-
- News
- Books
Featured Books
- design007 Magazine
Latest Issues
Current IssueProper Floor Planning
Floor planning decisions can make or break performance, manufacturability, and timelines. This month’s contributors weigh in with their best practices for proper floor planning and specific strategies to get it right.
Showing Some Constraint
A strong design constraint strategy carefully balances a wide range of electrical and manufacturing trade-offs. This month, we explore the key requirements, common challenges, and best practices behind building an effective constraint strategy.
All About That Route
Most designers favor manual routing, but today's interactive autorouters may be changing designers' minds by allowing users more direct control. In this issue, our expert contributors discuss a variety of manual and autorouting strategies.
- Articles
- Columns
- Links
- Media kit
||| MENU - design007 Magazine
Cannonballs, eBooks, and Signal Integrity
December 4, 2017 | Andy Shaughnessy and Pete Starkey, I-Connect007Estimated reading time: 12 minutes
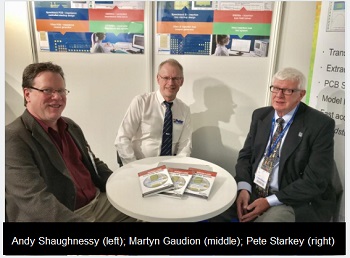
I-Connect007 editors Andy Shaughnessy and Pete Starkey recently met with Polar Instruments Managing Director Martyn Gaudion at productronica. They discussed the success of his recent book The Printed Circuit Designer’s Guide to…Secrets of High-Speed PCBs, Part 2, the ongoing challenge of facilitating communication between designers and fabricators, and the influence of chemical bond-enhancement processes on insertion loss.
Andy Shaughnessy: I’m here with our European editor, Pete Starkey. We're here in the Polar Instruments booth at productronica, and happy to have the opportunity to spend a few minutes with Martyn Gaudion. Martyn, it’s good to see you again. Why don't you give us a brief background on the company and we'll go from there.
Martyn Gaudion: It's great to be back at productronica and to meet you two guys again. Polar’s name is synonymous with PCB signal integrity, specifically with impedance control, but increasingly with PCB insertion loss. On the subject of insertion loss, we've developed an increasingly strong relationship with laminate suppliers, and being here at productronica this year gives us the opportunity for first-hand contact with all the laminate suppliers who provide us with materials information for the database that backs up all of our toolsets. So it's a really good place to be meeting up.
Shaughnessy: And there’s a lot of interest in your eBook as well. You're a best-selling author now!
Gaudion: Maybe not best-selling, but selling anyway! It's actually a non-salesy book full of really down-to-earth information that's a distillation of everything I've learned and Polar's learned over the last 25 years supporting the PCB fabrication industry. Also, it helps designers to be realistic in their designs and not overzealous in their expectations, and that's really what the book's all about.
We've just finished mailing the hard copy version to all of our customers, and some have come back and bought more. So we're thrilled with that. And we've had customers who have bought books for all of their sales force, and that’s a very pleasant surprise.
Shaughnessy: So there is a real thirst for the knowledge among PCB designers?
Gaudion: Yes. The series of books is really good because it's basically I-Connect007's idea, and I bought a copy of the flex book and that's taught me loads of stuff about flex. So, I recommend anybody who wants to dip into a new subject and get a really instant feel for a subject, the Printed Circuit Board Designer's Guide is an excellent series of books that will get you started on a new subject. So not only my book, but other people’s too.
Shaughnessy: Where are the designers most lacking, would you say, as far as information goes?
Gaudion: I was at a seminar in Munich a couple of weeks ago with Pete and it was clear that designers are lacking in their knowledge of the PCB fabrication industry. As you push the frequencies up and up, and the power levels go up, it's really important for the designers to have an understanding of how their PCBs are fabricated.
So I would really recommend that every designer gets at least one chance to get on a tour of a PCB fabricator because it's surprising to me how many designers have no idea how PCB is fabricated and that has real impact on the costs and reliability of your finished product when you come to actually turn your design into reality.
Shaughnessy: That's one thing that Pete has been saying over the years. Many designers have only maybe been to a board shop 25 years ago, or never. I've talked to designers who have never seen one.
Pete Starkey: I think of more recent times that barrier between design and fabrication has probably become lower and lower. It’s still there to some extent, but the software specialists who understand both sides of the story are increasingly able to provide tools that make life easier for guys on both sides.
Gaudion: Yes. In one area at the moment: everyone's pushing for higher frequency, and everybody thinks about the loss tangent of the laminate, but actually coming into play is the roughness of the copper. And again, you can get the best copper foil from your foil supplier, but you do have to realize that any layer that's got a drill end is going to be plated and so the roughness is determined by the fabrication process and not by the copper supplier.
So those are the kind of things that designers can maybe slip into thinking, "I'm going to specify this kind of foil," but you have to think, "Is that a layer where a drill ends?" Those kinds of things could have an impact on your signal integrity. So, you can end up paying more than you need to pay or not getting the specs you'd expect if you don't understand the way the PCB is put together.
Shaughnessy: What are some of the trends you see as you're presenting?
Gaudion: Everybody's starting to use electronics in applications that we wouldn’t have expected, in automotive, autonomous cars, drones, that kind of technology - there's electronics appearing everywhere. We're speaking to customers that we would never have had as customers in the past. We see a lot of automotive business heading our way where people didn't used to use high-speed boards, but now they do. And automotive won’t be able to treat PCBs as just a commodity as they're used to, because you need to understand how the board is put together if it's going to perform properly.
Shaughnessy: Even pharmaceutical companies now have circuit board designers.
Gaudion: Yes, exactly. Here at productronica, certainly we've seen an increase in demand and interest in insertion loss and that's a repeated thing. Back in the day when Polar started working on impedance, our test system, our favorite old CITS, has been going for 25 years. We started by testing impedance; modelling followed several years later and our modelling business grew. When we look at the insertion loss business, we've seen the modelling lead the testing by around ten years. So we've been selling modelling software, and our customers need modelling software, and it's really only these last 12 months we've started to see in increase in uptake in test.
One of the challenges for us is that there are many, many different methods of measuring insertion loss. With impedance, the industry settled on one technique very quickly, but for insertion loss there are several different methods all championed by the different OEMs. That makes the life for the fabricator more challenging, because, which piece of equipment should I buy? Which methods should I use? I'm sure the industry will gradually converge on a method, but at the moment there's SPP, which was really promoted by IBM. There's SET2DIL, which was promoted by Intel and now Delta-L promoted by Intel and a number of other different methods for insertion loss.
So we've integrated all those methods into our tools and what we do, and it's something that Eric Bogatin often recommends, is bring the data from the insertion loss testers directly into our modelling software. Then you can contrast the measure with the model to sanity-check if what you've made is actually what you thought you designed.
Shaughnessy: As you mention in your books, what happens if what you measured isn't what you thought you designed?
Gaudion: Yes. With copper roughness, some of the techniques for modelling copper roughness date back from the 1930s, 1940s, from the early days of radar. They were looking at the machining marks on wave guides. They kind of worked for 30 or 40 years, and now there are some new methods like the Huray method. But the Huray method is being quite tricky in terms of the data you need to feed into it. So we've struck up a very good relationship with Bert Simonovich, and he has provided us with the maths to take the Rz value, which is very commonly available in the fabricating community. We plan to put Rz into the tool, and convert it into the input data for Huray using a method called the canonball stack, and then you can get your insertion loss roughness compensation correlated up to around 45 GHz. So really, really big steps forward.
Page 1 of 2
Testimonial
"The I-Connect007 team is outstanding—kind, responsive, and a true marketing partner. Their design team created fresh, eye-catching ads, and their editorial support polished our content to let our brand shine. Thank you all! "
Sweeney Ng - CEE PCBSuggested Items
Trouble in Your Tank: Minimizing Small-via Defects for High-reliability PCBs
08/27/2025 | Michael Carano -- Column: Trouble in Your TankTo quote the comedian Stephen Wright, “If at first you don’t succeed, then skydiving is not for you.” That can be the battle cry when you find that only small-diameter vias are exhibiting voids. Why are small holes more prone to voids than larger vias when processed through electroless copper? There are several reasons.
The Government Circuit: Navigating New Trade Headwinds and New Partnerships
08/25/2025 | Chris Mitchell -- Column: The Government CircuitAs global trade winds continue to howl, the electronics manufacturing industry finds itself at a critical juncture. After months of warnings, the U.S. Government has implemented a broad array of tariff increases, with fresh duties hitting copper-based products, semiconductors, and imports from many nations. On the positive side, tentative trade agreements with Europe, China, Japan, and other nations are providing at least some clarity and counterbalance.
How Good Design Enables Sustainable PCBs
08/21/2025 | Gerry Partida, Summit InterconnectSustainability has become a key focus for PCB companies seeking to reduce waste, conserve energy, and optimize resources. While many discussions on sustainability center around materials or energy-efficient processes, PCB design is an often overlooked factor that lies at the heart of manufacturing. Good design practices, especially those based on established IPC standards, play a central role in enabling sustainable PCB production. By ensuring designs are manufacturable and reliable, engineers can significantly reduce the environmental impact of their products.
50% Copper Tariffs, 100% Chip Uncertainty, and a Truce
08/19/2025 | Andy Shaughnessy, I-Connect007If you’re like me, tariffs were not on your radar screen until a few months ago, but now political rhetoric has turned to presidential action. Tariffs are front-page news with major developments coming directly from the Oval Office. These are not typical times. President Donald Trump campaigned on tariff reform, and he’s now busy revamping America’s tariff policy.
Global PCB Connections: Understanding the General Fabrication Process—A Designer’s Hidden Advantage
08/14/2025 | Markus Voeltz -- Column: Global PCB ConnectionsDesigners don’t need to become fabricators, but understanding the basics of PCB fabrication can save you time, money, and frustration. The more you understand what’s happening on the shop floor, the better you’ll be able to prevent downstream issues. As you move into more advanced designs like HDI, flex circuits, stacked vias, and embedded components, this foundational knowledge becomes even more critical. Remember: the fabricator is your partner.