-
- News
- Books
Featured Books
- design007 Magazine
Latest Issues
Current IssueAll About That Route
Most designers favor manual routing, but today's interactive autorouters may be changing designers' minds by allowing users more direct control. In this issue, our expert contributors discuss a variety of manual and autorouting strategies.
Creating the Ideal Data Package
Why is it so difficult to create the ideal data package? Many of these simple errors can be alleviated by paying attention to detail—and knowing what issues to look out for. So, this month, our experts weigh in on the best practices for creating the ideal design data package for your design.
Designing Through the Noise
Our experts discuss the constantly evolving world of RF design, including the many tradeoffs, material considerations, and design tips and techniques that designers and design engineers need to know to succeed in this high-frequency realm.
- Articles
- Columns
- Links
- Media kit
||| MENU - design007 Magazine
Heat Transfer and Thermal Conductivity: The Facts
December 26, 2017 | Jade Bridges, ElectrolubeEstimated reading time: 2 minutes
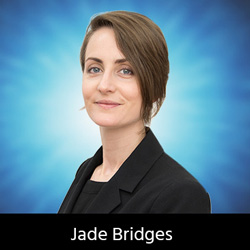
In my first two columns in this series, I presented a broad introduction to the subject of thermal management of electronic circuits. I hope my “quick start guide” and “problems and solutions” items have sparked readers’ interest in this elemental but essential aspect of electronic system design.
This month I’m taking a closer look at thermal interface materials—how they can be applied to achieve efficient heat transfer, and the significance of bulk thermal conductivity in relation to heat transfer and thermal resistance. I’ll also be touching on the influence that product miniaturisation is having on thermal management techniques, and I will return to this recurring question: Why do I have to spread my thermal interface material so thinly?
As in previous columns, my approach will be based on the frequently asked questions that our customer support teams field every day on the phone, at exhibitions and when visiting customer premises. I've selected five of the most common questions, followed by their respective responses, and I hope they offer useful guidance for readers who may be experiencing design problems related to achieving a satisfactory heat transfer performance in their electronic assemblies.
What would be your top suggestions for achieving the most efficient heat transfer?
First and foremost, read the thermal interface material manufacturer’s advice about optimum application methods. They’ve been around the block a few times and they know what they’re talking about! Remember, more is not necessarily better; uniform and thin applications of the heat transfer medium always work best. Most products are likely to have an optimum thickness of application, as determined by the manufacturer, and you should try to achieve this for best results.
It is important to understand your application. What are the environmental conditions under which it must operate, and how variable are they? Will the chosen heat transfer compound perform consistently as environmental conditions swing from one extreme to the other? Consider the heat sink; is this the actual casing surrounding the assembly or a separate heat sink placed on top of a component? Where cases are concerned, is there a gap between the case and the component?
What key issues must be considered when trying to achieve efficient heat transfer?
Again, think variability of environmental conditions. Just because the heat transfer is efficient under standard ambient conditions, doesn’t mean that it will remain stable over the lifetime of the product. Accelerated testing might be able to reveal related design issues; however, in-application testing is more likely to provide definitive information about the long-term performance of heat transfer materials.
Application of the heat transfer compound will depend on the type of interface or gap filling material being used. These compounds provide a medium for improving the conditions under which heat transfer takes place and thereby maximise its efficiency. Compounds should not be applied in excess amounts in the belief that they will achieve the thermal conductivity of a solid metal heat sink.
To read this entire column, which appeared in the November 2017 issue of The PCB Design Magazine, click here.
Suggested Items
Fresh PCB Concepts: Assembly Challenges with Micro Components and Standard Solder Mask Practices
06/26/2025 | Team NCAB -- Column: Fresh PCB ConceptsMicro components have redefined what is possible in PCB design. With package sizes like 01005 and 0201 becoming more common in high-density layouts, designers are now expected to pack more performance into smaller spaces than ever before. While these advancements support miniaturization and functionality, they introduce new assembly challenges, particularly with traditional solder mask and legend application processes.
Knocking Down the Bone Pile: Tin Whisker Mitigation in Aerospace Applications, Part 3
06/25/2025 | Nash Bell -- Column: Knocking Down the Bone PileTin whiskers are slender, hair-like metallic growths that can develop on the surface of tin-plated electronic components. Typically measuring a few micrometers in diameter and growing several millimeters in length, they form through an electrochemical process influenced by environmental factors such as temperature variations, mechanical or compressive stress, and the aging of solder alloys.
Insulectro & Dupont Host Technology Symposium at Silicon Valley Technology Center June 25
06/22/2025 | InsulectroInsulectro, the largest distributor of materials for use in the manufacture of PCBs and printed electronics, and DuPont, a major manufacturer of flex laminates and chemistry, invite fabricators, OEMS, designers, and engineers to attend an Innovation Symposium – Unlock the Power - this Wednesday, June 25, at DuPont’s Silicon Valley Technology Center in Sunnyvale, CA.
MVTec, Siemens Expand Technological Cooperation
06/12/2025 | MVTecMVTec Software GmbH and Siemens are expanding their technological cooperation in the field of industrial automation. To reinforce their increasingly close collaboration, Siemens joined the MVTec Technology Partner Program in May 2025.
Nordson Electronics Solutions Develops Panel-level Packaging Solution for Powertech Technology, Inc. That Achieves Yields Greater Than 99% for Underfilling During Semiconductor Manufacturing
06/11/2025 | Nordson Electronics SolutionsNordson Electronics Solutions, a global leader in reliable electronics manufacturing technologies, has developed several solutions for panel-level packaging (PLP) during semiconductor manufacturing. In one particular case, Nordson’s customer, Powertech Technology, Inc. (PTI) saw underfill yields improve to greater than 99% as they plan to transition from wafers to panels in their manufacturing operations. edwd