifying these traits within your own manufacturing facility and then implementing suitable process changes, it's possible to start seeing significant reductions in your waste output.
Techniques that can Help You Identify Waste
DMAIC (project management)
DMAIC is a data-driven processing tool that allows you to logically format an issue and plan around its continuous improvement. The tool demands you break down a problem and then adopt a solution in one logical flow. Each point within the acronym stands for a stage within the process. By following the stages chronologically, identifying wasteful processes and implementing improvements soon become accessible and measurable:
- Define the problem, improvement activity, opportunity for improvement, the project goals, and customer (internal and external) requirements.
- Measure process performance.
- Analyze the process to understand the causes of poor performance.
- Improve process performance by addressing and removing the cause.
- Control the improved process and monitor future performance.
Within the measure (M) and analyse (A) stages of a DMAIC project, Lean manufacturing and Six Sigma strategies are generally implemented to gain the best possible outcome. Lean manufacturing is a model armed with tools that aim to simplify and streamline a process in order to eliminate delay. In turn, Six Sigma is a methodology aimed at optimising and stabilising a process in order to eliminate defects.
Six Sigma (Optimizing and Stabilizing a Process)
Six Sigma focuses on optimizing and stabilizing a process in order to minimize defect levels. Some of the tools that encompass this methodology include control charts, Pareto charts and histograms:
Control chart
Control charts are a statistical process control (SPC) tool that are used to show whether or not your manufacturing processes are in a state of control. The graph uses collected quantitative data from a particular process, which is inputted to collate a base line performance. A realistic target line, derived from your current business position and future targets, is then inputted on top of this. It is then possible to see whether the process is reaching, exceeding or failing to meet your businesses targets. If you regularly miss the target it may be worthwhile re-evaluating your current process using one of the process improvement tools highlighted in the next section of this post.
Pareto chart
This data analysis chart combines both bar charts (individual values in descending order) and line graphs (cumulative total) in order to show which variables contribute most to a process issue. By identifying a defect and investigating the data you can then use a Pareto chart to highlight your findings. A Pareto chart can often identify the most common source of defect, or even the highest occurring defect, both of which are likely contributors to a high waste output. By analyzing your data successfully in this way you can look at ways to combat these problems and, ultimately, lower your manufacturing waste.
Histogram
A histogram is a step-column chart that displays a summary of the variations in (frequency distribution of) quantities (called classes) that fall within certain lower and upper limits in a set of data. Like Pareto and control charts, a histogram is another way to display data in order to identify harmful variances within a process that could be increasing your waste levels. Being aware of these analytical tools can help identify triggers of waste within your business and make the improvement process smoother and easier to integrate into production. In turn, they can help lower costs and improve efficiency, while returning your focus back to manufacturing quality products on a consistent basis.
Lean Manufacturing (Simplifying and Streamlining a Process)
5S, spaghetti diagrams and process mapping are all examples of improvement tools that have the primary intention of streamlining and simplifying a process in order to eliminate delay (a key contributor of waste) within your manufacturing process.
5S
The 5S system is an approach to organizing and standardizing an area to ensure it is optimized for maximum efficiency. By following the five steps, derived from the philosophy of Kaizen, it is possible to minimize the amount of waste an area within your manufacturing facility outputs.
The five stages are:
1. Being organized is key to minimizing waste. By sorting the work area and throwing away anything that doesn’t add value, it is easier to notice problems and address them with solutions.
Page 1 of 2
Suggested Items
Real Time with... IPC APEX EXPO 2025: Technica's Innovations and Partnerships
04/11/2025 | Real Time with...IPC APEX EXPOJason Perry of Technica USA and Robert Beber of Reeco share about the engagement at their extra-large booth at this year's show, where they showcased 11 pieces of equipment and announced the new partnership for Technica with Reeco, supplier of ESD clothing and workbenches. With a positive industry outlook despite global trade uncertainties, Technica has plans to expand in North America.
BEST Inc. Presents StencilQuik for Simplifying BGA Rework Challenges
04/02/2025 | BEST Inc.BEST Inc., a leader in electronic component rework services, training, and rework tools is thrilled to announce StencilQuik™ rework stencils. This innovative product is specifically designed for placing Ball Grid Arrays (BGAs) or Chip Scale Packages (CSPs) during the rework process.
MacDermid Alpha Introduces Reworkable Edgebond for High-Reliability Electronics
02/06/2025 | MacDermid Alpha Electronics SolutionsIn an era where high-performance and sustainable manufacturing practices are crucial, MacDermid Alpha Electronics Solutions is redefining industry standards with the launch of ALPHA® HiTech® CF31-4026.
PDR Offers Advanced Infrared Heating Technology for BGA Rework
12/02/2024 | PDRPDR Americas is proud to highlight its industry-leading solutions for BGA and SMT rework. As a trusted partner in electronics manufacturing, PDR’s rework stations deliver precision, reliability, and simplicity, setting a new standard for addressing the challenges of modern rework applications.
Winners of IPC Hand Soldering and Rework Competition Vietnam 2024 Announced
09/19/2024 | IPCIn conjunction with NEPCON Vietnam 2024, IPC hosted its popular IPC Hand Soldering and Rework Competition in Hanoi, Vietnam, September 11-13. Thirty-nine competitors from 16 electronics companies and one university in Vietnam vied for top honors.