-
- News
- Books
Featured Books
- pcb007 Magazine
Latest Issues
Current IssueThe Hole Truth: Via Integrity in an HDI World
From the drilled hole to registration across multiple sequential lamination cycles, to the quality of your copper plating, via reliability in an HDI world is becoming an ever-greater challenge. This month we look at “The Hole Truth,” from creating the “perfect” via to how you can assure via quality and reliability, the first time, every time.
In Pursuit of Perfection: Defect Reduction
For bare PCB board fabrication, defect reduction is a critical aspect of a company's bottom line profitability. In this issue, we examine how imaging, etching, and plating processes can provide information and insight into reducing defects and increasing yields.
Voices of the Industry
We take the pulse of the PCB industry by sharing insights from leading fabricators and suppliers in this month's issue. We've gathered their thoughts on the new U.S. administration, spending, the war in Ukraine, and their most pressing needs. It’s an eye-opening and enlightening look behind the curtain.
- Articles
- Columns
- Links
- Media kit
||| MENU - pcb007 Magazine
Estimated reading time: 2 minutes
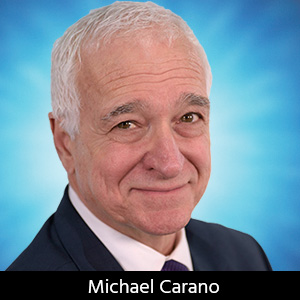
Contact Columnist Form
Trouble in Your Tank: Copper-to-Copper Peeling
Introduction
Yes, it is annoying, even critical. Your customer returns product to you complaining about poor adhesion of plated copper to the surface. So what is the genesis of this defect? Is it electroless copper peeling from base laminate copper? Or is it electrolytic copper peeling from the electroless copper? One can experience copper peelers in pattern plating, panel plating or in electroless copper. Peeling can be seen on the conductors, within the PTH or in the microvias.
Thermal excursions will exacerbate the problem as thermal stresses will increase the opportunity for one layer of copper to separate from another. As is often the case, separation of the copper from the post interconnect (aka interconnect defect) is considered peeling. However, I have presented ICD issues in previous columns, so this month the focus is on copper-to-copper peelers.
Electroless Copper Peeling
First, one must consider achieving good electroless copper-to-copper foil adhesion. One must start with a copper foil surface that is free from oxides, soil greases and other organic materials. In addition, a micro-etching solution, whether it be persulfate or peroxide-sulfuric acid-based, should be used to ensure a clean and active copper surface that will provide sufficient surface roughness to promote and enhance adhesion of the copper to the surface. Not to be forgotten is the need to get solid bond of the electroless copper to the innerlayer copper (post-innerconnect) and to the capture pad of a blind via.
In previous columns, I described several reasons that electroless copper could separate from the foil copper, copper interconnect and/ or copper capture pad. One such cause is the use of a particular type of cleaner-conditioner prior to the electroless copper deposition process. Some of these chemicals, while helping to promote strong palladium catalyst adsorption to the surface, may also leave a surfactant-like film on the copper. This film in turn will act as an adhesion barrier, causing the copper plated deposit to peel from the foil copper. One suggestion is to carefully evaluate any cleaner-conditioner to ensure compatibility with the electroless copper.
There are other possibilities that would lead to this type of adhesion failure. One such failure mechanism is related to resin smear remaining on the capture pad of a blind via. Figure 1 shows significant blistering of the copper from the blind via capture pad most likely due to resin. One way to fix this issue is to design the laser process to ablate the resin material down to the capture pad. Even with this scenario, the concern with UV YAG is that once the beam reaches the copper pad, the energy is “stepped down” to minimize further attack on the copper pad. This can lead to resin and ablated byproducts to remain on parts of the pad. In turn this provides a mechanism for adhesion failure. Any remaining resin material can act as a fulcrum, forcing the plated copper to peel.
To read the full version of this column which originally appeared in the April 2017 issue of The PCB Magazine, click here.
More Columns from Trouble in Your Tank
Trouble in Your Tank: Yield Improvement and ReliabilityTrouble in Your Tank: Causes of Plating Voids, Pre-electroless Copper
Trouble in Your Tank: Organic Addition Agents in Electrolytic Copper Plating
Trouble in Your Tank: Interconnect Defect—The Three Degrees of Separation
Trouble in Your Tank: Things You Can Do for Better Wet Process Control
Trouble in Your Tank: Processes to Support IC Substrates and Advanced Packaging, Part 5
Trouble in Your Tank: Materials for PWB Fabrication—Drillability and Metallization
Trouble in Your Tank: Supporting IC Substrates and Advanced Packaging, Part 5