-
- News
- Books
Featured Books
- design007 Magazine
Latest Issues
Current IssueAll About That Route
Most designers favor manual routing, but today's interactive autorouters may be changing designers' minds by allowing users more direct control. In this issue, our expert contributors discuss a variety of manual and autorouting strategies.
Creating the Ideal Data Package
Why is it so difficult to create the ideal data package? Many of these simple errors can be alleviated by paying attention to detail—and knowing what issues to look out for. So, this month, our experts weigh in on the best practices for creating the ideal design data package for your design.
Designing Through the Noise
Our experts discuss the constantly evolving world of RF design, including the many tradeoffs, material considerations, and design tips and techniques that designers and design engineers need to know to succeed in this high-frequency realm.
- Articles
- Columns
- Links
- Media kit
||| MENU - design007 Magazine
Predictive Engineering: Happy Holden Discusses True DFM
October 4, 2017 | Andy Shaughnessy, PCBDesign007Estimated reading time: 2 minutes
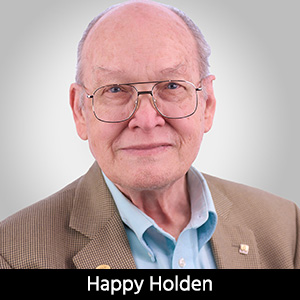
Happy Holden has been involved in DFM for over 45 years, since he first started working at HP and optimized their PCB design and manufacturing processes. Naturally, for this issue, Barry Matties and Andy Shaughnessy made it a priority to get Happy’s thoughts on DFM, and what true DFM entails.
Andy Shaughnessy: Happy, why don’t you start by telling us about your position on DFM, and why true DFM, to you, means that PCB designers and engineers should utilize predictive engineering.
Happy Holden: If you use the term “predictive engineering,” you're not going to get much recognition, because that's a term I use. What most people consider design for manufacturing, or DFX, is software that finds errors in design. Especially in CAM tooling put out by Valor, if a manufacturer puts in his design builds in a minimum, then the DFX software scans through that and finds what’s cautionary and that all requirements are met. That's all done after the fact.
For me, DFM was introduced when HP took up DFM. It was kind of invented by Professors Peter Dewhurst and Geoffrey Boothroyd. Anyway, DFM and DFMA (design for manufacturing and assembly) were really invented by these two American professors in New England. They wrote a book about it, Product Design for Manufacture & Assembly. It later became software.
Their whole philosophy centered on ways to figure out how to do it right the first time. Their book is about the nature of performance during design that allow you to decide if this is going to be easy to assemble. I think the more important component, that Hitachi and the Japanese took it up, was whether the product could be built by automation? That's really significant what Hitachi did with the philosophy. They not only took the ‘do it right the first time’ approach but then asked how they could do it simple enough that robots and automation can build it? The Japanese did this because they wanted to build all these first-generation products in a building next door in Japan and not ship it offshore like Americans were doing.
Contrast that with Apple Inc. Apple designs products that are impossible to automate. They're so complex. They're really fanciful, but they have to be built by human hands. You've got 86,000 17-year-old teenage girls in Shenzhen building these Apple products. Foxconn put up money to install 1 million robots to replace these girls. Today only about 400 robots have been installed out of that 1 million, because they found out the products they're building for the Americans can’t be automated.
I refer to DFM as being designed for manufacturing the first time. We're not just designing it, running software, finding the errors, going back, redesigning it, checking again, going back and re-spinning it, until it works. I'm alone in this definition unless you happen to be knowledgeable about Dewhurst and Boothroyd, which most people in printed circuits aren't.
To read this entire article, which appeared in the September 2017 issue of The PCB Design Magazine, click here.
Suggested Items
LITEON Technology Reports Consolidated June Sales of NT$13.6 Billion, Up 16% Y-o-Y
07/08/2025 | LITEON TechnologyLITEON Technology reported its June consolidated revenue of NT$13.6 billion. Thanks to the growth from power management in cloud computing, advanced server, and networking, the revenue is up 2% M-o-M, 16% Y-o-Y. The cumulative sales for January to June totaled NT$76.8 billion, up 24%, Y-o-Y.
Inside Aimtron’s Cross-border EMS Strategy
07/08/2025 | Nolan Johnson, SMT007 MagazineMukesh Vasani immigrated from a very small farming village in India to the U.S. in 1995 as a civil engineer. After shifting into electronics, Mukesh built his Chicago-based company, Aimtron, into a successful enterprise by combining quality with competitive pricing. He leveraged his roots in India to expand manufacturing without compromising on quality.
Be the Partner Engineers Can Rely On
07/08/2025 | Nolan Johnson, SMT007 MagazineGreen Circuits’ unique niche in the electronics manufacturing industry comes partly from its location in Silicon Valley, but also from its specialty of serving up quick-turn prototypes and low-volume work with high-complexity production. In this conversation, CEO Michael Hinshaw emphasizes the value of end-to-end services, especially while the pace of R&D development is accelerating amidst a growing demand for complexity across industries.
Electronics Industry Wrestles with Cost Pressures and Weaker Profitability
07/07/2025 | Global Electronics AssociationElectronics manufacturers are facing rising material and labor costs according to the Global Electronics Association’s June Sentiment of the Global Electronics Manufacturing Supply Chain Report.
Naprotek Appoints James Eisenhaure as Chief Financial Officer
07/07/2025 | Naprotek LLCNaprotek, LLC, a leading provider of mission-critical electronics technology solutions, today announced that James Eisenhaure has been appointed Chief Financial Officer, effective June 30. Eisenhaure has been serving as interim CFO since earlier this year and now formally steps into the role.